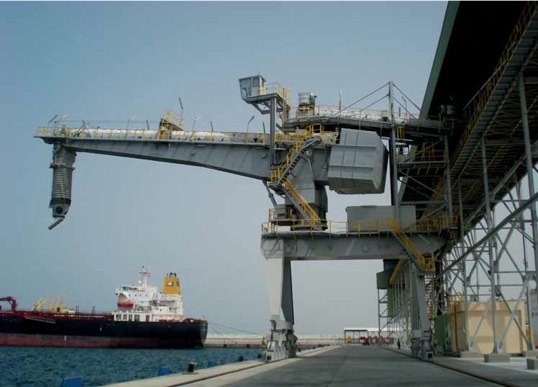
Automation and instrumentation for material handling from a single source
Klaipeda Stevedoring Company (Klasco) in Lithuania continues to invest in the expansion of its existing terminal handling capacities. It has therefore ordered from German SMB Group, based in Quickborn near Hamburg, another high throughput state-of-the-art shiploader for the loading of fertilizers at its deep water quay.
“We expect to have the shiploader commissioned by December 2013,” announced Andreas Heckel, managing director of SMB Group. SMB delivered the first shiploader to Klasco about six years ago. “It has proven its investment worth,” Heckel continues. “Even though the first shiploader was only constructed for one- or two-shift operation, the significantly increased handling volume for fertilizers had the shiploader running nearly around the clock in the last two years. There were no problems from it at all.” The enormous strain from wide temperature fluctuations and weather influences in the harbour of Klaipeda and the highly corrosive effects of the fertilizer shipped were added factors weighing on the shiploader. “The shiploader system was really strained, but ran reliably. The installed technology convinced Klasco such that we have now been awarded with a contract to supply a second shiploader as well,” says Heckel proudly.
LOADING CAPACITY OF UP TO 2,000TPH
Different products can be loaded from four separate docks into Panamax class bulkers at Klasco’s fertilizer handling facility. The storage capacity is 120,000 tonnes and the possible annual total turnover is approximately 2mt (million tonnes). The quay is of a suitable length: it is about 264 metres long and has a water depth of 14 metres. The fertilizers mainly arrive from Russia by train, are product compatibly unloaded by Klasco (up to 1,600tph [tonnes per hour]) and put in interim-weather protected storage silos. High-performance conveyor facilities then load the fertilizers via the current SMB shiploader onto bulkers at a loading capacity of up to 2,000tph. “The new shiploader will even have a capacity far in excess of 2,000tph,” Heckel reports. Additionally, Klasco will also invest in the construction of new storage capacities.
The shiploading division of SMB Group can look back at two decades of experience in project planning, design and construction of shiploading systems. Within this period around 100 systems have been delivered, ranging from stationary loading systems to mobile facilities travelling along the quay on rails. All important components and assemblies are produced by SMB in-house and tested in detail before delivery of the systems. The shiploaders are designed for bulk or bagged material loading facility, or as combined bulk and bagged material loading facility, depending on the customer’s requirements.
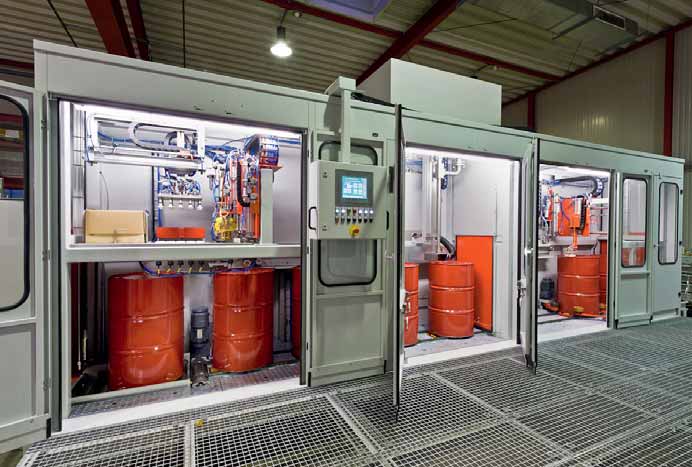
HIGH PRODUCTION CAPACITY
SMB Group has decided for a high percentage of in-house production capability. In this way, customer requirements are spontaneously and effectively implemented whilst maintaining a high quality. The internal design and production of mechanical and electrical assemblies forms the basis for the high level of vertical integration. Heckel:“This ensures best reliability in quality and delivery time for our customers.”
“We see ourselves as complete solutions provider for all tasks in which material must be filled, stored, internally transported and finally shipped,” Heckel defines the supply range of SMB Group. “Our customers have the benefit of getting transport and filling facilities, palletizing facilities or complex shiploaders, reclaimers and conveyor technology from a single source. All modules are not only perfectly aligned with each other, but also with the characteristics of material to be transported.”
LOGISTICS AND BULK LEVEL MEASUREMENT
SMB Group comprises two companies: SMB International GmbH and MBA Instruments GmbH. “Two brands — one idea,” Hans-Heinrich Westphal describes the group’s philosophy. He manages MBA Instruments GmbH together with Andreas Heckel. “SMB and MBA have focused their business activities in the company claim ‘Material Handling’. Planning, development, manufacturing, global distribution and service not only of the highly complex, automatic loading and storage systems, but also of level measurement technology are part of our product range.”
The product offering from MBA consists of many components with integrated measuring principles and a wide application range. Some examples of this: the product range includes membrane switches that are used as limit switches for bulk materials. The switching process takes place when slight pressure is applied by the bulk material on the stainless steel membrane. A micro switch is operated by this and triggers an electrical signal.
ROTATING PADDLE TECHNOLOGY: FOR THE FIRST TIME WITH STEPPER MOTOR The rotating paddle measuring technology is independent of the properties of bulk material. The measuring instrument type MBA200 for example is used as a full, demand and empty indicator of bulk material both in large storage silos and in small containers. In loading chutes and conveyor facilities, it signals a blockage in the product flow in time. “While a synchronous motor turns the paddle in the established rotating paddle device series MBA200, we have used the first stepper motor in the new device concept of the MBA800 series,” Westphal explains. “This was based on the MBA-owned patent of the magnetic slip clutch. Its function has in the meantime become an integral part of each stepper motor. The logical next step was using the adjustable parameters of this motor type to enlarge the application diversity of this measuring technology and an additional registration for a newpatent.” Speed,torque,triggertime,switchingdelayand other parameters can be adjusted individually to reach different applications.
“The new device series is complemented by the special version MBA808 with its double function ‘levelling and measuring’,” as Westphal reports. “To completely utilize the silo capacity, the bulk level measuring device MBA808 flattens the angles of repose. The new stepper motor version is strong enough to turn the extremely long and slightly bent paddle arms of the device and thus push aside light to medium to heavy bulk materials such as powder,
granulate or pellets.” Only when the flanks of the cone are filled with the bulk material and the paddle is entirely covered with the bulk material and cannot turn anymore, will a ‘full’ signal be sent. The vibrating paddle measurement technology with a patented single rod is also mainly independent from the fillingmaterial properties: the MBA700. This procedure is particularly suitable for powdered bulk material and has mainly become established over the vibration forkmeasuring technology. The MBA 369 perpendicular system was constructed for use in extremely narrow silos. It may be used for the semi-continuous level measurement of all bulk material. A so-called sieve weight can even be used to measure the height of sediments under water or other liquids. Radar impulses reflected by the material are also the basis for continuous measurement. The essential benefits: the MBA radar products work contact free and can be used for the bulk level measurement of stockpiles.
“The new shiploader for Klasco is equipped with level measuring devices by MBA,” Westphal says. Four devices of the series MBA220 are used here. They prevent the fertilizer from blocking the cascade headchute if the conveyor output is too high and thus secure the high reliability of the entire loading process.