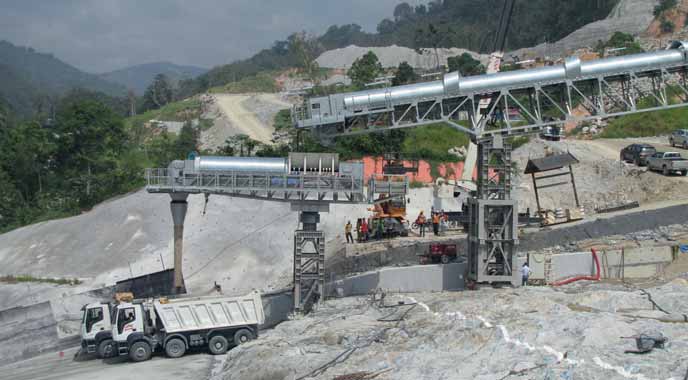
DemcoTECH: optimizing stockyard performance
The overall performance of the bulk minerals export chain is restricted, inevitably, by the poorest performing element in the chain, which could be any one of a number of processes, including transportation, the mining operation or port stockyard export facilities, says DemcoTECH engineering general manager, Paul van de Vyver.
The major function of stockyards is to cater for the cyclical nature of the incoming and outgoing product, combined with the requirement to blend material in some cases. The main problem is the need to accommodate a disparity between the rate of incoming and of outgoing materials — often a result of relatively continuous mine production and scheduled transportation, with the more cyclical nature of the export process, adds van de Vyver.
“Understanding the entire system is therefore required through a holistic design approach, which considers a number of parameters including partitioning to eliminate material contamination, material size, shape of the stockpiles, terrain limitations, stacking methodology, stockyard layout and equipment selection.
“Only then can a solution be provided that is customized to the client’s requirements, whether it be a stockyard for a mine, process plant, power utility, port or terminal — and one which will limit the possibility of the stockyard being the bottleneck in the overall transportation chain.”
Johannesburg, South Africa-based, DemcoTECH Engineering has a successful track record in designing, engineering, refurbishing and supplying stockyards and/or portions of stockyards, both in South Africa and internationally.
DemcoTECH, working jointly with Kantey & Templer Engineers, completed an expansion to the manganese export facility at Assmang Limited’s Cato Ridge Alloys plant in KwaZulu Natal, South Africa.
The project commenced with a concept study and covered the complete range of project services through to implementation of the works. It consisted of three major components, namely refurbishment of the existing tipplers, refurbishment and upgrading of the existing conveyors and, lastly, the supply of a greenfields stockpile and reclaim facility, with an automatic truck loading system.
“The changes to be made to the system were fully evaluated in a feasibility study beforehand, which included a time and motion study on the wagon tipplers,” says van de Vyver.
The stockpile included a new elevated tripper feeding the stockpile with a dust suppression system to providing a safe and environmentally friendly operation. The wagon tippler was supplied with a new side arm charger to eliminate the positioning of rail wagons using a locomotive.
In a major contract award, DemcoTECH was appointed as the materials handling engineering design and engineering company on Vale’s expansion project to establish a regional iron ore distribution centre in Lumut, Perak, Malaysia.
“Work started on the facility in 2010 and the first two 400,000dwt vessels carrying ore to the Malaysian Terminal were off-loaded early in 2014,” notes van de Vyver.
The distribution centre includes an ore storage yard and a marine terminal, capable of handling more than 60 million metric tonnes per year. Iron ore is received from Vale's mines in Brazil for distribution to customers across the Asia Pacific region.
Through a separate contract, DemcoTECH also provided operational readiness services, including operational and maintenance training modules.
“Our success has been based both on our design and engineering expertise and experience, as well as our ability to provide the client with fit for purpose, reliable stacking, reclaiming and blending stockyard layouts and equipment. This includes rail tipplers, versatile conveyor systems for the relevant stockpile configurations for blending, pipe conveyors for enclosed environmentally clean conveying and the selection of the correct stacking and reclaiming equipment. DemcoTECH also designs and supplies sampling plants for these applications.
“When designing a stockyard layout, DemcoTECH uses a number of tools, including simulation modelling, animations which allow the client to visualize the stockyard in terms of real life operating and maintenance conditions, finite element analysis (FEA) to review and audit complicated stress areas on these large machines and also material flow analysis to ensure optimum chute design, ” says van de Vyver.
Bedeschi Group: the value of a team approach
Bedeschi supplies machinery and services to the bulk material handling and mining industries with a specific focus on handling difficult materials, such as sticky clay and coal/lignite, or dry mining and abrasive materials, such as iron ore and other minerals. Furthermore, through its subsidiary, CTP Team Srl, based in Milan, Bedeschi also works in air pollution control.
In the last few years, Bedeschi and CTP have commissioned several stacker, reclaimer and filtration plants in Turkey. Some projects are related to the conversion of electrostatic precipitators into bag filters while others involve new equipment in existing plants or installation in new cement productions lines. The company has also been awarded a range of contracts related to gas filtration systems.
All the supplied bag filters are equipped with SWAP technology (Sonic Wave Acceleration Pulse) for bag cleaning.
CASE STUDY: MADENCILIK VE YAPI MALZEMELERI SAN.VE TIC. A.S
Bedeschi and CTP are taking part in the construction of a new greenfield cement plant in Turkey for a production capacity of 10,000 tonnes per day (approximately 3.3mt [million tonnes] of clinker). Bedeschi will supply all the machinery for raw materials handling, as outlined below and in Table 1.
Premix storage
This comprises two circular pre-homogenization plants with luffing, slewing stacker and bridge, each with a total storage capacity of 50,000 tonnes of limestone and premix for a total capacity of 100,000 tonnes of raw materials.
Additive storage (raw mill)
An additive storage facility comprising 4 × 10,0000-tonne areas will store materials for both the raw mill and the cement mill (iron ore, clay or sand at one side and gypsum and additives on the other).
Stacking will be carried out via a first belt stacking system with a capacity of 2,000tph (tonnes per hour). Iron ore and clay (or sand) will be reclaimed by a 250tph side semi-portal reclaimer. From the additives storage plant, 300tph belt conveyors will transport the iron ore, clay or sand to the raw mills’ feed hopper. Dust filters will be installed.
Additive storage (cement mill)
Gypsum and additives will also be stored in the additive storage plant. A 250tph side semi-portal reclaimer and 300tph belt conveyors will be used to transport gypsum and additives to the cement mills’ feed hoppers. Again, dust filters will be installed for dedusting.
Coal preblending plant
The plant will have a 25,000-tonne-capacity coal preblending plant equipped with two feed hoppers, two drag chain conveyors, two dosing belt weighers and belt conveyors. The belt conveyors will transport coal from the crushing plant to the preblending plant at a rate of 500tph. Once there, a 500tph tripper car will be installed to stack the coal, which is then reclaimed by two 100tph side semi-portal reclaimers. Transportation to the coal mill is via 100tph belt conveyors, and a belt weigher will be installed. To protect the coal mill from metal parts, a tramp iron removal system, metal detector, permanent magnet and a feed hopper with slide gate will be installed.
Dedusting
CTP Team will supply the following: common bag filters for dedusting exhaust gases, evaporation coolers including screw conveyors, rotary gate, control flaps, pipes and ducts, and complete engineering of duct arrangement and the final chimney.
Dedusting system technical highlights
The MKPR low pressure bag filter will be designed with a filtering surface of 21,714m2, incorporating 8m-long filter bags in fibreglass, with PTFE (Teflon) membrane. Cooling water is injected in the evaporation tower at 67m3/h. The fan electrical motor is designed at 2×750kW = 1,500kW. Compressed air consumption for cleaning all the filtering bags 350Nm3/h at 2.5 bar.
Thanks to CTP advanced ECO3 technology, the dust guarantee at the stack will be less than 10mg/Nm3.
Conclusion
Furthermore, ONT Spa, a leading company in the production of bulk material handling systems had been recently incorporated in the Bedeschi Group.
With over 55 years of history and a track of success in different fields, the company is large enough to be able to sustain complex projects, and flexible enough to satisfy customer requests.
The new collaboration between Bedeschi and ONT will guarantee more efficient and reliable solutions for customers in the bulk materials handling sectors. As a result of this, and of CTP’s expertise, Bedeschi is able to meet customer requirements and carry out environmentally friendly, energy-saving projects.
STM Conveyor Systems: flexible solutions for the bulk handling market
STM specializes in the engineering and supply of belt conveyors systems for bulk materials handling facilities. Since 1975, when it started as a family business, STM has provided worldwide innovative integrated solutions that increase efficiency, reliability and cost savings for its customers’ production processes.
Today, STM is able to offer its customers a full range of project services: engineering, fabrication and commissioning. Throughout, STM develops flexible, individual and effective solutions to find the ideal implementation for each customer: this enables it to remain viable in a highly competitive market, with differentiated competitors in every field.
In the STM factory, the quality and the continuous improvement in line, with the best industry practices and standards, are the drivers to meet and even exceed customer expectations.
STM usually performs complete installations in a wide range of industry fields such for example:
MINING
Based on a modular concept that greatly facilitates relocation or expansion as the mine develops, STM’s systems can expedite, optimize and economize the process of overburden removal, processing (crushing/screening),
redistribution and stacking. Conveyors for this kind of application are designed for a lifetime greater than 30 years, with solutions to minimize extraordinary maintenance and downtime risk. STM approaches mines as ‘24-hour production plants’, and is committed to delivering high-value performance and meet customers needs in terms of:
- excellent reliability;
- investment cost;
- delivery time;
- lower operating costs; and
- high standards of safety and sustainability.
STM’s flexibility makes it possible to manage a wide range of different plant configurations, both for sizes and for typology, including mobile plants. This configuration is one of the latest trends in a sector in which the plant owner wants to have freedom to move the plant after a limited time usage in determined area.
CONCRETE PLACING (RCC CONVEYORS)
STM developed a specific system for concrete placement, both for conventional concrete and for RCC concrete. Roller-compacted concrete, or RCC, is placed with conventional or high-density asphalt paving equipment, then compacted with rollers. RCC has the same basic ingredients as conventional concrete: cement, water, and aggregates, such as gravel or crushed stone. However, unlike conventional concrete, it’s a drier mix — stiff enough to be compacted by vibratory rollers. Typically, RCC is constructed without joints. It needs neither forms nor finishing, nor does it contain dowels or steel reinforcing. RCC concrete is mainly employed for gravity dams. To reduce the entire duration of the construction site, to meet operative, financial, environmental benefit and to deliver as soon as possible such important infrastructure to the local community, contractors are increasingly looking for equipment able to guarantee them continuous feeding with flexible use mode .This application in fact provide a conveyor line able to follow the dam growing, with special devices as elevation tools for conveyors and distribution devices as swingers, crawler placers, tripper conveyors.
In this field STM was awarded for the supply of the belt conveyors package at Ulu Jelai DAM — Malaysia: the line is designed to follow the dam grow up, with special elevation devices, in a strongly efficient and effective distribution system. The project is located approximately 200km north of Kuala Lumpur in the state of Pahang. The main component is the construction of the dam on the Bertram River, more than 80 metres high and constructed entirely using the advanced technology of RCC (roller compacted concrete).
TECHNOLOGICAL DEVELOPMENTS
In order to carry out in the most efficient way the concrete distribution on the dam floor, for the Ulu Jelai Dam Project STM has developed a special device to load trucks at continuous rate: the so-called ‘swinger’ makes it possible to supply RCC up to the end of the conveyor line with the flexibility of a 360° rotation, without downtime for the material flow. The swinger has a specific elevation tool that allows it to follow the dam growing as well as the modification of the conveyors configuration along the slope.
BATCHING PLANTS
Often belt conveyors are employed in the handling of inert materials such as gravel, sand and mixed granules for the preparation of concrete. The belt conveyors allow for the extraction and the automatic weighing of granules needed for the preparation of concrete mix. The installation plan usually includes a silo for storage and segregation of inert materials as well as a system belt conveyors system for dosing and feeding the inert materials to the concrete mixing plant. Based on customer needs, STM designs and develops the specific handling system for automatic flows management in the concrete mixing plant.
THERMOELECTRIC
A thermal power generation plant is the most conventional source of electric power. Conventional plants produce electricity by burning fossil fuels, such as coal, in order to have pressurized high temperature steam and to use it to rotate a turbine, with consequent electricity production. Biomass is biological material widely used as an alternative energy source in thermal power generation. The main advantage of using is that the CO2 produced during the process is the same gas that the material has absorbed from the atmosphere in previous years. This avoids any release of new CO2 into the atmosphere, with consequent benefits for the environment. To handle those kinds of materials in a complex power plant, it is necessary to design a system with exceptional reliability in order to avoid any kind of shutdown for tens of years. STM provides a complete engineering including specific back-up solutions, limited maintenance devices, best-in- class components manufacturers
WASTE TO ENERGY
Belt conveyors are usually inserted into complex and articulated systems in which every single element is fundamental for the overall functioning of the whole industrial plant — or stockyard. In a plant for electricity production from waste, STM usually carries out the complete engineering for flows exchanges, paths for personnel, access points, maintenance areas, load bearing structures, pylon towers, and conveyor switching. Even if the material is not so difficult to process or to transport, the low density makes it necessary to change the design approach to handle a high material volume but at the same time to guarantee high values of tonnes per annum to feed adequately the processing machines.
OTHER APPLICATIONS
Other areas in which STM has increased its expertise in conveying systems include heavy clay, refining, tunneling and bitumen plants.
MATERIALS
Working in such a range of fields, the variety of materials transported is even broader: coal, petroleum coke, RCC, gravel, sand, pellet, hot ash, clinker, municipal solid waste — each with particular behaviours along the process, and a need to find a solution to handle it in the most effective way.
COMPANY
STM is an Italian company, with headquarters and plant in Tito Scalo, Italy.
Claudius Peters wins reclaimer contract
Since its founding in 1906, Claudius Peters has become one of the world’s most respected engineering houses and an innovativeworldleader. ItsGermanengineeringexcellence continues to set benchmarks for the design, manufacture and commissioning of materials handling and processing systems for the gypsum, cement, coal, alumina and bulk-handling industries.
From conception and installation through to commissioning and after-sales support, Claudius Peters provides world-class service to the world’s biggest bulk materials producers.
The company is part of the Claudius Peters Group GmbH, headquartered in Buxtehude near Hamburg, Germany, with regionalofficesintheAmericas,AsiaandEurope.
In May 2012, Claudius Peters Technologies SAS, CP office in France, specialized in bulk material handling and stockyard equipment, including stackers, reclaimers, belt conveyor systems, etc, was awarded a contract by DOOSAN Heavy Industries & Construction Co. Ltd for the engineering and the supply of two coal reclaimers to be installed in the Muong Duong II coal-fired power plant inVietnam.The first machine has already been commissioned, and the second is currently under erection, with commissioning expected in late 2014.
Machine characteristics:
- stock capacity: 2 x 152.000 tonnes, 347m length
- pile width: 48m v rail span: 56m
- output:1,200tph
- chains drives: 250/55kW (main/secondary)
- Particularities:ATEX — air pressured control cabin including inert gas firefighting system — dust suppression system for discharge chute, etc...
These two machines are representative of what Claudius Peters Technologies SAS is able to supply, whatever its customers require, regardless of the bulk product to be handled, or the machine size.