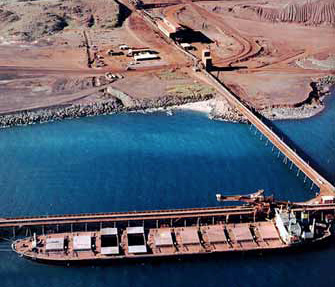
DemcoTECH showcases materials handling expertise in port handling facilities
Lack of sufficient overland and port materials handling facilities can often be the bottleneck in the economic growth of developing nations, which are generally plagued by minimal established infrastructure, says DemcoTECH Engineering general manager, Paul van de Vyver.
Headquartered in Johannesburg, South Africa, but with an international client base, DemcoTECH has first hand knowledge of the logistical and infrastructural challenges facing companies operating from developing nations.
“We have been responsible for a number of bulk materials handling facilities for terminals such as Grindrod’s Richards Bay and Maydon Wharf in South Africa, as well as having been responsible for the overall design for a multi-billion dollar iron ore import/export facility in Malaysia,” says van de Vyver.
As an engineering contractor on one of the world’s largest iron ore distribution centre projects to date,Vale’s project in Lumut, Perak, Malaysia, DemcoTECH provided materials handling
engineering and support services for the establishment of the iron ore import/export blending centre. Due to be operational in 2014, the regional distribution centre comprises a deep water jetty and an onshore stockyard to receive iron ore from Vale’s mines in Brazil and distribute it to customers across the Asia Pacific region.
In addition, DemcoTECH separately provided operational readiness services, including the preparation of operational and maintenance manuals and training modules.
In South Africa, DemcoTECH supplied a mobile ship offloading and warehouse distribution system for Grindrod Terminal’s fertilizer storage facility at Maydon Wharf in Durban.
“The system replaced a trucking system with a major impact on productivity of the operation,” notes van de Vyver.
The system, designed and supplied by DemcoTECH through an engineering, procurement and construction management contract (EPCM), comprised four mobile (grasshopper) tyremounted conveyors stationed on the jetty at locations to suit the ship docking arrangements. Once the ships have been offloaded, the fertilizer is conveyed to a central pivoting and retractable boom conveyor.
The existing warehouses were modified to incorporate five reversible, multi-point discharge shuttle conveyors. These conveyors feed individual bays in the warehouse.
“A very important feature to ensure optimum efficiency was the fully sequenced automatic starting and stopping of the systems, which ensures a seamless operation, with no blockages or hang-ups, and the ability to handle different types and grades of fertilizer,” says van de Vyver.
Also for Grindrod Terminals, DemcoTECH was responsible, through an EPCM contract, for the materials handling portion of the expansion to its multi product terminal at the deep-water port of Richards Bay, on the east coast of South Africa. The scope of the contract covered providing the materials handling to convey various materials, but mainly rock phosphate and coal, from the three Richards Bay terminal sites: Navitrade, Kusasa and Valley.
At Navitrade, a tippler discharges material onto three belt conveyors. The second conveyor discharges either onto the third conveyor, which feeds an open stockpile at Navitrade or to a pipe conveyor. The pipe conveyor feeds the Kusasa transfer house, which distributes the material either to the existing export line or to Kusasa conveyors that feed the Kusasa warehouse. The Navitrade stockpile is equipped with front end loaders, which reclaim material via a Buffalo feeder discharging the material into a pipe conveyor.
The Kusasa materials handling system consists of two belt conveyors, which feed the existing warehouse via a travelling tripper. The material is reclaimed from the warehouse via steel hoppers to four belt feeders. These feed a belt conveyor which in turn feeds back to the Navitrade pipe conveyor for export purposes.
The materials handling system at the Valley terminal site was an extension to plant supplied previously by DemcoTECH, which conveyed material from terminal conveyors to feed a single warehouse. The expansion extended the lead conveyor to feed a choice of two other warehouses. This involved modifications to the existing belt conveyor to accommodate a moving head to discharge the material either onto an existing stream or onto either of two belt conveyors. These discharge onto two dedicated warehouse feed belt conveyors, which in turn feed the dedicated warehouse via a travelling tripper.
“As this was a brownfield site at a very large terminal, the interfacing of new equipment into the existing equipment had to be carried out around planned shutdowns in order to minimize disruptions to operations,” noted van de Vyver.
“These projects showcased our comprehensive range of systems and technologies that we are able to design and supply for the port handling industry. This ranges from conveyors through to moving head systems, tripper systems, stackers and reclaimers, sampling plants, storage facilities and bulk material silos.
“Our experience and expertise in conveyor systems cover the full spectrum of overland and in-plant conveyors and we specialize in pipe conveyors, having supplied these systems using a triangular tubular gantry fitted with a mobile maintenance trolley.”
“With regard to sampling plants, we established an iron ore sampling plant at the Saldanha iron ore terminal in South Africa
for Kumba Resources, later completing an upgrade to the facility, which allows the sampling of a wide range of iron ore products, from fine material to lump ore for export purposes.”
The upgrade converted the sampling plant from a mass to a time based system, which reduces bias in the selection of material sizes for sampling purposes. The upgrade was carried out on a shutdown basis to minimize any demurrage fees.
The turnkey upgrade project covered installation of new conveyors to feed the sampling plant, addition of load cells into the weigh hopper for more accurate readings and introduction of a two-way splitter.
This automated iron ore sampling plant enables Kumba to assure quality that complies with the world’s highest International Standards Organization (ISO) benchmark. During the process, samples are taken from the supply line, en route to the ships, and are introduced into a fully automated robotic laboratory where they are prepared simultaneously for physical and chemical analysis. The sampling facility has two conveyor streams, with single product loading possible using either conveyor.
The sampling facility enables exporters to have the physical and chemical qualities of iron ore products certified independently before they are loaded for export. The facility was designed to comply with ISO 3082 and facilitates a quick turn- around time.
DemcoTECH services are offered though contracting mechanisms from EPCM to Lumpsum Turnkey including studies and from concept design through to detailed feasibility studies. After-sales services include spares, maintenance, refurbishments and operational readiness packages covering procedures, systems and workplace tools required to successfully operate and maintain a new or upgraded plant.
Tenova TAKRAF wins further order from leading Italian steel producer
Tenova TAKRAF Italy has been awarded a contract by ILVA S.p.A., a leading Italian steel producer, for the design and supply of a bucket chain continuous ship-unloader for handling iron ore and coal at the ILVA steel plant in Taranto, Italy. This plant is the largest of its kind in Europe. The 18-month turnkey contract builds on a longstanding business association between Tenova TAKRAF and ILVA of 40+ years.
The new continuous ship-unloader (CSU) will have an operating capacity of 4,000tph (tonnes per hour) for iron ore or 2,240tph for coal and will be able to download vessels up to 150,000dwt. The CSU will be erected on the existing runways of the ILVA plant’s Pier II to feed the entire steel plant with coal and iron ore and pellets, together with the other machines at the plant. The CSU will be almost entirely manufactured by Italian companies and is expected to be operational in late March 2015.
In addition to the long-standing and much-valued relationship with the client and competitive pricing, availability of this technology was a major factor in the award. Only a few companies in the world are able to supply this type of technology and Tenova TAKRAF offers many successful references. To date, 15 CSUs have been supplied worldwide, with relevant references to the lLVA award being excellent performances achieved by four CSUs recently supplied to Enel for Brindisi South and Torrevaldaliga North, in Italy.
Tenova TAKRAF developed its bucket chain continuous ship-unloader technology in the 1980s. Subsequent years have seen ongoing enhancement to the technology, with the most sophisticated part being the digging foot, for which Tenova TAKRAF holds the patent.
Following the devastating tornado of November 2012, ILVA initiated a plan for environmental rehabilitation of the steel industry in Taranto. The new CSU was ordered as a consequence of this. The plan involves replacement of the
old grab ship-unloaders (supplied in the 1970s under the Italimpianti trademark) with modern bucket chain CSUs, which significantly reduce dust emission during the discharge cycle. The CSU’s low environmental impact is a major feature, noting that the steel plant is close to the city area.
In this brownfields project, the CSU is replacing the existing old grab unloaders at Pier II. Tenova TAKRAF also supplied a CSU for Pier IV in 1999, and an additional large grab unloader for the same Pier in 2009.
“Tenova TAKRAF’s involvement with this important client dates back to the 1970s, at which time Tenova TAKRAF was known as Italimpianti,” says Alberto Dardano, managing director of Tenova TAKRAF Italy. “This valued relationship has been sustained not only through many repeat contracts, but also, through the quality of after sales services we have provided to ILVA on an ongoing basis.”
Tenova TAKRAF is a key supplier of equipment and systems for open pit mining and underground solutions and bulk handling, having provided hundreds of complete systems, as well as individual machines to clients all over the world in all climatic conditions. Leading-edge comminution systems for milling and crushing requirements in mining and mineral processing are based on a track record in mill supply dating back to the 1920s. Globally sourced air pollution control, specialized handling equipment, and technology for the cement and fly ash industries ensure selection of optimal processing options.
Tenova Mining & Minerals is a total integrated solutions provider to the global mining, bulk materials handling and minerals beneficiation and processing sectors, offering innovative technological solutions and full process and commodity knowledge across the mining industry value chain.
Tenova is a worldwide supplier of advanced technologies, products, and engineering services for the metals and mining & minerals industries.
Ausenco demonstrates significant expertise in delivery of turnkey contracts
Ausenco has significant experience with bulk-related turnkey projects carried out over the last 25 years, as well as projects in the minerals and metals mining and processing field. The company has completed EPC (engineering, procurement and construction) projects as a prime contractor providing detailed design, procurement and full construction services; as JV (Joint Venture) partner with shared EPC project responsibilities; and as subcontractor to the prime contractor who retains overall project responsibility. In addition, the company has provided design engineering services only (the ‘E’ component of the EPC contract) directly for the prime contractor.
On another very successful EPC project,Ausenco participated as a full JV partner in the EPC team that worked in a strategic alliance with the owner.
Ausenco demonstrates significant expertise in delivery of turnkey contracts Ausenco believes that it is always important to complete thorough front end engineering on a project before entering into an EPC arrangement. This will lead to the project being successful and a win-win situation for both the owner and the EPC contractor.
The company considers that the most significant project improvements occur in the early planning, engineering, and construction methodology development.
Because of this,Ausenco believes that engineer-led EPC projects offer significant benefits to the owner due to the fact that it has performed all of the preliminary design and has worked extensively with the owner to develop excellent working relationships and a mutual high level of trust.
A few selected examples of Ausenco’s key bulk-related turnkey projects include:
ANTAMINA CONCENTRATE EXPORT TERMINAL IN HUARMEY, PERU
Client: Bechtel International as agent for Compañia Minera Antamina
Timeframe: 1999–2002 Scope: EPC of concentrate export terminal Services:Planning, design, procurement, and construction
Project value: $230 million (export terminal only) Ausenco executed the EPC development of the Antamina Concentrate Export Terminal at Huarmey, Peru.
The terminal is capable of annual export of 1.8mt (million tonnes) of copper and zinc concentrates annually. Facilities include receiving tanks for the overland slurry pipeline, slurry dewatering facilities, storage shed for 150,000 tonnes of concentrate, conveyors from the filter plant to the storage building and from the storage building to the shiploader, berth for ships up to 50,000dwt and associated infrastructure.
Ausenco provided project engineering, procurement and construction management services as partner in a joint venture with SSK Montajes e Instalaciones S.A.C., a Peruvian–Chilean contractor to carry out the construction.
The project was executed under a PI (Performance Incentive) Contract where the owner and contractor share underruns and overruns. The contract was completed three months ahead of schedule with an associated budget underrun.
As well, the JV with SSK achieved the best safety record of the 40 contractors on the $2.3 billion Antamina mine/port project, having exceeded 3.5 million hours of work with only one lost time injury.
The project was successfully constructed to World Bank environmental management standards. Ausenco received the Consulting Engineers of British
Columbia Award of Merit for this project in 2002.
COLLAHUASI COPPER EXPORT TERMINAL IN IQUIQUE, CHILE.
Client: Compañia Minera Doña Ines de Collahuasi S.A. Timeframe: 1996–2000 Scope: Site selection, port feasibility study, EPC development of the terminal Services: Planning, engineering, procurement, construction Project value: $38 million Ausenco’s earlier work on port site selection and feasibility studies led to an EPC contract for ‘fast track’ design challenged by difficult site conditions and limitations of locally available equipment.
The Collahuasi Copper Mine was developed in northern Chile and at the time was anticipated to be the third largest in the world. The initial production was planned to be 1mt (million tonnes) a year of copper concentrate, which is transported by slurry pipelines to the port. The facility can accommodate vessels up to 60,000dwt.
The irregular underwater bedrock profile and the presence of large boulders made pile installation very challenging. Overcoming the lack of any substantial overburden, the required pile design capacities were innovatively achieved by anchoring pile tips into bedrock.
The seismic design of the shiploader illustrates state-of-the- art design approach permitting the shiploader to withstand a seismic event well in excess of the code requirements without significant damage.
This project features the first fully enclosed boom of a quadrant shiploader to contain dust, setting new standards for environmental design.
HAMERSLEY IRON DAMPIER PORT EXPANSION
Client: Hamersley Iron Pty. Limited
Timeframe: 1999-200
Scope: Iron ore export terminal expansion and upgrades
Services: Feasibility study, master plan, cost estimates, simulation modelling, definitive engineering and EPC services.
Project value: $200 million.
Hamersley Iron Pty. Limited is Australia’s leading iron ore exporting company with an annual throughput approaching 60mt/year. Its company-owned railroad delivers ore from five mines in the Pilbara region, some 370km, to two terminals in Port Dampier. Trains consist of 220 ore cars, each of 105 tonnes nominal capacity. The trains are rotary dumped at either East Intercourse Island or Parker Point, where the ore is conveyed to either lump or fines stockpiles for blending prior to shiploading in vessels up to 350,000dwt size.
Following a worldwide search, Hamersley selected Ausenco and Clough Engineering Group, a Perth-based contractor, to form a strategic alliance to provide engineering and construction services for future expansions.
The first task of the alliance was to develop a long-term master plan to define the future expansion possibilities in several stages to an ultimate capacity of 90mt/year (from 55mt/year). The master plan team examined many scenarios for expansion of one or both existing terminals while maintaining the growing throughput.
A key part of the master planning studies involved the analysis and simulation of operations. Extensive simulation modelling was done to test the existing and future operations. The model included the railcar loadouts at six mines, the railroads, railcar dumping, blending, stockpiling, reclaiming, screening and shiploading operations at the two terminals.
The master plan proposed expansion of the existing terminals in several incremental steps to suit the timing of new mine developments and market growth.
Next, the definitive engineering studies were completed, followed immediately by provision of EPC services for the Dampier Port Upgrade Project which also included upgrades and new facilities for both the Parker Point and East Intercourse Island iron ore export terminals.
TRF’s turnkey projects in ports and stockyards
INTRODUCTION TO TRF
TRF Limited has been a major provider of material handling solutions for five decades. Set up in 1962, it is part of the Tata Group that operates in seven sectors and has a combined turnover of about $100,00 billion. The company designs, supplies, erects and commissions bulk material handling equipment and systems in infrastructure industries like steel, power, mining, ports and cement. It provides total engineering solutions, from the concept to commissioning, to fulfill the requirements of its customers in the core sectors. TRF has the expertise in executing turnkey projects for handling dry bulk cargo within the country and also overseas.
TRF’S PORT & YARD EQUIPMENT DIVISION: CAPABILITY AND PRODUCTS TRF’s Port and Yard Equipment Division is a renowned supplier of port equipment and specializes in the engineering and manufacturing of bulk material handling equipment for ports, shipyards, power plants and metallurgical units. An in-house manufacturing unit located at Jamshedpur, India, supported by a highly skilled engineering team using advanced computer-aided designing tools and a strong quality assurance and inspection system are some of the key strengths of the division. An extremely efficient and dedicated team of erection and commissioning engineers ensure high level of supervision of the project equipment at site. The division also offers consultancy and maintenance services to these sectors. To enhance the performance of its state-of-the-art equipment and the benefits that accrue to its customers, they are customized to fit the requirements and unique characteristics of every location. This translates into uninterrupted higher output and a competitive advantage for its customers.
TRF’s Port and Yard Equipment Division is capable of undertaking turnkey projects for delivering material at high capacity and on continuous basis for different types of industries handling bulk cargo like coal, iron ore, limestone, dolomite, coke, lignite, fertilizers, food grains and similar types of raw materials. The projects start from unloading of bulk material, conveying, processing/sizing through a series of crushers and screens, storing and reclaiming through mechanized equipment and again feeding the discharge point by a series of conveyors and appropriate unloading machinery. To ensure that the entire operation is completed efficiently TRF supplies most of associated equipment, such travelling trippers, slewing stackers, bucket wheel reclaimers, stacker cum reclaimers, barrel reclaimers, stacker/reclaimers, wagon loaders, wagon tipplers along with side-arm-chargers which are manufactured in-house at its plant in Jamshedpur. Similarly, various types of ELL (electric level luffing) cranes such as goose neck, single boom grab and hook duty etc. and shiploaders, ship/barge unloaders have been supplied to various ports and shipyards for handling dry bulk material and construction of ships respectively. The capacity of the TRF stacking and reclaiming equipment ranges from 3,600tph (tonnes per hour) in stacking mode to 3,000tph in reclaiming mode. TRF’s wagon loaders are of 3,000tph with a boom length of 7.5 metres, ship unloaders are of 2,000tph with an outreach of 38 metres and ELL cranes are of 60tph capacity with outreach of 50 metres.
SOME TURNKEY PROJECTS IN INDIA AND THE INTERNATIONAL MARKET
The company’s major customers include Tata Steel Ltd, National Thermal Power Corporation, Steel Authority of India Ltd, Rashtriya Ispat Ngam Ltd, various state electricity boards , Bharat Heavy Engineering Ltd, Damodar Valley Corporation, Jindal Steel & Power Ltd, Essar Steel Ltd, Mideast Integrated Steels Ltd, Durgapur Projects Ltd, Bhusan Power and Steel Co Ltd, LANCO, Jindal Power Ltd, BMM Ispat Ltd, Heavy Engineering Corporation Ltd, Energo, National Aluminium Co Ltd, Calcutta Port Trust, Krishnapatnam Port Co. Ltd, NTPC Tamil Nadu Energy Co Ltd, NLC Tamil Nadu Power Ltd, Paradip Port Trust, Kandla Port Trust, Mumbai Port Trust, Visakhapatnam Port Trust,Tuticorin Port Trust, Nippon Denro Ispat Limited, Oswal Chemicals & Fertilizers Ltd, Mazagon Dock Ltd, Cochin Shipyard Ltd, Birla Copper Ltd and many more in government and private sectors.
TRF has also established a presence in the international market by supplying bulk material handling equipment to various projects and customers such as Tata Steel KZN, South Africa, Doosan Heavy Industries, Korea for their Cirebon, Indonesia project and Shadeed Iron & Steel Company, Oman (now Jindal).
The company has supplied a slewing stacker to Tata Steel KZN for its ferrochrome plant in Richard’s Bay, a reversible stacker reclaimer to Doosan Heavy Industries and various equipment and complete electrical and automation systems to Shadeed Iron and Steel Company.
MARKET OPPORTUNITIES IN INDIA
India has a coastline of approximately 7,517km and is serviced by various major ports and other minor and intermediate ports — both in public and private sectors. These ports handle various types of cargo, out of which dry bulk cargo — mainly food grains, iron ore, coal, chemicals and fertilizers constitute about 45% of the total volume of cargo handled. Although the volume of cargo has grown considerably in the recent past, most of the ports even today still carry out their operations with primitive methods of unloading by using obsolete geared vessels and mobile harbour cranes. These operations consume valuable time and lead to huge amount of wastage during loading and unloading. Immediate augmentation of the port facilities in terms of investment in high-capacity mechanized handling facility is required.
Some ports have already taken appropriate action to augment their cargo handling capabilities. Hence TRF sees this as a huge potential market as it has the ability to excel its market peers, in the country, by providing reliable and durable turnkey solutions that are developed in-house at highly competitive prices. This is possible because TRF has the complete range of products required for the purpose of putting up a mechanized berth, from start to finish, to handle dry bulk cargo at ports.
TRF is geared to provide the following products for:
A. Incoming cargo:
- ship/barge unloaders or ELL cranes (depending on the type of dry bulk cargo) or wagon tipplers as the case may be for unloading cargo;
- transportation of the cargo after discharging from the above equipment to the stockyard through a chain of conveyors; and
- stacking of cargo at the stockyard using stacker/reclaimers or slewing stackers.
B. Outgoing cargo:
- reclaiming of cargo from stockyard using stacker/reclaimers or bucket wheel reclaimers;
- transportation of cargo to the loading point by a chain of conveyors;
- loading of cargo by wagon loaders or shiploaders as the case may be for onward dispatch.
All the above products of TRF are well established in the market with a proven track record and customers have reported a high level of satisfaction with product performance. TRF is one of the engineering companies in India which has the expertise and ability to carry out such turnkey project in-house by designing and supplying equipment manufactured by it.