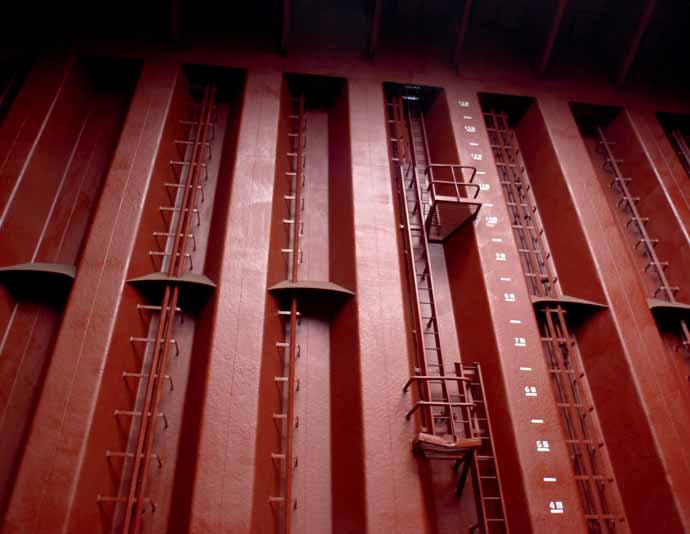
Two most significant developments, both occurring in the first decade of this millennium, posed a big challenge to marine paints manufacturers across the world. These required of manufacturers to make a complete break with a more than 40-year-old practice of using organo tin tributyltin (TBT) compounds in the making of antifouling coatings for sea going vessels. Under pressure from governments across the world, marine biologists and civic society, the International Maritime Organization first put a ban on production and sale of compounds using TBT compounds in January 2003 and then disallowed their presence in ship hulls effective January 2008.
Leading paints manufacturers responded well to the challenge of finding alternative compounds to TBT in making fouling control coatings by providing large funds for research and development. An outstanding example of the industry’s new thrust on R&D found expression in International Paint, an Akzo Nobel outfit, opening a state of the art marine coatings research centre in Singapore. The centre, which gets liberal funding from International Paint, is in the forefront of making technology breakthroughs. This is once again proved by the centre coming up recently with two new breakthrough fouling control products. Both have been well received by shipyards all over the world.
In the first place, what needs to be understood well is why ships need anti-fouling coatings at all. Marine fouling happens because of settlement and growth of algae and invertebrate animals on the surface of submerged portions of ship hulls and harbour installations. Running ships will become a more expensive proposition and with major disturbances caused to the environment in case fouling deterring coatings are not used. A scientific study has established that in the absence of application of anti-fouling coatings, ship fuel consumption could be up by as much as 40%. This will translate into total global fuel consumption by vessels climbing to 500mt (million tonnes) a year from the present 350mt. What is more, ships as they move from port to port are emitting huge quantities of CO2 and SO2. The least that the world can put up with is more greenhouse gas emission. Application of good quality anti-fouling coatings allows ships to run at good speeds. This in turn helps in reducing ‘operational, commercial and environmental costs’ of running ships.
The two new coatings, developed at the Singapore R&D centre of International Paint and creating new waves of interest among shipbuilders are (i) Intercept 8000 LPP. The new biocidal linear polishing polymer antifouling allows long-term performance for in-service periods of up to 90 months. (ii) Intersleek 1100 SR is the first biocidal-free fouling control coating featuring a unique patented slime release technology. This controls micro fouling on ship hulls. The performance is maintained throughout the docking cycle. Biocidal-free coatings work by providing an uncommonly smooth, slippery, low friction hull surface. Naturally, fouling organisms find it difficult to stay attached to the outer hull surface. Some stubborn organisms, however, still do, but only manage to do so weakly making it easy to remove those. In the other types of coatings, fouling organisms are prevented from sticking to underwater portions of outer hull surfaces through controlled release of biocides. Cuprous oxide is the principal biocide used to stop barnacle, an animal fouling, from settling on the surface. As for stopping the growth of algal, a weed, cuprous oxide needs reinforcing by rapidly degrading co-biocides. The latter do not bio-accumulate in marine environment.
An official of Indian Paints Association says “success in marine paints business demands of manufacturers coming up periodically with coatings for external and internal surfaces of ships that would last longer in an environment protective way. Equally importantly, shipyards want paints producers to be involved with them from planning stages of a new vessel building and throughout its life. Shipyards are showing distinct preferences for paint makers with capacity to offer consultancy in an area with significant bearing on vessel life and maintenance cost. Big investments in R&D and rising raw materials bills have pushed up prices of marine protective paints. But rapid quality improvement resulting from R&D breakthroughs in groups like International Paint, Jotun of Norway and Nippon Paint of Japan continues to bring down the cost of painting over a vessel’s total seaworthiness period.” The official further says a noticeable feature of recent times is global marine paints leaders headquartered in Europe reinforcing their presence in China and Southeast Asian countries by opening new factories and expanding the ones in operation and equally importantly doing R&D work on marine paints in those new locations.
International marine paints leaders know their future growth will be decided in a very significant way by the kind of presence they have in Asia. Stack up the shipyards in China, South Korea, Japan,Taiwan and India and you have close to 90% of global new building capacity. Furthermore,Asian countries are where an overwhelming majority of vessels will be docked for repairing and painting jobs. China like in so many other enterprises leads the world in the number of dry docks and dry dockings. No wonder then International Paint has opened its new global marine coatings headquarters in Singapore. The move is one more proof of indispensability of physical presence in select Asian centres to be of relevance to the region’s shipping industry. According to International Paint’s director of marine coatings Oscar Wezenbeek, “headquartering our business [marine coatings] in Singapore will further enhance our global position as it will facilitate growing our market share in Asia- Pacific... Asia will be an increasingly important market for us in the future.” The Akzo Nobel subsidiary arrived early in China in 1990 with its International Paint & Shanghai Co, which is rapidly growing manufacturing of marine coatings and coating powder for use in new building, ship maintenance and repair and on board maintenance. So much water has flowed down the Tyne river in England’s New Castle where the origins of International Paint stretch back 120 years. Today, European shipyards are mainly engaged in building very special types of vessels for commerce (LNG transportation) and defence.
Jotun too with two manufacturing units in Guangzhou and Zhangjiagang has a growing profile in China where also it has got a very active regional R&D centre. Another Jotun factory for marine coatings production at Qingdao in Shandong province will soon be ready for commissioning. An official of Jotun China is on record saying “we recognize that we are not the first to
enter the Chinese market where the demand for marine paints of all types is growing at a rate faster than in any other country. But our sustained investment in production facilities and the focus of our local R&D centre to develop products in line with Chinese requirements are helping us to make up for the lost time. We are ambition driven to become the best.” Success in marine paints business demands of producers to be present where the market is, since their involvement is required from conceptualization of new shipbuilding and through a vessel’s entire life. So it goes beyond supply of coatings to offering of a kind of consultancy to vessel builders.
European companies were early to realize that they must be present in strength in Asian countries in order to maintain a good share of a market where the future is. What they have not lost sight of is the capacity in particular of some Japanese paints groups like Nippon Paint to throw challenges to their peers from other continents in technology breakthroughs and product quality. Hasn’t Nippon Paint played a pioneering role in developing anti-fouling paints sans organic tin that harms marine life? Fouling organisms find it difficult to stick to ship hull if the surface remains extraordinarily smooth. Nippon Paint kept slippery skins of dolphin and tuna in view as it developed anti-fouling paints. Naturally, the market has responded well to these paints.
Even while the Indian market for marine paints is still modest in size, the future demand driver there could well be the maintenance and repair (M&R) segment. International groups are taking care of Indian market requirements through their local offices and chains of dealers. But going a step forward, Hempel Paints of Denmark, however, is to build a marine and protective coatings plant in the western Indian coastal state of Maharashtra. Besides targeting a bigger share of the local Indian market, Hempel will use the products from Maharashtra plant to sell in other south Asian countries. With foreign groups becoming active, Indian companies with marine paints in their portfolios have realized that their staying in this niche segment will depend on their ability to acquire new technologies from abroad. Not an easy proposition though.World leaders in marine paints after having pumped in big new funds in R&D since the beginning of the new millennium will not be disposed to either sell technologies or become partners in joint ventures with Indian groups.
The growth rate of the marine paints industry is linked to activity levels of new building and M&R. New building in turn is influenced by the state of world economy and world trade. The International Monetary Fund is lowering its growth forecasts for nearly all rich countries, including a 0.3% contraction for the euro zone.While the industry growth has slowed since the ruinous 2008-09 recession, paints manufacturers have to put up with cost inflation of raw materials like epoxy resins, titanium dioxide, solvents and metals. The market being not in great shape, paint manufacturers are not in a position to pass on incremental costs on account of raw materials to their clients. Margins have, therefore, come under pressure. It will be some time before marine paints business returns to the vibrancy of pre-recession days.
Caring for cargo holds with coatings from Hempel
No other part of a ship receives the same kind of battering as a cargo hold. The profitability of a bulk carrier is highly dependent on the long term durability of the coating used in its cargo hold. Angular dry cargoes like iron ore, coal, coke, bauxite, rocks and scrap iron can inflict severe damage to the cargo hold coating from high speed impact during loading, mechanical impact and abrasion during discharging and cargo gouging from cargo settlement during ship movement and sailing. Carriage of warm cargoes can soften the coating and reduce its mechanical resistance, so high thermal resistance is needed. In addition moisture in contact with acidic cargoes can form a highly chemical corrosive environment in the cargo hold and all of this the coating will need to protect against.
HEMPEL, a specialist in developing durable abrasion and impact resistant epoxy coatings, has recently launched a new cargo hold coating. Group Marine Product Manager Michael Aamodt comments;“HEMPADUR IMPACT 47800 is our newest addition to our dedicated cargo hold coating range. The coating is developed to offer uncompromising high performance against dry cargo abrasion, impact and corrosion resistance. Hempadur Impact not only offers superior impact resistance to prevent ‘shooting’ damage from high speed loading in the cargo hold but also has a high glass transition temperature to keep the coating hard and resistant also when exposed to warm cargoes.”
Hempadur Impact has excellent application properties; it dries and cures quicker than similar coatings on the market, and can carry hard cargoes after only three days’ curing at 25°C. This low VOC pure epoxy coating is conveniently available in grey, red and aluminium shades. Applicable year-round to steel surfaces prepared to minimum Sa 2 the coating offers a smooth and easy to clean surface between different dry cargoes.
Extensive benchmark testing of Hempadur Impact on Hempel’s state-of-the-art ‘coal cargo test-rig’ in comparison with comparable cargo hold epoxy coatings found in the market, shows that the coating offers superior protection. With a 7.5- year major repair interval it enables shipowners to extend periods between repairs — and will reliably reduce the vessel’s operating costs to deliver exceptionally strong return on investment.
HEMPADUR IMPACT 47800 at a glance;
- 7.5-year major repair interval;
- 76% volume solids;
- VOC compliant (below 250g/l);
- certified for carriage of grain and FDA compliant for dry food contact;
- application temperatures: 0°C to 40°C (23°F to 104°F);
- dry film thickness: 2 × 125μm;
- time to carry first hard cargo three days at 25°C; and
- easy to clean between cargoes.
HEMPADUR IMPACT 47800 is a true value for money cargo hold coating that will have a positive impact on a vessel operating costs, whatever the cargo, don’t settle for less.
Ultimately, securing correct surface preparation, paint application, drying conditions and required number of days curing before exposure to hard cargoes will determine the in-service performance and durability against damages.