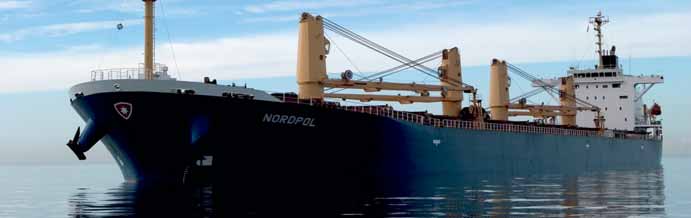
Cleveland Cascades Ltd. dedicated to solving dust problems globally
Cleveland Cascades Ltd is a world leader in the design and manufacture of bespoke loading chutes for the handling of dry bulk materials.
Having achieved awards for environmental engineering, environmental achievement and export achievement, Cleveland Cascades Ltd (CCL) uses its unique Cascade system to tackle the problem of dust.
Based in the UK, the company employs the original inventors of the ‘Cleveland Cascade’ system together with a dedicated team of experts in design, manufacture, assembly and commissioning.
With over 700 systems operating worldwide with applications in ship, silo, road, rail and tanker loading the company’s key to success is its proven ability to provide a well engineered solution with professional and committed support.
In addition to the company’s patented ‘Cascade Chute’, CCL also manufactures conventional telescopic free-fall chutes for applications where they are a requirement, such as for damp and sticky materials, or non-dusty materials. Vehicle loading applications such as truck, tanker, and rail wagon loaders are also provided.
Since becoming a private company in 2005, CCL has grown over four times in size, both in terms of turnover and staffing. This rapid yearly growth is due to a consistent approach of manufacturing quality products and turning each new customer into a regular customer. CCL loading chutes are used on every continent, and in almost every country of the world handling a vast variety of dry bulk materials, from large lump Iron ore and coal, to fine powders such as soda ash, phosphate and alumina.
More recently, the CCL ‘Cascade Chute’ has been used to effectively handle biomass at large quantities. The renewable energy source is particularly dusty when handling due to its formation of compressed wood fines, and due to its organic nature this dust can be potentially explosive. By specifying the optimum handling system, and also components that are classified to operate in its particular environment, CCL is fast becoming the solution to the industry’s biomass handling needs. To date, CCL have supplied systems for loading into trucks, silos and also ships at varied rates. By engineering the exact system to suit each customer’s requirements has resulted in systems capable of handling biomass with significantly reduced dust emissions, whilst also maintaining the quality of the product.
The most recent biomass project for CCL has seen two more truck loading systems delivered to the growing biomass operation at Port of Tyne in South Shields. This latest order now sees six CCL systems in operation at the Port, each handling biomass at rates of up to 600tph (tonnes per hour).
CCL’s customers to date include ThyssenKrupp, TAIM Weser, FL Smidth, FAM, SMB, Sandvik, Cargotec, BHP, PHB,Tenova, Telestack, BRUKS Rockwood, Odebrecht,Texas International Terminals,TRIO Engineered Products and many more.
Recent projects include a Cascade system in Japan to handle cement clinker. The shiploader, attached to a luffing boom, will handle the clinker at rates of up to 650tph. Another project is the manufacture of two telescopic tubular chutes that have been despatched to Brazil. These systems will handle soyabean at eventual rates of 2,000tph.
CCL approaches every project with the same attention to detail, thorough engineering process and high standards of quality, believing that every system produced is a direct reflection of the company and the best possible form of advertisement to potential new customers.
CCL are also implementing new products and product developments to the current product range such as the new, patent pending ‘Cascade VariFlow’ chute which represents the second generation Cascade chute, with the ability to automatically adjust cone inclination during loading to ensure absolute minimal dust emissions at all times, regardless of fluctuations in product feed rate. The ‘VariFlow’ can also be used to handle multiple products through the same chute more effectively than the original Cascade.
In addition to the VariFlow, CCL have also developed and supplied Cascade transfer chutes to solve the dust emissions problem created at conveyor transfer points. This represents a logical step for CCL, as for years we have provided the means for materials loading from conveyor to receptor, ship, rail wagon or tanker etc.And so now we are providing materials loading in the same controlled manner between two conveyor belts.
The transfer chutes combine existing Cascade and materials flow technology and experience with innovative design and engineering solutions. The Cascade transfer chutes are able to work between belts positioned at 90° to one another, inclined belts, and also height adjustable belts.The chutes are lined in hard wearing materials such as ceramic tiles, stainless steel, or UHMW (ultra high molecular weight) plastics to ensure effective resistance to abrasive wear from the materials handled. The transfer chutes also use an outlet which presents material onto the belt in its natural profile, creating maintenance free and dust free delivery onto the belt.
In addition to developing new products, CCL also look to improve its current ranges where possible. More recently, the requirement for equipment to be as light as possible in terms of weight has become more and more prominent. In an effort to deliver the exceptional quality that CCL is renowned for, but also be able to offer these systems with an effective weight saving, CCL has moved to offer GRP fibreglass cones in its Free Fall system range. Where originally steel would be used to manufacture the cones, CCL have found that, with some materials a weight-saving of up to and over 50% can be achieved by switching to GRP fibreglass cones with a suitable liner for the product being handled. The most recent project where this has been offered is for three loading chutes for operation in the Ukrainian Port of Illichevsk. Each system is 30 metres in length; therefore the weight-saving by utilizing the GRP cones has been hugely significant.
Cleveland Cascades Ltd hopes to remain at the forefront of innovative design within the bulk industry, taking its technology and experience and applying it where possible to solve dust and material degradation issues.
With this ethos of continual improvement and expansion, CCL hopes to further develop itself into a well established figure within the bulk industry.
Eka Bulk Handling Software Solutions for Efficient Commodity Management
Eka provides smart commodity management software solutions. Eka’s analytics-driven, end-to-end Commodity Management platform enables companies to efficiently and profitably meet the challenges of complex and volatile markets.
The company’s best-of-breed solutions manage commodity trading, procurement, logistics, storage and handling, processing, enterprise risk, and compliance. Eka partners with customers to accelerate growth, increase profitability, improve operational control, and manage risks and exposures.
Through its acquisition of MatrixGroup in 2013, Eka now also provides process management, task execution, and business intelligence systems tailored for the bulk handling industry including mining operations, grain facilities, and export terminals for all types of commodities.
Ninetye-five per cent of the grain exported out of Australia is through Eka’s platform.
With Eka’s software platform, customers’ physical assets (machinery, storage locations, ports, etc.) operate at maximum efficiency in the storage or movement of physical bulk commodities – giving them the most throughput for the least amount of downtime and cost.
With Eka’s bulk handling software platform, customers can effectively manage their sites and save money:
- Automate process decisions
- Improve utilization of plant assets
- Gain real time visibility into all operations
EKA’S BULK HANDLING PRODUCT PORTFOLIO INCLUDES:
- Eka.Bulk Handling: An end-to-end solution to manage the physical processing of raw materials such as coal, iron ore, and grain in mining operations, grain facilities, and export terminals.
- Eka.Site Automation: A dynamic plant management and control tool, incorporating high level process planning, scheduling, task execution and product tracking.
- Eka.Anti Collision: 3D modelling of mobile machines and structures providing precise position to prevent collisions.
- Eka.3D Stockpile Manager: 3D model of stockyard, including quality, for better stacking and reclaiming decisions.
- Eka.Commodity Site Manager: Physical operations management of bulk commodity handling sites including stock, cargo receipt, shipment, and billing.
Eka’s software platform consists of proven machine control code, dynamic plant representation, and comprehensive reporting packages, all within an advanced architecture running on industry standard hardware platforms. Key benefits of the software include:
- Ability to improve operational awareness and control – Through real time product tracking and smart sequence control.
- Well-suited functionality – Modular and scalable nature of the product allows systems to be implemented in increments targeting specific areas that are required at the time.Then permits future expansion of software modules as suited to your needs.
- Better utilization of plant assets – Using smart sequence control options allowing common plant to remain running.
- Faster tasks — Dynamic user interface displays the information relevant to the current production activities.
- Anti-contamination — Advanced anti-contamination control that does not allow mixing of incompatible products at any stage, from task planning through to execution.
- Better evaluation of causes of downtime — Delay accounting captures all delays and, where possible, analyzes and assigns reasons for these delays.
- Real time visibility into all operations — Comprehensive reporting suite provides complete reporting of operations and productivity, equipment usage, tonnes passed over equipment, run hours, inventory, quality management, and maintenance reports.
With Eka’s configurable commodity handling and management software platform, customers can streamline their commodity handling processes to decrease costs and maximize profits.
ABOUT EKA
Eka is a team of 400+ staff with offices in Asia, Australia, Europe and the Americas, serving a rapidly growing global client base across multiple commodity segments.
Inspectorate sets up new facility at Immingham
A new coal sample preparation facility has been set up at HIT in Immingham by Inspectorate.
Inspectorate is a wholly owned subsidiary of Bureau Veritas, one of the world’s leading independent testing, inspection and certification companies.
The sampling and preparation will be fully consistent with ISO 18283:2006.
The new facility, staffed by Inspectorate employees, opened in February and is equipped with two QHS Hammermill crushers, a Retch SR300 Rotormill, drying ovens, and Gilson riffle dividers. From the initial bulk sample of several tonnes, the facility can rapidly produce representative laboratory samples of <0.2mm to test the coal quality for its customers.
Inspectorate believes that the on-site capability will help reduce turnaround times for proximate analysis significantly. This will be a major benefit to customers who need initial constituent readings before the material can be used to maximum efficiency.
Erwin Oosterveen, Inspectorate’s Solid Fuels Business Development Manager for the UK and Northern Europe, said:“This major new development in on-site sampling should be tremendously helpful to the industry. It’s a one-stop shop for the energy industry that is convenient and quick. And that’s all backed up by the accuracy of testing and analysis for which Inspectorate International is renowned.
“Our new Immingham facility complements Inspectorate’s (and its parent company Bureau Veritas’), existing large global network of coal and solid fuels sampling and testing facilities, which includes the USA, Canada, Russia, Colombia and South Africa. The facility means we can now offer an end-to-end service to clients importing these products into the UK.
“In time we can see the facilities we offer being extended to cater for more industry needs. Our main aim now, however, is to make sure that the new service gets off to a flying start. We are confident that it will and look forward to proving ourselves to clients.”
Inspectorate is part of the Bureau Veritas Commodities Division. Bureau Veritas acquired Inspectorate in 2010, making it one of the world leaders in commodities inspection and testing. Inspectorate is the core of Bureau Veritas’ Commodities Division. Its customers can look forward to continued expertise and excellent customer service, supported by a global network and a brand name synonymous with quality, professionalism and integrity.
GUARDIAN anti-piracy barriers go from strength to strength in 2014
Following on from the proven success of the product over the last 12 months, the GUARDIANTM brand of anti-piracy barriers restructures under a new company name.
With immediate effect, GUARDIAN will now be provided by Guardian Maritime Limited.
In taking their whole operation back in- house the original inventors and owners, David and Teresa Stevens, plan to further expand the company, adding to the team and increasing worldwide representation as well as further developing a range of additional anti-piracy products. The team has already expanded with the addition of Jean Winfield as its new Marketing Director. She has more than 20 years’ experience in PR & marketing, with the last 15 years being specifically in maritime having been involved with many shipping companies and events across the globe. She joins Guardian Maritime’s board having already worked with the company through her PR & marketing company Jeanius Consulting and is delighted to take on the new additional role.
“From the very first time I saw GUARDIAN I knew it was both a product and a company I would like to work with, a company passionate about tackling piracy and safeguarding seafarers. I am looking forward to working with the sales team to promote and extend GUARDIAN’s reach, continuing to provide ships with both a highly visual deterrent as well as a practical and cost effective anti-piracy system. GUARDIAN is both safe and easy for crew to use, meaning no more cuts from razor wire and is environmentally friendly by being recyclable too.”
Welcoming her appointment, David Stevens, Guardian Maritime’s Sales Director, said: “I am delighted that Jean has joined our team and look forward to seeing her continue to drive the business forward. GUARDIAN anti-piracy barriers ensure shipping and more importantly seafarers are protected while operating in high risk areas.
The first real alternative to razor wire, GUARDIAN works by covering a ship’s safety rails with a specially designed barrier. Once installed, GUARDIAN provides a highly visible, robust and simple way of making access to ship or rig virtually impossible.
Manufactured with UV protection, resistant to water and most chemicals (acids, alkalis, oils etc) and remaining robust over the temperature range experienced by vessels, it is ideally suited to a maritime environment. GUARDIAN’s sections are interchangeable between vessels, providing a strong and rigid structure, tailored to fit around fairleads and unique structures. It is also very adaptable – being available in any choice of colour or pattern to suit any type of sea going vessel. Easy to use and far safer to handle than traditional razor wire for crew, GUARDIAN also saves operating costs by lasting three to five years, and is recyclable.The system is currently protecting some of the world’s biggest fleets including CMA-CGM, Maersk, BW Tankers as well as being used to protect offshore rigs and drilling ships.
The system is currently protecting some of the world’s biggest fleets including CMA-CGM, Maersk, BW Tankers as well as being used to protect offshore rigs and drilling ships.
“GUARDIAN remains the original, best quality and only readily available product with a proven track record. It has a 100% success rate in protecting ships and rigs which is crucial for those ships
operating in high risk areas.” says Teresa Stevens, Director of Guardian Maritime Limited. “We are sadly aware that there are companies reportedly offering ship owners and operators an alternative, inferior product. We are currently taking full legal action against such companies for infringement of design rights, patent and licences. There is only one genuine GUARDIAN for ships and only one product in production ready for the market.”
The success since its launch in 2012 is echoed by ship operators “The GUARDIAN system is a perfect and cost effective way of refusing boarding to pirates and stowaways. After numerous and extensive tests we found the GUARDIAN system impregnable and effective. I highly recommend GUARDIAN for any Marine Company whether they be low and slow or high speed with freeboard” says Rob Twell, Quality, Safety & Security Manager CMA CGM Group.
LNG as a bunker fuel: future demand prospects and port design options
UK based Ocean Shipping Consultants has recently published a detailed report, written by David Bull, Senior Consultant, Maritime & Waterways, Ocean Shipping Consultants, on the current hot topic within the marine sector of LNG as a bunker fuel.
There is much debate regarding the pricing of LNG as a fuel and the current pricing structure for the fuel is opaque. Understanding that there is much speculation, Ocean Shipping Consultants’ new Report — LNG as a Bunker Fuel: Future Demand Prospects and Port Design Options — examines the economics of LNG as a fuel for several vessel types. These include containerships, bulkers, Ro-Pax and platform supply vessels. As well as investigating the economics of LNG as a fuel, there is also discussion in to the costings and options that are currently available to ports that wish to install LNG bunkering infrastructure.
The reason for the investigation is that new environmental regulations coming into force during the near future will have significant impact on those vessels that pass through the UK’s waters, especially the 500 vessels that pass through the English Channel per day. These new regulations are focused on emissions of sulphur oxides (SOx).The UK has an emissions control area (ECA), covering the English Channel and the North Sea, meaning that within that area sulphur content of fuel must not exceed 1.00% and by January 2015, will further reduce to 0.10%.
To enable vessel owners to comply with the ECA rules LNG utilized as a bunker fuel will help reduce ship-borne emissions within UK waters. By utilizing LNG compared to HFO, SOx emissions are reduced by virtually 100%. There are other benefits such as NOx emissions which are reduced by 80%, CO2 emissions are cut by 30% and particulate matter is reduced by 90%. However, major developments of the LNG bunkering infrastructure need to take place before it can be viewed as a viable alternative to conventional fuels. Currently there is limited bunker development within the UK.
There are currently around 50 vessels that now utilize LNG as a fuel with a similar number of vessels on order. Owner/operators from the Baltic and the Scandinavian countries have been the prime movers in this sector, but now more owners, operators and ports are investigating the benefits of LNG as a bunker fuel. Vessels such as the Viking Grace have shown the potential of LNG as a bunker fuel.
The European Commission (EC) have launched through the European Sea Ports Organisation (ESPO) its ‘Clean Fuel for Transport Package’.This consists of a directive on the use of alternative fuels and accompanying infrastructure for road and water borne traffic.
The plan is to develop LNG bunkering facilities in all European ports within the Trans European Core Network by 2020.A similar obligation outlines that all core inland ports will also have LNG refueling stations by 2025. In total LNG refuelling stations are to be installed in 139 maritime and inland ports. The ports will not all be major gas terminals but will be facilitated through either fixed or mobile refueling stations. Through this project the true potential and scale of LNG as a bunker fuel can be seen.
Within the report there are various vessel types that are examined with regards to the economic benefits of utilizing LNG as a bunker fuel. An example of the bulk sector is provided here. For a Panamax bulker utilizing LNG compared to HFO identifies an overall reduction of approximately $2,750/day at sea (for Price Scenario 1 - where LNG is priced at 80% of HFO). For Capesize vessels the overall reduction is $4,500/day at sea for Price Scenario 1, compared to conventional HFO.
A further example of a reduction in costs by utilizing LNG compared to MGO as a bunker fuel is highlighted by an example of a PSV operating in the North Sea. Under LNG Price Scenario 1, the overall reduction in costs approximates $5,500/day ($6,400/day for Price Scenario 2 – where LNG is priced at 60% of HFO). These are a few examples of the cost comparisons that are outlined in the new Report.
In addition, the Report includes forecasts of the future volume of LNG as a bunker fuel as well as a forecast for the number of LNG-fuelled vessels, and highlights that this is an important and growing area of the shipping business for the UK ports to be involved in.
New 2013 edition of the International Maritime Solid Bulk Cargoes (IMSBC) Code
IMO recently published the 2013 edition of the International Maritime Solid Bulk Cargoes (IMSBC) Code and supplement, incorporating amendment 02–13, which may be applied from 1 January 2014 on voluntary basis, anticipating its envisaged official entry into force on 1 January 2015.
To keep pace with the expansion and progress of industry in recent years, the Code has undergone many changes, including:
- Fully updated individual schedules for solid bulk cargoes
- New individual schedules for such cargoes as nickel ore, alumina hydrate, aluminium smelting and remelting by- products, clinker ash, coal tar pitch, coarse iron and steel slag, crushed carbon anodes, grain screening pellets, granulated nickel matte, granulated gypsum, ilmenite, sand, silicon slag, torrefied wood and solidified fuels recycled from paper and plastics
- References to the most recent SOLAS amendments
- Updated information from the 2012 edition of the IMDG Code
The publication also presents additional information that supplements the IMSBC Code, such as the Code of Practice for the Safe Loading and Unloading of Bulk Carriers (BLU Code, including BLU Manual) and Recommendations on the safe use of pesticides in ships applicable to the fumigation of cargo holds. The International Maritime Solid Bulk Cargoes Code and supplement is commended to Administrations, shipowners, shippers and masters and all others concerned with the standards to be applied in the safe stowage and shipment of solid bulk cargoes, excluding grain.
ABOUT IMO
As a specialized agency of the United Nations, IMO is the global standard-setting authority for the safety, security and environmental performance of international shipping. Its main role is to create a regulatory framework for the shipping industry that is fair and effective, universally adopted and universally implemented.
In other words, its role is to create a level playing-field so that ship operators cannot address their financial issues by simply cutting corners and compromising on safety, security and environmental performance.
Poseidon Marine Security launches ProtectaDeck — a new anti-piracy product
NEW ANTI-PIRACY PRODUCT
Poseidon Marine Security has launched a global marketing campaign for its new product ProtectaDeck, an anti-piracy barrier for the shipping industry to protect vessels and oil rig platforms from the increased number of piracy attacks throughout the world. ProtectaDeck prevents intruders from boarding, is inexpensive, as well as being easy to install and maintenance free.
Whilst attacks in the traditional piracy areas such as Somalia have reduced, there have been increases in other piracy hotspots in particular the Gulf Of Guinea. Pirates are extremely ready to resort to violence, loot cargoes and other valuables or abduct crew members and hold them for ransom. Other hotspots include Indonesia, Malaysia and the Malacca Strait South China Sea and even nearer to home, cargo barges on the River Danube where there have been attacks by Eastern bloc mafia groups.
Managing Director Luis Labaton says “We offer a bespoke service. ProtectaDeck works by covering the ships safety rails with a specially designed barrier preventing access to pirates whose main method for gaining access is by use of roofing ladders and grappling hooks.
The risk of attacks is high, with over 15,000 ships a year passing through pirate infested waters a year. If ships have anti-piracy devices on board it not only provides protection but gives financial benefits such as reduced insurance premiums. Luis adds,“we are proud that all our products are made in the UK”
Poseidon Marine Security is backed by serial entrepreneur and inventor David Salon of Gravitas International who says,“ we have worked hard developing several anti-piracy products and believe ProtectaDeck will be the latest must have for the shipping industry “
BOILER PLATE
Poseidon Marine Security has developed ProtectaDeck to complement its range anti-piracy products.Although many ships have anti-piracy product devices on board such as barbed wire and water hoses ProtectaDeck is cheaper, safer to use by crew and eliminates the no risk of unwanted deck boarding.
With piracy attacks increasing in new hotspots we expect a high demand for our product not only from the shipping industry but also from oil rig operators.A similar product is due to be launched in the summer aimed at protecting government building and military bases.
Poseidon Marine Security is backed by David Salon, an inventor and the founder of the Daley’s group who recently sold his business to 3M before forming Gravitas International which specializes in anti-flood barriers.