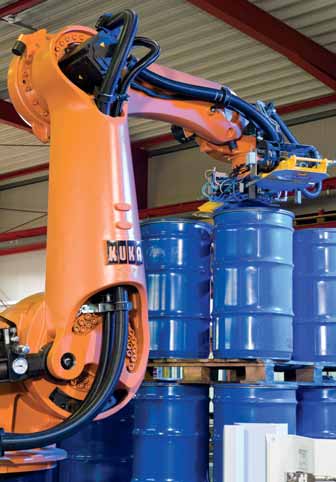
SMB Group from Germany creates comprehensive systems for material handling
Industrial process chains in the construction sector are in a state of constant development. The SMB Group offer systems and conveyor technologies that can be tailored to meet business needs, from delivery to reloading.
For intra-logistical processes to work seamlessly together in handling a variety of goods, high priority is placed on the interaction between software and hardware. It is exactly these automated systems that facilitate the processes and contribute to savings in time and costs. The support provided by the new technologies is of essential
importance, especially for companies with an extensive intra-logistics chain. An example of such a comprehensive system in the field of material handling is SMB Group’s unloading robot.
UNLOADING ROBOTS ARE DESIGNED FOR THE AUTOMATIC FILLING SYSTEMS.
The automation process starts with the delivery, and it makes no difference whether goods are dumped as bulk cargo into bins or into the containers. SMB has designed the truck unloading robots for internationally operating companies. The robot places the containers quickly and accurately onto the roller belt, which is installed directly on the loading ramp. In designing this system, it is especially important to make sure that the weight and movement of the machines are synchronized. Frequency converters are used to prevent rapid, jerky movements.The overall light weight of the system is achieved through optimized use of special finite- element-method software. During single drum unloading, a palletizer is attached to the unloading robot, which places the drums automatically onto the pallets.An empty pallet magazine is pushed fully automatically to the empty pallets.The pallets with empty drums are then fed into the filling system.The system detects the position of the drum opening.The drums are unscrewed automatically, then closed and sealed again after filling.
"However different the needs of our customers may be, the complete system for any application can be designed on customer request, using a variety of synchronized system modules," explains Andreas Heckel, Managing SMB Group.
SMB-GROUP
SMB International and MBA Instruments:Two brands - one idea. SMB and MBA have focused their business activities in the area of "material handling". Planning, development, manufacturing, highly complex global distribution, automatic loading systems, filling systems, level measurement technology, palletizers, conveyor systems, compact high-bay warehouse ship loaders are part of our product range.
SMB Group has quite deliberately opted for a high proportion of in-house production at its plant in Quickborn, near Hamburg. In this way, customer requirements can be implemented spontaneously, targeted and quickly while maintaining high product quality.
In-house design and production of mechanical and electrical components are the basis for the decision to implement high production depth, which guarantees reliability in terms of quality and delivery time. Installation and service teams work on national and international projects.The global sales network ensures quick and targeted information and coordination.
Kirow Ardelt GmbH – high performance for handling bulk materials
Kirow Ardelt GmbH has been building cranes for more than 110 years and by using the experience gained from supplying several thousand harbour cranes over this time, has advanced to become one of the leading manufacturers of lifting equipment for handling bulk materials.
In particular, the development of the double jib level luffing system, together with the integration of hoppers and unloading equipment into the crane system, are key factors behind the advance to achieve higher handling performances and exemplary efficiency of the equipment.
Only a few months ago, two of the largest ARDELT cranes were introduced for handling operations in Wilhelmshaven in Germany. The primary task for both cranes is the unloading of coal carriers for supplying a nearby power station.
In order to unload vessels as large as Capesize efficiently, the crane has been designed with an outreach of 55m and lifting capacity of 63 tonnes.
These cranes are able to achieve a free digging performance of up to 2,400tph (tonnes per hour).
German engineering skills combined with the cutting edge technology of established sub-suppliers guarantees the outstanding efficiency of a slewing harbour crane.
The proven double jib level luffing system with its short rope lengths, provides precise and fast positioning of the grab. The grab used at port of Wilhelmshaven is a four-rope grab manufactured by Verstegen and has a capacity of 44m3 with a deadweight of approximately 19 tonnes. These dimensions are necessary in order to provide the handling volumes required.
The grab fills a hopper, which then supplies the bulk material via conveyor belt to the longitudinal quayside conveyor.
Like ship unloaders, the ARDELT TUKAN K cranes utilize the shortest working path between the hatch and the integrated hopper.
However, the energy consumption, maintenance and repair costs and noise emissions of these slewing cranes are lower than conventional ship-unloaders or mobile harbour cranes. The minimal energy consumption is a consequence of the solely electrical operation and ensures a high level of efficiency, in addition to the balanced jib system which renders inertia practically insignificant. Energy from braking movements and lowering of the load is fed back into the mains via an active line.
SENNEBOGEN presents the 8130 EQ:
75% more energy efficient thanks to its balance technology and electric motor
In an exclusive preview demonstration, SENNEBOGEN presented its new 8130 EQ balance material handler to DCi.
The 8130 EQ combines two important SENNEBOGEN trademarks: flexibility and low operating costs.
“With the 8130 we are entering a new dimension in terms of energy efficiency,” explains managing director, Erich Sennebogen.
“As the machine is fully balanced in every position a much smaller energy input is required.”
And it gets even better: “First tests have shown, that in combination with our electro-hydraulic drive, we can save about 75% in operating and energy costs, savings of 75%!”
In contrast to conventional hydraulic material handling machines, this latest machine from SENNEBOGEN not only sets new standards with regards to performance and handling but also enables savings of up to 75% in energy and running costs compared with conventional diesel motor drive concepts.
The SENNEBOGEN 8130 EQ with electric motor operates environmentally friendly and efficient, both in scrap handling and port material handling. An adjustable counterweight means that the machine always remains perfectly balanced in any position and the centre of gravity stays central. This EQ (equilibrium) principle enables the machine to constantly remain balanced. Thanks to the directly linked counterweight, minimal energy usage provides sufficient drive even for large reaches and high loads.
SOPHISTICATED BALANCE TECHNOLOGY AND ELECTRIC MOTOR: 75% SAVINGS The way it works is simple. The whole machine can be controlled using just two cylinders. A bar running parallel to the boom connects the jib to the rear counterweight and ensures effective transmission of power. During every operating movement, the counterweight is held in balance in a similar way
to classic lever principle behaviour. In this way, it takes almost no energy at all to move the machine. Even for heavy loads and high reaches, only the loads attached must be moved and driven — an enormous saving in terms of effort and energy. Savings in running costs and energy costs of up to 50% can be achieved just by using this sophisticated balance concept.
Used in combination with the electrohydraulic drive concept, further considerable savings are possible. As an electric machine, the 8130 EQ uses just 25% of the energy required by similar diesel-powered machinery.
There are even more advantages to the electric motor, including low energy consumption, low additional costs and above all, the motor operates extremely quietly and smoothly without refuelling. The 8130 EQ’s 400 volt electric motor generates a powerful 130 kW, while short hydraulic connection and reliable control technology allow the power to get to where it is needed.
AT HOME IN PORT MATERIAL HANDLING AND ON THE SCRAPYARD The new SENNEBOGEN 8130 EQ is particularly well suited for use in port material handling and on the scrapyard as well as for logging. The balance technology shows off its strengths in all situations where bulk goods or large quantities of scrap need to be handled cost-effectively. With a bearing load of 5 tonnes and a reach of 27m, a stationary machine can easily operate in an area of around 2,300m2. Additional material can be piled up to a height of 25m. Several working steps can still be carried out with optimum logistics from a central position. A clear view is always guaranteed thanks to the pylon structure and the raised cab position.
In addition, the machinery guarantees the highest level of efficiency and productive workflows in port material handling. From ships to Handysize-class vessels, the SENNEBOGEN 8130 can unload goods up to a depth of 8m and can bear a load of up to 10t.
CENTRAL AND EASILY ACCESSIBLE — THE SENNEBOGEN POWER PACK
Optimal ease of use and convenient maintenance safeguard the sophisticated machine design. Centrally accessible monitoring and maintenance points guarantee quick and easy inspection of the entire hydraulic system. The Power Pack that can be accessed inside offers the best possible access to the engine and the control technology in any weather conditions — that’s easy maintenance at its best. All drive and control components are kept together in a large engine compartment. The clearly arranged design, simple maintenance and understandable technology prove their worth in daily use. With 60 years of experience, SENNEBOGEN guarantees excellent reliability and the best in safety and durability. A rapid supply of spare parts and premium maintenance are ensured thanks to the use of proven standard components and the easy-to-reach positioning of both cylinders.
PROVEN TECHNOLOGY AND NEW PRODUCT DEVELOPMENTS – MASTERCAB IS THE IDEAL CABIN SENNEBOGEN represents individual, customer-specific solutions and thanks to the modular design of its machines, a wide range of equipment options is always possible. From stationary underframes, crawler chassis or rail solutions to pontoon constructions, a wide range of solutions are possible, all tailored to the customer’s requirements. The machine is also available as an option with a 151/164kW Cummins diesel engine. In the cabin on the 8130, the driver not only has a clear view, but thanks to the SENNEBOGEN SENCON Control System, all the adjustments can be made centrally, current measurement readings can be taken and the driver is able to fine tune things himself using the clear display. The proven SENNEBOGEN maXcab industrial comfort cabin allows the driver to get the best all-round view — an important safety factor — thanks to end-to-end tilted bullet proof glass and floor windows. In addition to the existing comfort cabin, the SENNEBOGEN
8130 will also be available with an all-new cabin design for the very first time. The new SENNEBOGEN Mastercab offers an outstanding feeling of spaciousness, the clearest view and the highest level of comfort. The resiliently mounted spacious harbour cab is impressive due to its large floor window and excellent all-round view — a valuable advantage for safety, for example when unloading ships.
The interior, complete with air-suspended seat, complies with the most recent ergonomic standards and certainly impresses with its staggering interior dimensions. In addition to sliding
windows and air conditioning, the Mastercab is the largest cabin in this machine class and is the first to be fitted with a spare foldaway seat. This means there is space for an instructor to sit for training purposes, where he can take an active role in instructing the driver. In comparison to the previous maXcab industrial cab, the optional cab is around 50% wider and 25% higher. For the driver this means the space has been almost doubled to over 6m3. Various storage solutions complete the top of its class interior in the new Mastercab and make it the perfect cab for demanding material handling. In the future, the Mastercab will be available as an option on SENNEBOGEN machines from the 850 model upwards.
SENNEBOGEN: service company, family enterprise
SENNEBOGEN, a German family-run enterprise, develops and produces complete model ranges for duty cycle crawler cranes, crawler-, telescopic- and harbour cranes, material handling machines, multiloaders as well as base carriers. In addition to flexible machines from series production, SENNEBOGEN also designs individual specialized machines in close collaboration with its clients.
SENNEBOGEN stands for material handling and lifting technology, global leadership through innovation and continuity as a German manufacturer.
The company’s customers and partners highly appreciate it as a responsible service company because it focuses on providing simple and better solutions. Its flexibility and ability to respond fast and direct communication with its partners only furthers this appreciation.
VALUES OF A FAMILY-RUN ENTERPRISE
1 Safe investment — longevity and high residual values through robust designs
2 Tailor-made — modular designs, customer specific build
3 Availability — engineered focus: controllable design — no over-engineering
4 Reliable — focus function and performance at any time
5 Innovative — leading through innovation through better solutions
6 Sustainable — clever investment; reduce lifetime cost.
7 Lasting values — quality ‘made in Germany’ — also for second hand markets
8 Future-oriented — electrohydraulic drive concepts — emission free, low noise, enduring.
VALUES OF A FAMILY-RUN ENTERPRISE
- economic strength for long-term stability;
- profitable, long-term oriented organic growth; and
- long-lasting and reliable partnerships worldwide.
THE ORGANIZATION — INDUSTRY ORIENTED
SENNEBOGEN has a wide variety of application- and competence focused product lines. Its product and industry specialists guarantee excellent support to its customers.
COMPETENCE GREEN LINE
SENNEBOGEN’s Green Line includes machines from 12 tonnes to 300 tonnes operating weight and machine availability of up to 7,000 operating hours per year.
SENNEBOGEN listens to its customers’ individual requirements and finds appropriate matching solutions. Furthermore, its products are highly reliability due to robust
design and quality components. Examples of where the Green Line of handling machines are
being used are: scrap handling, waste/recycling/biomass, timber and forest industry, ports, demolition, agriculture and municipalities.
COMPETENCE CRANE LINE
SENNEBOGEN’s full crane product line includes: telescopic cranes, crawler/rubber tyred, truck cranes, crawler cranes, HD rope excavators, foundation machines, multicranes.
Advantages of Crane Line products: Unique: simple maintenance, high availability, compact dimensions. Economic: low operating costs, high residual values, excellent transportability. Crawler cranes: Easy transport — ready for operation fast — working safe and with sensitivity. Telescopic cranes: Easy transport — ready for operation fast — working safe and with sensitivity. HD crawler cranes: duty cycle works in special foundation.
COMPETENCE PORT LINE
SENNEBOGEN’s Port Line includes a wide variety of purpose built cranes and material handling machines for the port industry with high productivity. Due to its modular system the Port Line offers the perfect solution for virtually every ship, vessel or barge size as well as every kind of cargo and every size of port.
These machines also have a high life-time expectancy due to very robust design and use of high quality components.
The Port Line’s machines are used in the following places: civil engineering, foundation construction, lifting industry, mining, and the demolition industry.
SALES AND SERVICE PARTNERS
SENNEBOGEN’s worldwide sales and service network, with experienced and factory trained partners, guarantees excellent service and local availability of parts.
There are 100% family owned subsidiaries present in important regions like North America, Middle East, Singapore and Russia.
FOUR INDIVIDUALLY ORIENTATED LOCATIONS
Plant Straubing 1, corporate headquarters
≈completed in 1959; v total area 44,000m2; v office & production space 16,000m2; v approx. 200 employees; and v corporate headquarter of the group as well as assembly of
OEM base carriers and fabrication of steel components.
Service centre Straubing
- expansion in 2008;
- completed in 1991;
- total area 160,000m2;
- office & production space 25,000m2;
- approx. 200 employees; and
- assembly of the Green Line material handling machines with
- approx. 50 employees; and
- product support and spare parts centre.
Plant Wackersdorf
up to 80t operating weight.
Plant Balatonfured/Hungary
- integrated in the group in 1996 total area 120,000m production space 22,000m2 approx. 300 employees
- fabrication of steel components as well as machining of steel structures
Plant Straubing 2, Industrial Park ‘Hafen’
- completed in 2008;
- total area 125,000m2;
- office & production space 20,000m2;
- approx. 350 employees; and
- research & development, assembly, marketing & sales of cranes, material handling machines and harbour mobile cranes focused on large machines, serial production and customized solutions.
SERVICE-CENTRE/SENNEBOGEN LLC
Straubing Service Center
- expansion 2008, 50 employees; and
- customer service/spare parts centre.
SENNEBOGEN LLC, Charlotte, USA
- completion 2010;
- total area 130,000m2;
- sales, spare parts, training centre; and
- managing 48 sales partners with more than 240 service points
PRODUCTION
- three locations in Bavaria, manufacturing of large machines — innovation leader for decades;
- flexible production methods and fast response times — transfer of customer ideas into solutions;
- use of local and high quality suppliers — logistic advantages and economic solutions; and
- ‘made in Germany’ stands for highest quality standards
RESPONSIBILITY
SENNEBOGEN is following a long-term strategy to become a strong player in the market. It is committed to keeping its designs simple and maintenance friendly, to train operators and service people. SENNEBOGEN’s focus remains on efficiency, safe operation and high machine availability.
The company is also dedicated to training the next generation — 10 % of its employees are working in its apprenticeship programme, the company’s investment into the future of the company.
PEOPLE
SENNEBOGEN believes that trained, experienced and motivated employees are the guarantee to its success in the market.
Low management structures and direct decision involvements of employees help the company to act quickly on customer solutions and to react fast to market changes.
Therefore it believes in high investments into employee training and apprenticeship programs, as well as close co- operations with high schools, universities and institutions.
EMOTIONS
A successful long-term operation is based on active participation to develop the company as well as interests in politics, industries and associations. Consequently SENNEBOGEN believes that a friendly and ecological company environment breeds satisfied customers, partners and employees, which instills in everybody the excitement and passion for their daily tasks.
Kirow Ardelt GmbH – high performance for handling bulk materials
Kirow Ardelt GmbH has been building cranes for more than 110 years and by using the experience gained from supplying several thousand harbour cranes over this time, has advanced to become one of the leading manufacturers of lifting equipment for handling bulk materials.
In particular, the development of the double jib level luffing system, together with the integration of hoppers and unloading equipment into the crane system, are key factors behind the advance to achieve higher handling performances and exemplary efficiency of the equipment.
Only a few months ago, two of the largest ARDELT cranes were introduced for handling operations in Wilhelmshaven in Germany. The primary task for both cranes is the unloading of coal carriers for supplying a nearby power station.
In order to unload vessels as large as Capesize efficiently, the crane has been designed with an outreach of 55m and lifting capacity of 63 tonnes.
These cranes are able to achieve a free digging performance of up to 2,400tph (tonnes per hour).
German engineering skills combined with the cutting edge technology of established sub-suppliers guarantees the outstanding efficiency of a slewing harbour crane.
The proven double jib level luffing system with its short rope lengths, provides precise and fast positioning of the grab. The grab used at port of Wilhelmshaven is a four-rope grab manufactured by Verstegen and has a capacity of 44m3 with a deadweight of approximately 19 tonnes. These dimensions are necessary in order to provide the handling volumes required.
The grab fills a hopper, which then supplies the bulk material via conveyor belt to the longitudinal quayside conveyor.
Like ship unloaders, the ARDELT TUKAN K cranes utilize the
shortest working path between the hatch and the integrated hopper.
However, the energy consumption, maintenance and repair costs and noise emissions of these slewing cranes are lower than conventional ship-unloaders or mobile harbour cranes. The minimal energy consumption is a consequence of the solely electrical operation and ensures a high level of efficiency, in addition to the balanced jib system which renders inertia practically insignificant. Energy from braking movements and lowering of the load is fed back into the mains via an active line.
In order to relieve the crane operator, it is possible to operate the handling process in semi-automatic mode.
The grab depth optimization system patented for ARDELT ensures smooth operation and minimizes interruptions that result from shutdown due to over-filling of the grab, or loss of performance from insufficient grab filling. Consequently the cranes fit seamlessly into the series of TUKAN K cranes supplied to various customers over recent years:
- two TUKAN K 1500 cranes for the bulk terminal in the port of Aarhus in Denmark. With a 45t lifting capacity and 45m outreach, each crane is designed for a performance of 1,100tph of coal or feedstuffs. Since bulk materials with very different characteristics are involved, the hopper is fitted with a specialized heated washing system.
- two TUKAN K 1500 cranes for unloading gabbro, with an hourly capacity of 1,100 tonnes. Material is removed via conveyor belts and chutes which service two truck lanes. The lifting capacity of the cranes is 50t and their outreach is 40m. These cranes are located at the port of Mesaieed in the emirate of Qatar.
- one TUKAN K 3000 crane, which unloads 1,400t of coal per hour in the port of Brunsbuttel, Germany. Lifting capacity and outreach are 68t and 50m respectively.
- the steelmill of CS Huachipato in Talcahuano, Chile is serviced by a TUKAN K 1500 40t x 40m which handles coal and ores.
- in Basle-Kleinhuningen and the Auhafen port on the Rhine river in Switzerland, two TUKAN K 750cranes are installed for handling various bulk materials. Both cranes have a lifting capacity of 12.5t with an outreach of 27m and are ideal for unloading inland waterway vessels.
On special request ARDELT can also create cranes with two integrated hoppers in one system. The dual hopper design is required in order to unload materials with differing densities and characteristics, optimizing the performance of the TUKAN K crane.
During 2013 ARDELT will supply another TUKAN 1500 K crane with two integrated hoppers for a port in the Baltic, this delivery will mark another highlight for our company.
In a differing design from that of the crane in Auhafen Port in Basle, which has the hoppers arranged on top of one another, these hoppers are integrated into the crane portal side by side.
With the handing over of this crane and the installation of another two cranes for handling sulphur in Tunisia during 2014, Kirow Ardelt GmbH will continue its series of successes for the delivery of high-performance double jib level luffing cranes tailored to the handling of all types of bulk materials.
Liebherr mobile harbour crane proves its versatility in the inland port of Bendorf, Germany
A LHM 280 is enhancing the material handling capacity of the German Rhine port of Bendorf with its universal possibilities of application. The port is operated by material handling and forwarding agency BUS Bendorfer Umschlags- und Speditionsgesellschaft.
The roots of the inland port of Bendorf date back to the year 1899. Today, the port is a key logistics hub and its customers benefit from the direct access to waterways, railroad and highways. Buying the Liebherr mobile harbour crane was part of the €6.5 million investment to improve the port’s infrastructure before it was officially reopened in August 2012 by Roger Lewentz, German Minister of the Interior.
Despite ongoing construction work no less than 1.6 million tonnes of material were handled in the port of Bendorf in 2011. The most important types of material handled were stones and soil followed by mineral oil products, steel, fertilizer and road salt.
From the very beginning, the LHM 280 has occupied an important position in the logistics processes of the Rhine port. The mobile harbour crane excels in both mobility as well as versatility as it is able to handle all traditional goods of the port. With its lifting capacity of 84 tonnes the all- rounder is also perfect for handling heavy goods.
“The LHM 280 has even exceeded our expectations. Especially the favourable consumption is far below our calculations,” says Markus Stock, executive director of BUS Bendorf. The mobile harbour crane is operated by an eco- friendly electric drive. During operation the crane is powered by an external current source — thus, fuel consumption is significantly reduced.
According to the executive director the decision to buy a
Liebherr mobile harbour crane was influenced by two key factors: first, the LHM 280 offered the best cost-performance ratio and second, BUS Bendorf had already gained positive experience in the past with the efficiency of wheel loaders manufactured by Liebherr.
The acquisition of the LHM 280 has already had positive effects on the port’s growth in terms of material handling. Thanks to the new high-performance mobile harbour crane concrete segments for wind energy plants are now handled in Bendorf.
Flexibility and quick response to customers’ needs are central requirements for inland ports. Due to its broad portfolio of mobile harbour cranes with different boom lengths and lifting capacities ranging from 42 to 208 tonnes Liebherr is able to meet these expectations. Moreover, the LHM series convinces through its wide range of applications: apart from individual loads and bulk material the cranes can also handle containers. The LHM 280 thus offers the Rhine port of Bendorf further potential for development.
KRÖGER Grabs still focused on further growth after 50 successful years
Combining quality, robustness and reliability to fulfill the severe jobs in daily operation is the company’s key ambition. KRÖGER grabs are employed by customers all over the world, typically used in rough environments like harbour, sand and gravel, underwater mining, steel and scrap as well as incineration operations. The KRÖGER product portfolio offers a broad range of products: cable grabs, motor powered grabs, motor hydraulic grabs and hydraulic grabs. All are available in standard configurations down to customized applications for all kinds of conceivable goods. Operations sizes range from 0.2 to 40 cubic metres. The modular system of KRÖGER grabs allows the company to react instantly on design and delivery requirements.
A special KRÖGER quality feature, to benefit the environment and for improved efficiency, is the zero- maintenance bearing design. It can be offered for the entire grab portfolio. One of the main challenges for current and future cargo handling activities is to increase grab capacity and to optimize opening/closing times to achieve best productivity ratios and the fastest return on invest. KRÖGER’s design philosophy aims at highest productivity, product quality for a long-lasting working life and lowest maintenance requirements.
In 2013 KRÖGER will focus on further technology development and growth projects as started in 2012. The momentum of the 50th company anniversary and the result of the 2012 business year with a highly motivated team of specialists will result in further technology innovations and new market entries. One of the main topics is to further establish KRÖGER’s sales and service network in one of the largest growth markets in the world — China. After a successful market entry with several projects in the waste to energy segment and the positive response on German quality, KRÖGER will increase the effort to fulfill local market demands. Besides selling a broader product range, the company also wants to establish the KRÖGER brand as a service provider for all applications within grab technology.
Another highlight in 2013 will be the ‘Bauma’ fair in Munich from 15–21 April. KRÖGER will present latest technology developments and present its product specifications. While it expects the trend towards very flexible and mobile hydraulic machines within the cargo handling industry to continue, large, old and heavy perhaps retrofitted cranes are expected to disappear over time. A new heavy-duty rotator for high performance hydraulic machines will be one of the main technology innovations shown. Another major topic is the increasing demand for fully automated cargo handling technologies and the required specifications for cargo handling attachments. KRÖGER will also present solutions in this segment.
In 2012 KRÖGER Greifertechnik celebrated the company’s 50th anniversary — 50 years of successful designing, developing, producing and maintaining grabs made KRÖGER one of the leading companies in the premium grab sector.
The focus of KRÖGER is state-of-the-art grab-technology.
Clear growth course
RHENUS MIDGARD EXPECTS TO DOUBLE HANDLING VOLUMES AT THE NIEDERSACHSENBRÜCKE JETTY
The berthing of the first fully laden Capesize vessel at the Niedersachsenbrücke jetty in November last year is a clear expression of the growth course that Rhenus Midgard in Wilhelmshaven has adopted. Never before has a ship of this size been able to arrive at a German seaport fully laden. This will just be the first of many and these vessels will help to turn the upgraded terminal on the Jade Basin into a central hub for coal imports.
People use heating in the winter season. Christmas is a time for lights. The resources, which are required to operate power stations generating energy or power, will continue to include a fair share of coal in future too — and this fact should not be underestimated. Despite all the efforts to boost renewable energy sources, the fossil fuel will continue to make a significant contribution towards guaranteeing power supplies in the next few years and decades.
“In the light of the halt to domestic coal mining in Germany, future needs will largely be covered by imported coal,” Michael Appelhans, managing director of Rhenus Midgard, explains. The logistics services provider is a long-standing partner of the coal industry and provides its expertise and assets to manage supply chains.
INCREASING VOLUMES
The Niedersachsenbrücke jetty, a traditional coal handling terminal on the North Sea coast off Wilhelmshaven, forms part of the company’s capacity. The facility, which has been operated by Rhenus Midgard since the mid-1970s, has been expanded and modernized during the last three years. Once the final upgrading work has been completed, the facility will reach its full operating capacity during the second quarter of 2013, but it
already provides excellent conditions for handling this kind of black gold. “We transshipped about 1.6mt [million tonnes] of coal at the Niedersachsenbrücke jetty last year. We’re hoping to handle more than 3mt during 2013,” says Appelhans, forecasting that volumes could roughly double. “New consumers joined the list at the start of the NewYear and other potential customers for 2013 are already waiting in the wings.” The Rhenus Midgard managing director believes that annual volumes at the Wilhelmshaven site could rise to between 8mt and 10mt in the long term.
RECORD CARGO
Fully laden Capesize bulk carriers, which can now be accommodated at the Niedersachsenbrücke jetty, will help achieve these results. The dredging work to deepen the mooring basin, which was handled by the Niedersachsen Ports infrastructure company, already allows the facility to handle bulk carriers of this size. “Wilhelmshaven can offer a draught of as much as 18.50 metres and is therefore the only German seaport where these vessels can berth when fully laden,” says Matthias Schrell, managing director of Rhenus Midgard in Wilhelmshaven, emphasizing his point.
The fact that Capesize vessels no longer need to be lightened before berthing in Wilhelmshaven ensured that the German seaport was able to set a new record at the beginning of November
2012. The NAVIOS POLLUX arrived at the Niedersachsenbrücke jetty after a voyage from South America lasting 19 days and was laden with 171,477 tonnes of coal. This was the largest single amount of coal to ever arrive at a German seaport.
“The handling of the NAVIOS POLLUX, which is 292 metres long and 45 metres wide, was a significant moment for us and underlined the unique status of the Niedersachsenbrücke jetty in Germany.As no problems emerged when handling the first vessel of this size at the port, we’ve finally been able to exploit the potential arising from the existing nautical conditions,” says Matthias Schrell.“More Capesize vessels will visit the port in the near future and the cargos could come
from countries like America, South Africa or Australia.”
IMPROVING PERFORMANCE
The berthing of a Capesize vessel is one side of the coin – unloading the coal from vessels, which can carry up to a quarter of a million tonnes of coal, is the other. For this purpose, the Rhenus Group has invested in its handling equipment and storage capacity at the Niedersachsenbrücke jetty. In the past, one ship unloader was used on the pier – now two new double jib level luffing cranes with a lifting capacity of 63 tonnes have been added; operating together, they are able to unload up to 4,000 tonnes of coal per hour.
At the land-side section of the terminal, two new stacker/reclaimers operate and are able to place 4,000
tonnes of coal into storage per hour or load 2,000 tonnes of coal per hour on to coal wagons heading for destinations further inland.The logistics services company had earlier built a new, automatic train loader for this purpose.
The terminal will reach its full productivity when the last new conveyor belt goes into operation during the 2nd quarter of this year; the belt will connect the pier with the two storage areas which are each able to hold approx. 450,000 tonnes of coal. “We’ve paid attention to a high degree of loading precision in the technical design of the overall equipment, but we’ve also attached importance to the smooth transition between the individual stages of the handling operations,” says Matthias Schrell, describing the dove-tailing of the individual components.
“As the upgrading work on the railway line from Wilhelmshaven to Oldenburg was completed during the winter and it now has double tracks, our business also benefits from improved links to the European rail network,” says Matthias Schrell.“These rail connections enable the coal to be distributed in line with demand and ensure the high level of reliability needed in the supply chain for coal-fired power stations.