but very effective. The screw shaft is fixed via a cone to a heavy
shaft. The shaft barrel itself is supported at both ends with a
housing. The operating rotational speed of the construction is far
below the critical rotational speed. The design advantages are:
* the non-return valve is completely closed for zero load.
arrangements. This includes top feeding either pneumatic or
outlet with in-line or left or right hand discharge. Each pump
source.
different applications. These include the transport of cement and
and granulated blast furnace slag. More than 1,500 IBAU pumps
are successfully in operation, about 70% in the cement industry.
advantage.
hour). The mill load is mostly constant but can depend on a
number of operational parameters. IBAU pumps
cement over distances up to 500m into the storage silos. The
horizontal mills.
mechanical mixers. The finished product from either the
pumps back into the silo cells. Throughput depends on the
100tph to 350tph. Conveying length depends on the silo height
and is often between 40 to 60m.
Fly ash/GGBFS conveyingFly ash, GGBGS and other additives are needed as a component
in producing special cements. This can be done via separate or
combined grinding. IBAU pumps (Fig. 8, below) transport the
bulk material either from storage silos to the mills in combined
grinding or from the mills to the silos in separate grinding
processes. The pumps enable conveying of practically all
throughputs from 100tph to 350tph over distances of 50m to
500m.
Coal dust transportationCoal dust with bulk densities of about 0.5kg/m3 and
temperatures of up to 100°C from coal mills is separated in
filters, from which it has to be transported either to the storage
silos for the primary or secondary burners. Because of
pressure-proof design back pressures are limited to about 1.5
bar, which limits the conveying throughput and conveying length
to about 250m. IBAU pumps allow a maximum safety because
of a number of safety devices, including oil and conveying air
cooling with appropriate temperature measurement, pump filter,
pump feeding via rotary feeder and level indicator in pump
hopper and pack-pressure sensor in the conveying line.
Ship-unloading
Stationary or port-mobile mechanical and pneumatic
ship-unloaders need downstream equipment that
can cope with peak loads, and are able to transport the material
over distances up to 500 m to the harbour storage silos. Such
requirements are well fitted by screw pumps, which offer a
variable load. Fig. 10 on p49 shows two integrated IBAU pumps
in a high-performance ship-unloader for up to 800tph rated
capacity. The material from the pumps can be injected into one
pipeline. The ship-unloader is equipped with a clamping device
which is to connect the ship-unloader safely and quickly with the
pipeline at the different unloading positions along the bulk
carrier. At the end of the pipeline are two-way valves which
distribute the cement into the selected silos. Fig. 11 below
shows a road mobile pump system, as it is used e.g. for
downstream conveying at road-mobile ship-unloaders.
Self discharging bulk carriers
Advanced self-unloaders in the 1,000dwt to 60,000dwt range are
equipped with fluidization systems in the cargo holds. The
systems can be installed in new builds and conversions within six
months. Unique in the IBAU concept is the space-saving midship
tunnel design, that integrates the discharge equipment and
divides the holds into a portside and starboard compartment.
For transporting the cement from the midship tunnel to the
shore terminal, IBAU screw pumps with a special design are
used, which have a very low feed point and allow a lateral
feed from left and right hand side.
Each pump transports up to 350tph cement. Conveying
distances of more than 600m can be achieved.
CONCLUSIONIBAU screw pumps offer a high performance and maximum
efficiency in pneumatic conveying with outstanding pump design.
The design clearly demonstrates that a shaft barrel design offer a
number of advantages against the more complicate two end
shaft bearing without any compromise to smooth and vibrationfree
running. The many optional pump arrangements, which
include a full road-mobile system offer customers in the cement
industry easy planning, when high throughputs, long transport
distances and flexible load are required.
Cargo hold cleaning after cement carriage
The cleaning of cargo holds after
the carriage of cement in bulk
can be one of the more
interesting challenges that a
Handy operator will face in the
dry bulk trades, writes Capt. Clay
Petroff VP Operations of Tidal
Transport & Trading. To
successfully bring the cargo holds
back up to grain standard, or
better, after discharging bulk
cement requires diligent planning,
coordination and monitoring on
the part of the operator. Failure
to do so can impact not only the
schedule and results of the
current voyage but also have
consequential costs and delays on
later voyages.
PREPARATIONProper preparation for hold
cleaning operations includes a
comprehensive plan and timeline
that factors in location, equipment, personnel, and cost. In order
to better understand the scope of the operation, among the
questions the operator must prepare for are:
* will the cement be loaded by spout (gravity) or will it be
pneumatically blown in through a flanged opening on hatch
covers with hatches closed? This is important for if the cement
is loaded by spout with hatches open the residues above the
cargo line can often be minimal and those areas may require
little, if any, dry cleaning. Alternatively, when the cargo is blown
in it is not unusual to see cement powder caked 5–10mm on
every surface of the hold, including the underside of the hatch
covers as well as the fore and aft overhead frames and stiffeners.
This will significantly increase the scope of the cleaning
operation.
* what is the condition of the cargo holds prior to loading? Is
the vessel condition to grain standard to begin with? What is
the condition of the hold coatings? Good hold coatings can
greatly help in the cleaning process while rough, pitted, and scaly
surfaces will increase the difficulty of the cleaning.
* is the vessel double skinned or is it a standard bulker with
hopper sides and exposed frames? Are there excessive trimming
plates and pipe guards in the fore and aft areas of the hold? Are
the Australian Ladders enclosed or are they exposed? Increased
surface area directly correlates to the increase in time required
to clean.
* does the cleaning plan include use of shore assistance at the
discharge port? Are there experienced cleaning gangs available
at the port and at what price? What is the basis of the cost, is it
‘no cure, no pay’ or is it ‘time & materials’?
* what is the experience level of the ship’s crew with cement?
Can they be trained and equipped to handle the task? Due to
the physical nature of the work, motivation for this type of
operation can be an issue. As well, clauses concerning hold
cleaning by crew must be reviewed carefully to ensure
compliance with the terms of the charter party.
* does the discharge port have available the equipment
required for proper cleaning, especially if cleaning the upper
reach areas of the cargo hold is required? Can aerial lifts and
pressure washers be sourced at the discharge port? Can this
equipment be loaded onboard at the discharge terminal?
* does the discharge terminal allow cleaning to take place
alongside the berth? If not, a layby berth may have to be
arranged or the vessel may have to handle the task at anchor.
This can present additional logistics issues as barging of
equipment may need to be arranged.
How much cargo does the terminal typically leave in each
hold? The contract terms for stevedores varies greatly and it is
not unusual to see in excess of 100 metric tonnes left behind
after discharge.
The more information the operator can obtain prior to
loading the better the chances of a successful cleaning. Whilst
the ships’ agent(s) will be a good source of information on local
practices and availability of equipment and labour, proper
diligence lies with the operator to effect the best outcome.
CEMENTIt is important for any operator to understand the hazards
involved with exposure to the cargo they are carrying and
cement is no different. Contact with the skin is the most
common hazard when handling cement, especially when wet, as
it can cause burns and dermatitis. Also, exposure to high levels
of dust, especially during the dry cleaning operation, can irritate
the nose and throat. Proper personal protective equipment
(PPE) should be provided to any personnel being asked to
perform any hold cleaning activity. This should include, but not
be limited to:
- disposable protective suits;
- safety goggles;
- head sock;
- particle masks if general sweeping; and
- full face respirators with particle filters if using air for cleaning.
Additionally, if using chemicals or acid for cleaning, proper
PPE suitable for the cleaning agent must be used.
HOLD CLEANINGThere are many methods used for cement cleaning and newer
methods are frequently being tried in order to improve
efficiencies and costs. The choices in cleaning method are oft
times dictated by what is allowed or preferred locally at the
discharge port. A few of the more common methods of hold
cleaning are:
*
sweeping — generally sweeping with a soft bristled broom or
brush is most thorough and sure way to dry clean the cargo
holds. It allows for close inspection of the areas being cleaned
with the least amount of training required, especially if using
ship’s crew. It also has the least dust emissions and can be done
within most port limits with no environmental issues. If carried
out properly with the right equipment, this method can be quite
efficient. In many ports sweeping can be carried out in adjacent
holds during the discharge operation, which greatly reduces the
time required to complete cleaning at the end of discharge. The
downside of this method is that it is the most physical in nature,
sometimes exacting a toll on the available labour or crew.
*
compressed air — blowing with compressed air is a
common cleaning method which is sometimes used in
combination with sweeping. It can be slightly faster than
sweeping on vertical surfaces and is generally less physical in
nature. The problem vessels have had utilizing air, especially
recently, is the cloud of dust particles this method emits.
Emission standards inside many of the ports does not allow for
this type of method to be used as commonly as it once was.
Availability of sufficient air pressure can also be an issue as
compressors may need to be sourced if ship’s supplied air is
insufficient for extensive cleaning.
*
acid/chemical — acid and chemicals are used in
many parts of the world for removal of cement
residues. While this method can be effective it does
require specially trained personnel and is typically
contracted out. Aside from the hazardous nature of
the cleaning agent, there is also the problem of
disposal of the wash residues to be considered.
*
mechanical agitators — the use of mechanical
agitators utilizing air through small tubes and whips
has been introduced into the market. This method
is advertised to negate the requirement for aerial
lifts or other equipment used for working aloft.
This equipment can be efficient on flat vertical
surfaces but getting behind tight areas and under
the overhead areas can pose problems. As with
utilizing air, the emissions outputs must be
considered if using this equipment inside port limits.
*
curtains — some owners have taken the step of
installing curtains prior to loading that hang from
the coaming to the tank top in order to shield the
vertical surfaces. This method requires additional
time prior to loading in addition to the advanced
preparation of the materials required to be used
and the arrangement/cost to install. Though not a
common practice this method can greatly reduce
the amount of time required for cleaning after
discharge.
Whatever plan decided upon for the hold
cleaning operation, it should be communicated with
all of the stakeholders well in advance of the vessel
arrival at the discharge port.
HOLD WASHINGBefore water is introduced into the cargo hold a thorough
inspection of the surface areas should be carried out by senior
officers to ensure no visible cement residues remain. The
thoroughness of the dry cleaning operation will directly impact
the amount of equipment and time required for hold washing. If
dry cleaning is done properly with good general hold conditions
then quite often the holds can be washed to grain standard
utilizing only a combi-gun or similar nozzle arrangement. If hold
conditions are poor or if stubborn residues remain after dry
cleaning which cannot be efficiently removed then high pressure
washing may be required.
After washing and pumping is complete, bilges cleaned, and
hold surfaces dried, all areas of the hold should be re-inspected
for dried cement residue as well as loose scale and paint. It is
not uncommon for some residues of cement to remain in the
holds even after the most efficient cleaning. However a close
inspection by an attentive ship staff can address any areas
requiring light scraping and touch up.
Hold cleaning after carriage of cement is not technically difficult,
but it is laborious and can be time consuming and expensive.
Mistakes with cement are not often forgiving. However, with
approximately 70 million tonnes of cement transported by sea
annually(1), chances are that many dry operators will be faced
with this task at some point in their career and with proper
planning and monitoring the challenge of cement cleaning can be
met with success.
Singapore cement terminal awards refurbishment contract to Cargotec
To improve its performance, Sin Heng Chan Cement Terminal
has contracted Cargotec for a major new refurbishment
project on its Siwertell ship unloader
In January Cargotec won a substantial new refurbishment
contract from major cement importer Sin Heng Chan
Cement Terminal in Singapore, which will see the company’s
local bulk handling services branch upgrade Sin Heng Chan’s
Siwertell ST-490F ship unloader. In July 2009 Cargotec in
Singapore successfully supervised a service project. The
customer was pleased and shortly thereafter, a new meeting
was held to discuss the refurbishment of the Siwertell
ST-490F ship unloader.
“The contract came about through excellent teamwork
from Cargotec’s bulk handling services in Bjuv, Sweden,
coupled with good co-operation from the local branch office
in Singapore, as well as a long-standing relationship with Sin
Heng Chan Cement Terminal,” says Daniel Frostberg,
Cargotec’s bulk handling services sales manager.
The refurbishment project will involve the upgrade of part
of the Sin Heng Chan Cement Terminal and its Siwertell ship
unloader to a new and improved design. The unloader will
also be updated with the latest versions of both hardware and
software to simplify operations.
This will provide an improved alarm monitoring system
and secure spare parts supply. It will also reduce wear and
tear costs and improve the performance and reliability of the
upgraded element of the terminal and the Siwertell ship
unloader.
Euromec ‘grabs’ the attention of the cement market
Euromec Srl considers itself to be at the forefront of the
production of electrohydraulic equipment to handle all types
of bulk material. With 60 years of experience, it has
specialized in the handling of all different kinds of bulk
material, including cement. It has received the most rigorous
certifications worldwide, including ATEX, NEC500 and NEMA
for dangerous environments and GOST certifications.
Thanks to this high degree of specialization, and to the
company’s ability to satisfy all the needs of its customers,
Euromec delivers to companies that are known throughout
the world. Cement-related customers include companies
such as Italcementi, Buzzi Unicem, Lafarge and Cementir, as
well as many others.
Furthermore, all of Euromec’s equipment, built using the
expertise that the company has gained over its 60 years of
operation, are made with the highest-quality materials and
components. Its products currently on the market are made
of sheet metal and are fully automated, which means that they
can operate 24 hours a day. They are also suitable for use in
extremely hot environments, such as those in the manufacture
of clinker. Machine downtime is kept to a minimum, as is
maintenance downtime. Euromec’s careful attention to the
needs of its customers and its meticulous technical
knowledge, combined with its experience in the materials
handling process, make it a major force, guaranteeing that its
products can be found in all the largest ports and plants all
over the world. Reliability and after-sales service keep
Euromec at the forefront of the market.
During the planning stages, Euromec pays particular
attention to ensuring that its production processes are as
simple as possible, so that it can keep production costs low,
can improve the final quality of its products, and reduce
maintenance to a minimum, so that it can offer its end-users
an economical, reliable, long-lasting product with low
maintenance costs.
The company has a great many references for its products,
and its 60 years’ experience mean that it has the backbone to
satisfy all of its clients needs. Its warehouses and offices are
always open and it welcomes visits from potential clients. It
believes that its exemplary references are its best ‘business
card’.
Primasonics acoustic cleaners become popular in Nigerian cement plants
In 2007 Obajana Cement constructed a new cement plant in
Kogi state, Nigeria. Obajana Cement is part of the impressive
privately owned Dangote Group and the Obajana Cement Plant
is now the largest in Sub-Saharan Africa. The project was
managed by ACC, India and FL Smidth were lead equipment
suppliers. This new site contained eight large cement storage
silos (61m in height and 18m in diameter).
Shortly after commissioning, Obajana Cement contacted
Primasonics International to ask its advice in solving side wall
material build up and blocking within these large silos. First of
all the silos had to be cleaned in an efficient and safe manner
before Primasonics acoustic cleaners could be installed. The
initial decision the company had to make was whether to
employ an international silo cleaning company or purchase its
own safe, rapid silo cleaning equipment. With a total of eight
massive silos to clean out, it became obvious that by far the
most economical solution was to purchase its own silo cleaning
equipment and it chose the Primasonics Prima Whip. At the
same time Primasonics technical staff had concluded that each
massive silo required the installation of twin acoustic cleaners
model PAS-60, the most powerful audiosonic acoustic cleaner
available.
By late 2007, Obajana Cement had taken delivery of the
largest version of the Prima Whip plus a total of eight
Primasonics acoustic cleaners model PAS-60 for four of its
storage silos.
The results were so successful that the following year, the
Obajana Cement placed another order with Primasonics
International for the supply of a further eight model PAS-60
acoustic cleaners for its remaining four storage silos.
It seems good news travels fast. Primasonics was then
contacted by Lafarge Cement WAPCO Nigeria Ltd, Sagamu
Plant, which was interested in the Primasonics Prima Whip for
cleaning its numerous cement silos. After discussions with
Primasonics technical team, Lafarge Cement made the decision
to purchase the Primasonics Prima Whip. After 12 months of
using Primasonics equipment here is what the Sagamu Plant
maintenance manager has to say: “We have used the Primasonics
Prima Whip for several months now on a cement silo cleaning
programme where we consider safety our first priority. We
purchased the Primasonics Prima Whip system so we can
remove the build-up in the silos from above in a safe and
efficient manner, thus eliminating the danger of manually going
inside to work. We are now successfully completing Prima Whip
cleaning of our second silo of the four we have in use and in
total we have been able to remove approximately 1,500 tonnes
of caked up cement.
“The process we use is to open up from the centre and work
around to release the cement from the side walls and down to
the outlet. We then work on all the build-ups on the walls of
the silo to make sure when we enter from the side hatches at
the base of the silo so as to remove all the free cement lying in
the bottom no material is left on the walls which could fall and
engulf or injure our workers. This can now be safely and quickly
done without the risk of injury to our workers. When this is
complete we can then overhaul the extraction systems and air
slides and put the silo back into full operation.
“The Prima Whip system has worked very well and has been
a big success for us in this project. Thank you Primasonics for all
your help and for supplying us with our Prima Whip.”
Primasonics is now in discussions with personnel at the
Sagamu Plant about installing the Primasonics PAS 60 model
acoustic cleaner on its clean silos to prevent the build up from
re-occurring.
Van Aalst solves Panama conundrum
Van Aalst Bulk Handling is a specialist in the manufacture of
equipment to handle cement, specifically shiploaders and
unloaders which can handle cement and fly ash.
At the end of last year, Van Aalst Bulk Handling started up a
ship unloader in Panama, which is built on a floating terminal
For a large hydropower project, a dam has to be built in
Changuinola river basin. Changuinola Civil works has made a
floating terminal. However, there is not enough space on shore
to erect silos.
Van Aalst Bulk Handling has therefore delivered a ship
unloader for this terminal. This ship unloader can unload supply
ships with cement, and pumps this cement or fly ash into the
holds of the terminal or to small silos on shore.
When no supply ship is available, the ship unloader can
unload its own holds to supply the small silos on shore.
Van Aalst Bulk Handling has also entered the recycling market.
Asphalt recycling creates ceramic powder which can
be used in combination with cement and concrete. The big
problem is that the product is extremely abrasive.
Van Aalst has manufactured a conveying unit and
silo for cement, which can cope with the characteristics of
this product.
Delivery took place in January this year.
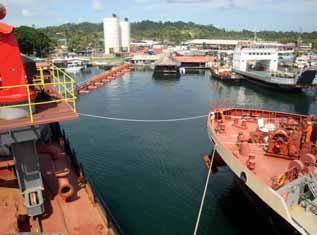
CTP commissions equipment for Greek cement plant
Earlier this month (May), the CTP Team, part of the Bedeschi Group, commissioned a new
bag filter for kiln/raw mill exhaust gas dedusting at Aspropyrgos plant (Greece)
belonging to Halyps – Italcementi Group.
The project involved the modification of the existing conditioning tower and the
supply of a new lime injection system for SOx reduction.
The filter implements an innovative gas distribution specifically designed to enhance
the lime reaction for sulphur emission control and it is fitted with 7.5m bag length
performing low-pressure cleaning technology and best efficiency in gas filtration and
cleaning.
As part of the contract, CTP also supplied a new compressed air station, lime dosing
silos, complete ducting and filter fan. The work included the dismantling of existing
equipment and erection of the new equipment.
Electrical feeding equipment, together with a dedicated full automation system of
the new dedusting plant, completes the turnkey project.