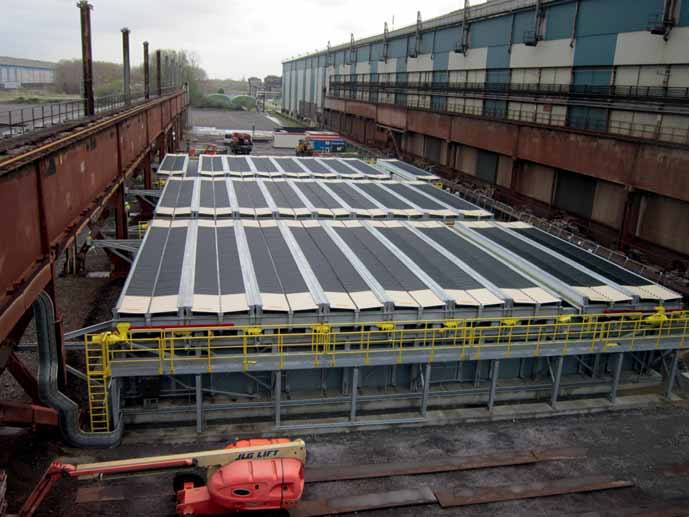
N.M. Heilig B.V. is a manufacturer of durable installations and components for the international dry bulk industry. The company offers equipment to satisfy almost every need related to the transshipment and storage of material in dry bulk terminals.
N.M Heilig B.V. has over 30 years of practical experience, and its equipment is all of a high quality. It specializes in the design and construction of elaborate installations. It offers equipment for loading, unloading, transporting, crushing, categorizing, washing, sieving, separating and processing dry bulk materials.
About 250 highly skilled and enthusiastic employees divided over five subsidiaries within Europe serve the company’s clients. Most installations are supplied as turnkey solutions, but individual components are also supplied to many leading companies in the bulk handling industry.The company delivers both mobile and fixed-position systems.
PROJECT: MOBILE SCREENING PLANT
Recently N.M. Heilig B.V. has delivered a turnkey solution for the screening of coal on location.
In the past this customer was using a fixed screening plant centralized on the terminal. Due to the fixed base of this screening plant, there was a lot of internal transport needed to and from the screening plant. The transport costs associated with this set-up were high. To reduce these costs, when the installation needed replacement, the customer chose to replace the fixed installation with two mobile installations.
The first of these custom-built screening machines was delivered and put into operation in November last year.
The screening plant (see picture above) is fed by a wheel loader. Through a mobile hopper, the material is brought to the first conveyor, the material surpasses the ironing step and then is divided into fractions by the screen.
This screen makes three fractions with a capacity of 350tph (tonnes per hour).
PROJECT:‘THERMAL ROOMS’
For Holland’s biggest steel producer, N.M. Heilig B.V. is currently involved in the design, production, assembly and implementation on site of three so-called ‘thermal rooms’. Each room is a rectangular box construction which is covered by nine big movable hatches on top of each room, where the producer will stock just-produced hot carbon-steel materials. The materials will be loaded into the ‘thermal room’ by gantry cranes. The rooms are constructed with robust steel structures, concrete and insulation. The hatches are rail based. A lock system device for the shutters is installed, operated by electrical hydraulic accumulators and complex operating software.
Each room can be filled with 320 tonnes of steel slabs. In total up to 1mt (million tonnes) of steel slabs can be placed in the rooms to prevent rapid cooling and loss of quality.
Only two hatches can be moved variously and simultaneously, the location and opening of these hatches will be determined by the operating system. After the location and opening is set, the accumulator unlocks the lock system and detaches the nine hatches into two pairs of hatches to create an opening. There are eight combinations to open the shutters, for required logistic reasons of the crane movements.
Open or closed position of the shutters and synchronous operation will be detected and managed by electrical sensors. In normal operation, the time to open or close the shutters will be a maximum of 14 seconds, and occasionally this can be speeded up to seven seconds. This speed, in combination with a total movement of the enormous weight of approximately 10 tonnes per hatch (ca. 45m2/hatch), is a challenge which N.M. Heilig B.V. will overcome.
This project was put into operation in November last year, and is currently running well. With this investment the customer can boost production, guarantee the steel quality and reduce costs by preventing the steel slabs from cooling down, so limited energy is needed to heat up the slabs before the slabs are rolled into coils.