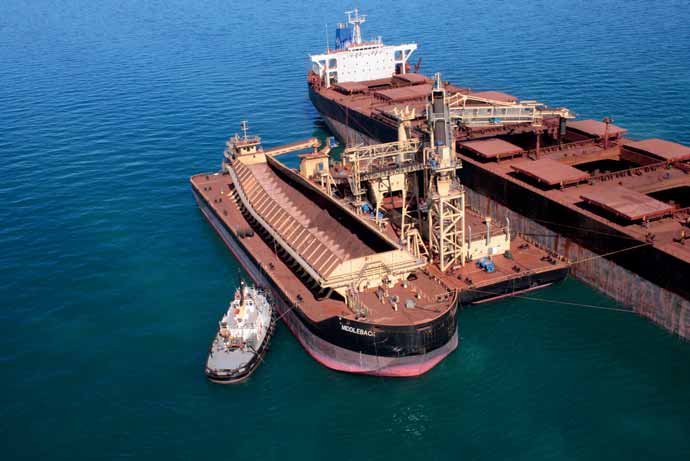
An innovative and affordable solution for bulk logistics in developing countries
It is arguable that economic growth of a particular country depends on its ability to provide adequate infrastructure to facilitate growth. This statement is especially true for countries that depend heavily on exports of natural resources to boost economic growth. However, supporting infrastructures such as ports, rails or roads does not come cheap and requires great deliberation before commencement of development: think of feasibility studies, environmental impact assessments, delays in political approvals etc. — the main constraint on development is the funding issue. Unfortunately, many countries which depend heavily on such exports are developing countries and, therefore, lack the funds required to build costly infrastructure. Private investors or companies are thus expected to invest themselves in the infrastructures required to exploit the resources. Apart from some of the larger mining companies, few small-to-midsize players have the firepower and risk-appetite to invest in fixed infrastructure in developing countries. Unknown political risks, difficulty of funding in countries with below investment grade credit ratings are some of the main constraints cited by potential investors. Such situations indicate a need for an infrastructure that is not fixed, so that it can be moved and used somewhere else in a worst-case scenario.
Indonesia for example, before becoming one of the fastest growing emerging nations and one of the world’s major coal exporters, started its journey in coal exports 20 years ago without a proper coal terminal. Because of this constraint, Louis Dreyfus Armateurs (LDA) started developing innovative solutions to allow large exports of dry bulk commodities (mostly coal and ores) from such areas, without the need to invest the large capex usually required by fixed port infrastructures. In 1991, LDA provided PT Adaro with the first floating crane transshipper unit to reach Indonesia. The transshipper enabled PT Adaro to become one of the key players in Indonesia for innovative transshipment solutions. The country has been a special case for maritime logistics, due to its vast network of rivers accessible for coal miners which made river barging and transshipment a very viable logistical solution compared to trucking and railing, where costly investment in dedicated roads or rails are required. Today, there have been notable improvements in the availability of deep-sea terminals; however, these are mostly built by private developers — with only two common-user coal terminals available in Kalimantan as of now — the problem of high initial capital investment still remains.
Ever since then — through its dedicated subsidiary LD Ports & Logistics and Orchard Maritime Services Pte Ltd (OMS), which handles the Southeast Asia activities of LDPL — LDA has been active in the maritime logistics industry worldwide, acquiring an essential know-how in offshore transshipment, and associated barging and port management services. Below is an example of LDPL’s approach to provide maritime logistics solutions to a client in India.
CASE STUDY: IRON ORE TRANSSHIPMENT IN INDIA
The background
A major Indian iron ore producer approached LD Ports & Logistics (LDPL) in 2006 with a need for a suitable logistics solution. The company owns iron ore mine concessions in Goa, India and was looking to export its coal effectively without the need for costly infrastructure upgrades. The bulk of the company’s production is exported to countries with smelters capable of handling low-grade iron ore, as low-grade iron ore is not suitable for many iron ore smelters in India.
In addition, the company was looking for a long-term partner with transshipment expertise and — most important of all — a commitment to long-term reliability. LDPL — which shares the company’s view on long-term partnership — was therefore ideally positioned to work closely together with the company. Moreover, the enduring history of LDA confirmed the company’s need for a reliable partner through thick and thin.
The Problem
When LDPL was approached, there was already an existing port (Mormugao) and a few transshippers were already operating at nearby anchorages. However, Mormugao port was already congested and there was not enough capacity to handle the company’s growing exports of cargo. The transshipper units available in the area were floating transfer stations with conveyors and therefore were not suited for the type of low- grade iron ore that the company exports, due to the its inherently high moisture content. Loading interruptions to clean
up the conveyor belts and moving parts were frequent, and maintenance costs were high.
Moreover, LDPL identified that the transshippers available at that time had to be partly manned by foreign crews due to the inability to find local crews skilled enough to operate the comparatively more complex systems of a floating transfer station. This contributed to higher running cost when compared to employing local crews.
The solution
Given the characteristics of the iron ore that was exported in the area, LDPL concluded that the most ideal tool to load such material would be a floating crane which utilizes grabs as the main transshipment tool. LDPL specifically designed a floating crane transshipper unit using simple, efficient and robust features to enable handling of sticky cargo. The design is based on a pure electrical power supply distribution with no hydraulics, thus reducing the need for costly maintenance and improving reliability and durability. The floating crane also has its own propulsion, allowing operational flexibility.
With its floating crane transshipper, LDPL also eliminated the difficulty and costs of expat crewing because of the easy-to- operate nature of the floating crane system. With minimal training, local crews can already operate the floating crane effectively and efficiently.
Moreover, floating crane transshipper(s) can cater better to new producers due to their scalability; with the client having uncertain ramp-up volume at the time of deliberation, LDPL confirmed the suitability of floating crane transshippers. Floating transfer stations, with their high transshipment capability and higher capital expenditures, can be uneconomical to operate at first for this specific case as they will be under-utilized during early years of ramp-up.
The technology
Floating crane transshipper units used for this particular project have the following advantages and specifications:
LDPL 32T floating crane transshipper unit
- based on a reliable and proven design with a life expectancy of over 20 years: no hydraulics, 100% DC current PLC controlled;
- low fuel consumption (±3.5 MT/day MGO); v classed BV/ALM (Appliance for Lifting in Marine environment);
- environmentally friendly: no hydraulics on board and are equipped with grabs specially designed for handling dusty materials (enclosed scales, knife sealing systems for handling fines and free flowing materials);
- Designed to operate with winds up to Beaufort 4 (maximum 16 knots) and sea state up to Douglas 3 (maximum 1.25m waves height); and
- able to handle high-moisture content cargo.
The application
At first, LDPL provided one floating crane to match the client’s required volume output at that time and therefore the first floating crane transshipper was delivered in 2007 to a newly- formed joint-venture between the miner and LDPL.
Small barges (<3,000dwt) were loaded with iron ore at the barge-loading facility and then transported the cargo offshore to ocean-going vessels via LDPL’s floating crane transshipper. The vessels are mostly sailing to China, as India has a freight advantage over other iron ore-exporting regions such as West Africa and South America.
After a few successful years, the client was pleased with the transshipper’s performance and with the partnership formed with LDPL. Therefore in 2010 LDPL ordered two more floating crane transshippers to satisfy the client’s demand. With multiple units at its disposal, LDPL helped achieve complete operational redundancy of transshipping for the company: internal redundancy for each unit due to the design of its power generation and also redundancy through the presence of multiple self-propelled units. This is also one of the main advantages of multiple floating crane transshipper units compared to conveyor-based transshippers, as conveyor-based transshippers will need to stop the entire transshipment operations in the event of a breakdown of just one of the conveyor systems.
This problem-solving approach and customized solution for its client is what made LDPL an ideal partner for maritime logistics; to date, LDPL’s solution in India has transshipped over 11mt (million tonnes) of iron ore before the Goan Mining Ban took place, and the three floating crane transshipper units have proven to be able to load up to 840,000 tonnes per month, which is equivalent to fully loading five 170,000dwt Capesizes per month, or more than 10mt per annum of export capacity. This has been achieved even though there is a notable increase in handling time: more wheel-loader activity (due to the size of barges), more mooring and unmooring manoeuvres (due to the larger number of barges required), and also more shifting manoeuvres (due to the fact that many vessels have been partially loaded before offshore loading operations took place).
LDA always strives to provide clients an integrated maritime transportation solution with a wide range of logistics services matching the specific needs of each client, whether to a mining company, trader or end-user (industrial users/power plants).
ABOUT LD PORTS AND LOGISTICS
Headquartered in Singapore and France, LD Ports & Logistics (LDPL) is a subsidiary of Louis Dreyfus Armateurs (LDA), an acclaimed leader with more than a century of experience in the shipping industry. It is the only maritime logistics company which is owned by a shipowner.
Known for its consistency, reliability and innovation in the delivery of logistics and port operation services around the world, LDPL is a one-stop solution — design and operate — for all maritime logistics projects.
Self-propelled barges
LDPL has designed its fleet of self-propelled barges in response to the demand for a more flexible, reliable and cost-effective barging solution. Depending on customers’ operations, self- propelled barges can be fully customized to clients’ needs and entirely operated by LDPL.
The fuel-saving self-propelled barges can sail in both river and sea, with up to 13,000dwt tonnages at 5.5m draught and can sail at a speed of 10 knots — twice as fast as that of towed barges of similar size, more manoeuvrable and 40% more fuel efficient.
LDPL’s self-propelled barges are IACS-class sea-going vessels with significant seaworthiness in bad weather that can sail distances of up to 1,000 nautical miles.
Floating crane transshipper units
LDPL floating crane transshipper units are designed to be simple, efficient and robust which are essential features for any logistics operations to be performed at sea.
The floating crane transshipper unit design has been optimized to perform high transshipment rates in loading and unloading all types of vessels, from Panamax to Super Capesize.
Transshippers
A new generation transshipper (floating transshipment unit) has been designed to cater to the needs of exporters with large volumes of dry bulk cargo. LDPL provides two main types of Floating Transfer Station (FTS) – Environmentally Friendly Transshipper, for high-speed loading at areas where environmental concerns are existing, and Separated Hulls with Significant Buffer Capacity for specific operations where cargo blending/storage is required.
Port management
LDPL teams have extensive experience in port management from vessel berthing (using harbour tugs), mooring and stevedoring, maintenance of equipment to the loading and unloading of cargo (using shore cranes). With the objectives to keep efficiency and safety as the main priorities when managing ports, LDPL has proven to be a reliable and trusted partner to its clients.
Self-unloading barges
LDPL has developed a new self-unloading barge design to answer the specific needs of exporters with high volumes of dry bulk cargo requiring a fast and reliable self-unloading vessel system.
The solution involves a 15,000dwt self-unloading barge, designed to ensure a discharging rate of up to 40,000 tonnes per day through a totally enclosed conveyor system.
CSL International: transshipment activities on the North American coast
The CSL International Pool offers a transshipment service on the North American East Coast. Using geared Handymax and Panamax vessels specially fitted with side-mounted grabs, hoppers and a boom for single-point discharge, the service allows a gearless Panamax vessel to have its cargo of coal from the Far East transhipped at rates up to 35,000 metric tonnes either into barges for direct delivery to shore based facilities, or by direct delivery from the transshipment vessel itself.
With strict environment regulations continually being implemented, the requirement for ‘environmentally friendly’ coal from various parts of the world is becoming more and more a necessity. The use of transshipment vessels has now opened the door for this coal to be burned on the North American East Coast. The service allows charterers to by-pass draught limitations and ports that lack discharging installations, both of which have hampered the use of gearless Panamax vessels in the past.
THE TRANSSHIPMENT VESSEL WORKS IN A VARIETY OF WAYS
Discharging into barges
The transshipment vessel remains stationary and discharges the gearless Panamax directly into barges using its side-mounted grabs, via the discharge boom. As the barges move to the shore facility, the transhipment vessel continues to discharge the Panamax into its own holds. When the barges return, the transshipment vessel continues to discharge the Panamax
directly into the barges. Once fully discharged, the Panamax will depart, leaving the transshipment vessel to continue to load the barges from its own holds.
Lightering the Panamax and discharging to shore directly The transshipment vessel discharges the Panamax directly into its own holds and then proceeds to the berth to discharge at the customer’s facility via its discharge boom. When fully discharged, the transshipment vessel returns to the Panamax. When the Panamax’s holds are empty, it will depart, leaving the transhipment vessel to proceed to port to complete the discharge at the facility.
Lightering the Panamax and then discharging the remaining cargo on both vessels in port This situation is similar to No.2 except that once the Panamax vessel is lightered sufficiently to proceed safely to port, it does so and then ‘double banks’ with the transshipment vessel alongside the customer’s facility. The transshipment vessel then fully discharges the Panamax, upon which time the Panamax departs, leaving the transhipment vessel to discharge the cargo remaining in its holds.
Distribution of lightered quantities at more than one discharge port Using a transshipment vessel, a ‘cargo pipeline’ can then feed more than one facility by using any combination of the above.
Bedeschi & BLL in continuous transshipment project
After the successful commissioning of the largest transshipper in the world, Ore Fabrica, which is operating in the Subic Bay, Philippines to discharge iron ore fromValemaxes,Vale has appointed Bedeschi to supply cargo handling equipment for another transshipper, Ore Sossego. This transshipper is also of about 280,000dwt capacity and is presently under implementation. The Ore Sossego will also be fitted with 5 MPG cranes, of Liebherr make, and a cargo handling system comprising of five hoppers, of 50m3 capacity each, equipped with variable belt drives feeders, conveyors and two shiploaders. The major difference between Ore Fabrica and Ore Sossego is that while the shuttle vessel receiving the iron ore on Ore Fabrica remains stationary and the shiploader moves and travels the length of the transshipper, in case of Ore Sossego the shuttle vessel will have to be warped alongside the transshippers and will be fed by two fixed shiploaders.
The basic layout will be such that one section of longitudinal conveyor will be fed by three cranes and the other by two cranes, both moving in opposite direction and transferring the iron ore to a transverse conveyor. The transverse conveyor will have a capacity of 6,000tph (tonnes per hour) and will transport the cargo across the beam of the transshipper leading to a deviator, which will distribute the cargo to either of the shiploaders. These retractable shiploaders of 3,000tph capacity each, will be having an outreach of 44m and will have slewing and luffing capability. Once in operation the transshipper will be able to transfer cargo directly from the Valemaxes into the shuttle vessel in a triple banking operation. In the absence of shuttle vessels the discharging operation of the Valemaxes will still continue and cargo will be stored in the holds of the transshipper, to be reclaimed and transferred to the shuttle vessels later.
Bedeschi has recently completed the commissioning of a Floating Transfer Station — Princess Victoria, a sister unit of Princess Chloe, which has been in successful operation in Kalimantan, Indonesia, since 2011 for PT Mitra. This FTS is equipped with two Liebherr cranes working with a combination of hoppers, feeders, conveyors and a retractable, luffing and slewing shiploader of 2,200tph capacity, supplied by Bedeschi. The FTS is also equipped with automatic sampling device, on line weighing system and metal detection system. The shiploader of the FTS, which has an outreach of about 38m and an airdraught of 19m, is fitted with a curved delivery chute, which can deliver coal into all parts of the holds of a Capesize vessels, evenly without any broken space. Another important feature is that the shiploader has the capability to lift and transfer a bulldozer into the holds of the ocean going vessels for cargo compaction. These unique features stand out and give the FTS an edge over any competition in terms of loading efficiency. The FTS Princess Victoria was constructed in Keppel Shipyard at Subic in Philippines and the equipment installation and commissioning was supervised by Bedeschi technicians. The FTS is now in successful operation in Kalimantan in Indonesia.
Another recent completion of a project by Bedeschi is the engineering, supply and installation of a new shiploader for loading coal for a rechristened FTS Bulk Celebes. The client Coeclerici Logistics had requested Bedeschi to study an existing floating transfer station operating in India and supply a new and efficient shiploader to enable it to load coal at 2,200tph i.e. faster and efficiently. The new retractable shiploader, is similar to the ones already operating in Indonesia, is equipped with the curved delivery chute has been supplied by Bedeschi and the FTS was retrofitted in Singapore for coal loading operations in Indonesia.
The newly completed FTS Royal Sesa has arrived in India but has yet to commence cargo loading operations, because of the iron ore ban put by the local regulators.
The complete engineering of the systems mentioned above has been carried out in-house by Bedeschi engineers. All the critical components are manufactured in Bedeschi’s workshop in Padova, Italy under strict quality control right from the raw material procurement to final dispatch. Bedeschi strives for excellence not only in the field of offshore transshipment, but for shore-based facilities like in Columbia,Turkey, Italy and Israel.
Gaining a strong position in the offshore stevedoring & transshipment market
50 million tonnes of dry bulk commodities have been handled in the last 12 months through the fleet of floating terminals designed and commissioned by the Italian firm Logmarin Advisors (part of Rina group) which has proved to be reliable and efficient.
Over the last years offshore transshipment solutions, as an alternative to shore-based infrastructures, have generated new interest as end users discover the potential opportunities this technology can offer.
The logistic chain is the single most important service function that any business continuously strives to enhance. Improvements in the logistic costs allow companies to gain and maintain a competitive edge, as any savings on the supply chain costs reflect on the competitiveness of the supplier and consequently on the final product price.
Nowadays, dry-bulk dealers may have many difficulties on exporting/importing their commodity as open land next to deep water is not easily available and so, in these cases, floating terminals can provide a viable economically solution to overcome such restrictions and give a real boost to the efficiency of the commodity supply chain.
Logmarin Advisors is specialized in shipping logistics for commodities such as coal, agri-bulk, bauxite and iron ore and it has been involved in most of the major transshipment operations around the world, providing different logistical solutions, both onshore and offshore.
For Logmarin 2012 was a year of strong progress and achievements in the supply chain sector — over 50mt (million tonnes) of dry-bulk commodities have been exported/imported in the last 12 months through the 17 floating terminals developed by Logmarin. Each of these has proven to be reliable and efficient thanks to the high performances, exceeding both the contractually agreed performance and expectations, allowing Logmarin to maintain mutually beneficial long-term relationships with its clients.
Nowadays, four floating facilities of different sizes and characteristics are at various construction stages, one unit at conversion stage and one at design stage. Such results show Logmarin’s remarkable hand at this market niche and its strong position. In spite of being a small
company, which includes professionals with wide experience in all facets of naval architecture, marine and civil engineering, as well as staff with marine master background and technical/operative experience, many world class commodities suppliers such as Anglo, Marubeni and Vale; end users including Japan Power, ENEL and Kepco; logistics services providers such as KSA, Mitra Swire CTM and RockTree have opted for Logmarin’s design to design or to make more efficient their commodity supply chain.
SOFTWARE AND HARDWARE
When planning a new project development or the improvement of an existing one, Logmarin’s aim is to work side by side with its clients to produce tailored solutions suiting the specific client’s needs rather than only suggesting general answers. For that reason, Logmarin’s service starts from the project outset, with a comprehensive feasibility study and examination of the realities of the requirements, passing through the design stage and the identification of bottlenecks, studying the different ways to overcome them, until the final implementation and commissioning.
Solutions for the logistics supply chain are almost unlimited, therefore it is necessary to produce a solution delivering value to the client and based on a solid knowledge of the market and of the technical and operative expertise. In order to make the customers more aware of the advantages arising from a global view of the supply chain and to support them in their decision- making process, Logmarin has customized a commercial software tool to analyze the key resources of the end-to-end supply chain.
The customized Dynamic Supply Chain Simulator Software (Log.Des) is a powerful tool which enables the companies to create a real and accurate model of their end-to-end logistic process in a dynamic-animated computer model and then evaluate alternative ‘what-if?’ scenarios to identify the optimal solution and to explore the potential changes’ effects on service, costs, sustainability and risk.
Projects in Indonesia, Papua New Guinea and Australia have already benefited of Log.Des results.
As supply chain design is pretty much like a ‘human process’, it is not enough to simply purchase or develop a software tool or to let specialized software simulation companies model your supply chain, without having a specific and exhaustive awareness of what really happens in the reality.
THERE IS NO ‘ONE-SIZE-FITS-ALL’ SOLUTION FOR TRANSSHIPMENT OPERATIONS To serve its customers with a wide variety of products and services whenever is possible or required, Logmarin — together with top-class crane supplier Liebherr and Bedeschi, the Italian conveyor system and storage facility specialist — through its strategic alliance Bulk Logistic Landmark (BLL) can provide advice, design, engineering and cargo handling facilities for storage, shore terminal and floating terminals.
The experience and the know-how of the three companies
FC Vittoria at Adang Bay (East Kalimantan) approaching a cape size for coal loading.
have been already effectively and successfully deployed.
EXAMPLES OF REPRESENTATIVE PROJECTS:
The Toros shore terminal.
A project developed for a coal terminal located in the Bay of Iskenderun, in Turkey which brought to the upgrading of the existing terminal by fitting two new travelling cranes and hoppers to enhance the terminal discharging capacity. The terminal now has the capability to unload coal from the largest post-Panamax vessel at an average daily rate exceeding 25,000 tonnes.
The FT ‘Princesse Chloe’
The floating terminal devised and designed on behalf of Mitra Swire CTM operating in Indonesia, which is capable of loading over 800,000 tonnes of coal per month. At the time of writing, the Chloe was about to cross the threshold of hundred vessels loaded since April 2011 (including 23 Capes), with a daily average loading rate exceeding 53,000 tonnes.
The ‘Ore Fabrica’ — floating hub.
The world largest floating terminal delivered in February 2012 and operating in Subic Bay, Philippines, has a 285,000-tonne buffer storage transshipper, equipped with Liebherr’s cranes and Bedeschi’s conveyor system and travelling shiploader with a design capacity of 5,000tph (tonnes per hour).
VALUE ADDED ADVICE, DEVICE AND DESIGN
Logmarin team deals with their clients with three key success factors:
1 The right technology (Log.Des); 2 The experience acquired in the field and the feedback received from on-going operations; 3 The team-working capability and experience synergies with their clients.
The results that Logmarin has reached are the proof of its professionalism and long experience, and its ability of providing customized efficient and reliable solutions developed on the actual experience gained from on-going operations. Such operational experience is not available in standard engineering firm.
As such, the Logmarin team concentrates all efforts to compete against the commodity supply chain bottlenecks of its clients. In addition to the more traditional markets, Logmarin is involved in transshipment projects where efficiency and price are not the only decisive factors but higher environmental and quality standards are fundamental requirements.
MacGregor transloading technology serves India’s booming bulk markets
Growing coal import and iron ore export industries in India are benefiting from MacGregor’s ability to provide efficient, reliable and flexible transloading system solutions.
From a technical perspective, the keys to a successful bulk handling operation are flexibility, reliability and continuity. Combining these efficiently ensures not only the profitability of an operation, but also limits its environmental impact.
To achieve the highest efficiency rates it is important to tailor the technology to an operation, although this has historically been limited by available port facilities accommodating either an operator’s desired size of vessel or the self-unloading installation. Transloading is a particularly effective way around this problem.
For transloading dry bulk materials, MacGregor offers complete solutions for floating cranes, transfer terminals, transloading ships and self-unloading barges. Currently benefiting from these are the growing Indian coal import and iron ore export industries. “Whether feeding India’s supply and demand markets or exporting iron ore, the whole supply chain has to be an efficient operation,” says Ajay Jalali, MacGregor’s marketing manager in India. “This starts from mining, to loading mother vessels, and unloading on the East and West coast of India. Due to limited port facilities there is an increasing move to unload imported coal into smaller barges using transloading terminals, transloading ships and floating cranes.”
Coal is a difficult commodity to handle and requires tailored technology to overcome issues such as the oxidation of coal at storage yards, flow problems during rainy seasons, blockages at chutes and bunkers, spillages, the problems associated with having combined mixes of differently-sized and different quality coals, and the abrasion of coal handling equipment. “Cargotec is able to overcome all of these issues,” Jalali says.
MacGregor has delivered its first order for a complete transloading system to India. The combined transfer terminal, for a leading Indian iron ore exporter, M/s.VM Salgaocar & Bros. Pvt. Ltd., is designed for transloading iron ore into Panamax-sized vessels.
MacGregor scope of supply comprised: two K3028 heavy- duty grab cranes; two hoppers; a belt conveyor system, with a rated capacity of 2,000 tonnes per hour; and a telescopic reversible ship loader. The transfer terminal M.V.Vishal Hira is currently in Goa and will be undergoing final product trials in March 2013.
“The system is tailor-made for the customer to suit its intended operations in Goa,” notes Anders Berencsy, Cargotec’s sales manager for transloaders at MacGregor. “Our customer wanted a solution with the responsibility for the main functions of the systems from one supplier. We are the only company able to supply cranes, hoppers, a conveyor system and a shiploading boom for the transloading system. This is essentially all the equipment that is needed to handle the bulk cargo throughout the entire transloading process.”
In Nov 2012 floating Crane Barge M.V.Narmada Jalprabha owner by M/s.Ahiliabai Sardesai was commissioned with MacGregor K3035 heavy duty crane, the floating crane barge is designed to handle both coal and iron-ore. The barge is currently used for unloading coal from Capesize vessels in the state of Gujarat. In October last year, MacGregor received an order for a four-
wire rope K5036 heavy-duty grab crane from India. The 50- tonne capacity crane will be delivered by August 2013 to an Indian shipyard. The crane will be integrated onto a floating barge, which is expected to be operational by the end of this year.
“This will be the largest capacity bulk handling floating crane
in India,” highlights Ajay Jalali, MacGregor’s marketing manager in India. “Our customer wanted higher capacity coal unloading from Capesize vessels. It chose the Macgregor K5036 crane based on its capabilities, operational performance and the fact that it is backed by a strong service presence in India.
“Until now the largest floating cranes available in the country have been limited to a 35-40 tonne SWL grab operation, so the K5036 offers a substantial increase,” adds Jalali.
Coeclerici saves the day after major storm damage at the Port of Taranto
On 28 November 2012, a tornado with winds up to 250km/h hit the South of Italy and, in particular, the city Port of Taranto, writes Capt. Giordano Scotto d’Aniello, Head of Commercial Department at Coeclerici Logistics, Milan, Italy.
The storm caused extensive damage to the area, bringing down a chimney stack, a warehouse and a lighthouse at ILVA (Europe’s biggest steel mill and a major employer in Taranto) factory docks. In addition to the human tragedy — one person died and 40 were injured — the storm caused heavy damages to the port area. Part of the equipment used to load and unload ILVA commodities was destroyed, with disastrous consequences to the activities of the steel mill.
Among the various vessels awaiting to carry out commercial operations at the berth were two ships in particular. Both were loaded with about 300,000 tonnes of iron ore, and were forced to anchor as a result of the storm damage. They were unable to approach the dock (the only single dock able to accommodate
units of that size had suffered heavy damages), and were waiting to be unloaded and to deliver the cargo essential for the proper functioning of the factory.
For the complex steel mill system to operate, it needs a regular daily supply of iron ore pellets. If these were to run low, this could create huge economic damage and result in the closure of the whole blast furnace at ILVA.
While ILVA did all that it could to repair the damaged port infrastructure, an urgent solution was needed to allow ILVA to receive a sufficient quantity of iron ore to keep the steel mill running and to prevent the closure of the whole production chain. If this were to happen, a complex procedure would be needed to reactivate it, with enormous capital loss.
ILVA immediately contacted Coeclerici requesting a logistic solution to solve the difficult situation that it was in. It was essential to find a rapid solution. After an internal study, Coeclerici suggested that the only viable solution was to carry out a transshipment operation using the company’s FTS (floating transfer station) Bulk Irony, which was then operating in the Piombino area in Italy, about 600 nautical miles from Taranto.
The initial plan was to relocate the Bulk Irony to Taranto and to perform the transshipment operations in the area within the port. A thorough evaluation of the logistics and the authorizations needed for such an operation at the Port of Taranto took place. It was decided that the operations should take place in Piombino, where Coeclerici has been authorized since 2003 to operate within a ‘duly authorized transshipment area.’
The cargo of ‘Tubarao blast furnace pellets’ that were essential to prevent the closure of the blast furnace was ‘stored’ in the Rigel VLOC (very large ore carrier). The Rigel is a giant of the sea — 300,000dwt, 327m LOA, beam 55m, and was immediately redirected to the Piombino anchorage for the lightening operations.
ABOUT THE ‘RIGEL’ OPERATION
The vessel has six holds and each of them can store up to 50,000 metric tonnes (like a Supramax vessel!). The plan was to lighten as much cargo as possible, and to reload it into shuttle vessels of about 28,000dwt, supplied by ILVA, which would then be transported to Taranto, making it possible to discharge at Taranto’s only ‘surviving’ berth.
However, the transshipment point is an area that is only 0.6nm in radius. This limited the safe anchorage of both the shuttle vessel and the Rigel at the same time. Therefore, the FTS Bulk Irony was obliged to lighten the Rigel from both the port and starboard sides, leaving the shuttle vessel always moored alongside the anchored mother vessel.
The cargo that the FTS Bulk Irony helped to lighten made it possible for the ILVA steel mill to continue operating while operations at Taranto were being restored, without having to shut down its activities.
SMOOTH RUNNING...
The smooth running of the operations was achieved through very close interaction between the onboard operators and Coeclerici’s shore personnel. The success of the project was attributed to the Master’s competence and to Coeclerici’s 35
years of experience in logistics operations. The operations carried out by the Bulk Irony are a further
example of the flexibility of a ‘floating transfer station’, which can perform the same operations both ‘offshore’ and ‘onshore’, like a port loading/discharging facility.
The FTS Bulk Irony is not new to this kind of practice which goes outside its regular operations. In fact, during its first decade in Piombino, the unit was used also as a ‘back up device’, supporting the shore facilities in any emergency events.
ABOUT THE FTS ‘BULK IRONY’
Coeclerici Logistics developed and designed the FTS Bulk Irony, which has been based on many years of experience in operating floating cranes and floating terminals in a wide variety of working and environmental conditions. The Chinese shipyard Nanjing Xinhua constructed and assembled the Bulk Irony under the direct supervision of Coeclerici Logistics and Coeclerici patented the advanced and innovative FTS design. After a long journey of 8,603 nautical miles, the Bulk Irony arrived at Piombino on 29 December 2002. During the initial commissioning period in which two lighterage operations were carried out, the FTS Bulk Irony, immediately exceeded the expecteddailyunloadingrate. TheresultisthattheFTS became an essential and cost effective link in the Lucchini production chain.
The FTS Bulk Irony overcomes Piombino’s draught restrictions by lightening part of the raw material shipment (both coal and iron ore) offshore Piombino’s port, thereby reducing the overall sea freight charge. Once lightened, at a rate of about 1,000tph (tonnes per hour), the ocean going vessel and Bulk Irony discharge the raw material onto the jetty. The annual tonnage to be transshipped for Lucchini is approximately 500,000 tonnes, allowing Bulk Irony to have a ample spare capacity, which can be utilized by the other users of the Piombino port.
The FTS Bulk Irony is self-propelled and is therefore capable of short coastal trade if and when required. In addition to dry bulk commodities, the FTS is also capable of transshipping steel coils on roads and providing intermediate temporary storage. The Piombino Port Authority regards the FTS facility as an important instrument to further enlarge its activities and to attract transit cargo to north and central Italy.
‘GREEN HANDLING DESIGN TO OPERATE’
Coeclerici is aware of the impact that dry bulk operations may have on the environment. Handling coal and iron ore can cause environmental pollution, both in air and sea if the utmost care and precautions are not taken. After years of experience in such operations, Coeclerici Logistics is committed to the highest environmental standards and has taken the onus of the maintenance of environmental standards on itself.
Bulk Irony’s lighterage operations are carried out in a place which is at a mere step from the Island of Elba and from the Parks of the Val di Cornia, which are rated amongst the best for Italian tourism and historical resorts (from Etruscan times). For these reasons, the area has become an internationally famous tourist resort and the Blue Flags awarded by the European Community indicate an unpolluted sea rich in rare fish species. The environment standards required to operate in this area are extremely stringent. Accordingly, the FTS Bulk Irony has an environmentally friendly design, approved by the local authorities such as Health & Safety, Environmental and Coast Guard. The facility also meets the requirements of international classification societies such as IMO, MARPOL, ISO 14001 and the environmental ‘EMAS’ registration.
The engines and generators meet the most demanding emission control regulations and have a highly fuel efficient and economical combustion system. Coal and iron ore dust emissions and cargo loss are prevented by custom-designed devices, according to Coeclerici’s recommendations. These include: spillage-free grabs; receiving hoppers equipped with spill plates to avoid spillage into the sea; windbreaks to avoid airborne pollution; and water spray systems. Fully enclosed commodities transfer points; conveyor belts and loading booms as well as settling tanks and sewage systems to treat dirty water are also fitted. All personnel are educated and trained to conduct their tasks in an environmentally responsible manner. Nowadays Coeclerici Logistics, which operates with its units worldwide, has attained a formidable leading position in the field of dry-bulk logistics.
One of the strong points of Coeclerici Logistics ‘business’ is that it is market-oriented and focused on the real customer’s needs. “We do not sell standard solutions, because there are no standard clients and bottlenecks,” and this is proven by the continuous success of Coeclerici Logistics with new units delivered to clients during the past couple of years .
- Bulk Zambesi and sister vessel Bulk Limpopo: these units have been in operation in Mozambique since 2011 and 2012, respectively, and are both employed by Vale to overcome the draught restriction at Beira port. Both transshipment units, fully designed and built by Coeclerici Logistics, load at Beira berth and transport their coal cargo to a suitable deep water anchorage off the coast, where there are no draught constraints and where the coal is transferred into ocean going vessels (OGV) up to 180,000dwt by means of a sophisticated loading system installed onboard. Bulk Zambesi and Bulk Limpopo are each duly equipped with heavy duty cranes, grabs, a belt conveyor system capable of transshipping at a peak rate of 5,500tph, and state-of- the-art gears allowing a throughput of around 12mt (million tonnes) of coal per year. The two vessels are in compliance with the latest international code resolutions for ship’s safety and security, protection of crew and of the environment.
- The FTS Bulk Java, sister vessel Bulk Borneo and the FTS Bulk Celebes have been employed by PT Berau Coal to perform coal loading operations at Muara Pantai anchorage in Indonesia to support the client’s export throughput. The units have been custom-designed and built, by Coeclerici, to solve the logistical problems inherent in a coal production process that is expected to increase to 30mt (million tonnes) in the coming years. The FTS Bulk Java and Bulk Borneo came into operation in 2011 and 2012 while the Bulk Celebes was delivered to the client in January 2013.
- The three units will soon be joined by the FTS Bulk Sumatra, scheduled to be delivered in July 2013. Coeclerici Logistics operates also in Venezuela with the FSTS (floating storage and transfer station) Bulk Wayuù, in the Black Sea with Bulk Kremi I and in Indonesia with the FTS Bulk Pioneer.