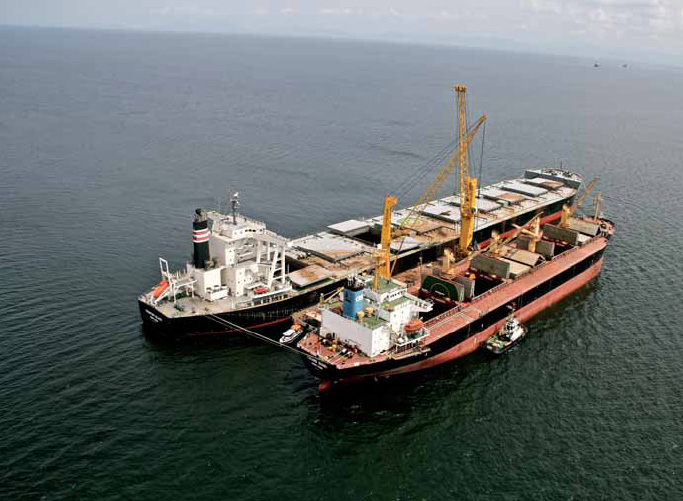
New bulk carrier design puts Ecoships in the lotus position
Ecoships, the technical ship management arm of Newport Shipping Group, has introduced a next-generation bulk carrier design, developed to set the standard in ecologically compatible marine transportation.
Inspired by the low friction to water flow and self-cleaning properties of the lotus flower — a symbol of purity and beauty in Buddhist and Hindu philosophy — Ecoships’ Greenlotus 32, is a 32,500dwt geared, wide hatched, Handysize bulker, designed to meet existing and future CO2 (carbon dioxide) NOx (oxides of nitrogen) and SOx (oxides of sulphur) emissions regulations.
Captain Aykut Yilmaz, Newport Shipping’s General Manager, said:“The Greenlotus 32 is a proven eco-friendly bulk carrier that builds on the success of two earlier designs delivered in 2011. From cost and energy efficiency perspectives, it makes a lot of sense for shipowners to reconsider their ageing Handies in favour of the Greenlotus 32. The return on investment is very attractive due to its extremely low fuel consumption and it meets the most stringent emissions reduction requirements.”
The 170.90m-long, 27m-wide hull form, optimized for energy-
efficient operation using computational fluid dynamics and finite element analysis, has a propulsion arrangement based around a de-rated,Tier III compliant MAN B&W SG50ME-B9 two-stroke main engine driving a large diameter, fixed pitch propeller.
“This configuration provides a heavy fuel oil consumption of just 15.6t/day at a service speed of 14 knots and 7.6 t/day at 11 knots. Compared to the daily fuel oil consumption of comparable Handy-size designs, the Greenlotus 32 can generate daily fuel savings of more than US$6500 on a bunker price of $650t, operating at 14 knots,” Yilmaz added.
The Greenlotus 32 is also equipped with built-in technology for voyage and weather routing, trim optimization and a system to provide real-time analysis of ship data, including bunker quality and emissions.
Additional emissions abatement can be achieved through the optional installation of an exhaust gas scrubbing system and/or a selective catalyst reduction unit.
Exhaust gas recirculation and waste heat recovery systems, available with the standard Greenlotus 32 design, add to the vessel’s arsenal of ecologically friendly measures. “It really does minimize the environmental impact of bulk shipping,” said Yilmaz. Suitable for the carriage of a variety of cargoes, including coal, grain, ore, direct reduced iron, cement, bauxite and steel coil, across five double skin cargo holds, the ‘Eco-Smart’ design features wide, steel-covered hatches in conjunction with the absence of hoppers and lower bulkhead stools to facilitate optimal loading and discharging operations.
Fuel tanks, coffered against cargo Hold 5 to reduce the risk of pollution and to protect heat sensitive cargoes, have been prepared for low sulphur fuel operation.
Fulfilling IMO requirements for permanent means of access for close up survey work and ease of maintenance, service piping and electrical cables run along two side pipe tunnels within the double hull. The arrangement serves as a safe conduit between the superstructure and foredeck during inclement weather.
Ballast and bilge piping has been similarly arranged in a pipe duct running through the double bottom of the vessel.
The tank top has been strengthened to 20t/m2 on top of all cargo holds. The vessel is equipped with four sets of deck cranes each with a 30t safe working load and 36m outreach. Each crane is supplied with a frequency converter system to ensure optimum energy efficiency.
Harald Lone, CEO, Newport Shipping, said: “Vessels built to this new design will feature advanced energy-efficient technologies making them very cost effective to operate.We have already partnered with shipyards in China, Korea and Turkey to offer competitive pricing structures.”
“The Greenlotus 32 is a real game-changer,” he said.
ABOUT NEWPORT SHIPPING UK LLP
Newport Shipping UK LLP is a ship management company, registered and headquartered in London, UK and provides a complete and comprehensive range of commercial and technical ship management services both for its own fleet and third party owners of dry cargo, tanker and chemical tanker tonnage.
Its commercial management service covers all aspects including chartering & operations, accounting, research & consulting, and demurrage & claims.
Newport Shipping’s fully owned subsidiary Ecoships A.S offers full technical and ship management services with focus on dry cargo ships, container vessels, and product and chemical tankers.
Its senior management team has extensive shipowning, ship broking and finance industry experience having spent decades in leading companies in Oslo, Istanbul, New York, Singapore, Hong Kong and Jakarta.
Floating terminals: offshore cargo handling made easy with Coeclerici
Coeclerici Logistics, the logistics division of Coeclerici Group, is one of the world’s leading bulk commodities transshipment companies with a history of more than 40 years in this specific field, writes Capt. Giordano Scotto d’Aniello, the Head of the Commercial Department at Coeclerici. Technical innovations, cross- disciplinary expertise, skill optimization, long-standing direct operational experience and a proven track record are the main strengths of Coeclerici’s logistics branch.
Coeclerici has engineered and promoted the use of ‘floating terminals’ throughout the world designing and developing different types of floating transshipment stations capable of lighterage/top-off operations, cargo transfer and self-unloading of many different dry bulk materials. These carry out all the same functions as a port terminal but with far smaller investments, lower management costs and less environmental impact.
The solution is based on a floating system which is able to load and/or discharge large ocean-going bulk carriers offshore, with a exceptional daily rate. The system can also be self propelled so that it can be moved easily from one location to another without the need for tugs and pilots. The versatility of the system is such that it is able to overcome draught restrictions, vessel size restrictions, lack of port facilities, environmental restrictions etc. And yet it should be simple enough to adapt to the local prevailing conditions and be operable with the local crew.
The flexibility of the system should allow it to handle all kinds of dry bulk cargo. Last but not least, the time of implementation of this system should be such as to minimize the losses being incurred by the end-users.
As regards self-unloaders in particular, we refer to vessels equipped with onboard cargo-handling systems, able to discharge its cargo without shore-based unloading equipment. For cargo we consider any dry-bulk commodity such as coal, iron ore, etc.
MAIN ADVANTAGES
- self-unloaders deliver more usable product than conventional vessels by virtually eliminating waste and contamination; v self-unloading vessels can discharge dry-bulk cargo at an unimproved dock without assistance from any shore-side equipment or shore-side personnel — they do not require any land-based assistance;
- self-unloaders can provide offshore transshipment operations, topping up or offloading into larger vessels.
- self-unloading vessels can reduce a cargo’s overall delivered cost per ton because they are fast, efficient and less capital- and labour-intensive than on-shore based systems;
- the new generation of self-unloader is equipped with advanced dust suppression systems. Dust suppression units are situated throughout the cargo handling areas, and the discharge booms are enclosed and fitted with water sprayers to further reduce dust during off loading; and
- finally they can also be used for seaborne trading, over dry material handling.
SOME EXAMPLE OF SUCCESSFUL COECLERICI’S PROJECTS INCLUDE:
- FTSs (floating transfer stations) Bulk Java/Bulk Borneo and Bulk Sumatra: the FTSs are non-propelled barges of 11,838dwt (Bulk Java and Bulk Borneo) and 11,855dwt (Bulk Sumatra), duly designed to smoothly perform coal transloading operations at Muara Pantai anchorage in Indonesia. The FTSs are equipped with two heavy duty cranes and two swivelling shiploaders, along with a combination of hoppers and conveyors. The FTSs are designed with a minimum air draught of 18.5m at maximum draught that makes it possible to transship and to guarantee from 2,000tph (tons per hour) to 2,400tph from barges to Ocean Going Vessels (OGVs) up to Capesize.
The systems are environmentally friendly and designed to meet the requirements of international classification societies and Coeclerici standards. Any coal spillage and pollution are prevented by anti spillage hoppers, spillage free grabs and closed conveyors belts. - FTS Bulk Celebes: custom-designed by Coeclerici for the specific needs of offshore coal transloading operations in Indonesia, this self-propelled FTS is suitable for both loading and unloading and for blending operations to manage different coal grades.
- Bulk Zambesi and Bulk Limpopo: the twin 53,776dwt transshipment units (TUs) have been fully designed and built by Coeclerici to load coal into OGVs, by means of sophisticated loading systems installed onboard, at Beira in Mozambique. The units have each been equipped with five heavy duty cranes, grabs, a belt conveyor system capable of transshipping at a peak loading rate of 5,500tph and state-of- the-art gears enabling a throughput of around five million tons of coal per year for this specific project.The vessels are in compliance with the latest international code resolutions for ship’s safety and security, protection of crew and of the environment.
- FTS Bulk Irony: the ultra hi-tech floating barge Bulk Irony is a geared self-propelled facility, developed and designed by Coeclerici Logistics to lighten vessels up to Panamax size. Since 2003, it has operated three miles from the Piombino coast, helping the Lucchini steel mill to overcome the depth restrictions of the port.
The system has an average lightening rate of 26,000 tons per day, using two heavy duty cranes and a conveyor system comprising four fully covered belt conveyors. Besides discharging iron ore and coal, the system is also capable of transporting and loading coils for export purposes. The system is in compliance with ISO14001:2004 and achieved the prestigious Environmental Management Audit System (EMAS) registration in April 2009.
Each of the above systems has been tailor-made according to customers’ technical and operational requirements, ensuring high performances (over contractually guaranteed parameters) and long lasting working lives, that guarantee to the clients a reliable solution for their needs.
Wear protection systems for self-unloading vessels
Wear-resistance specialists were approached by a global shipment management service provider, responsible for fleet and gravity type self- unloading vessels to provide a solution which would help reduce material build up, increase material flow and promote an easier cleaning regime along with an effective wear-protection system.
Kingfisher was approached by the global provider whose self-unloaders are expected to operate 24 hours a day without the need for stevedores or trimming crews, as this speeds up cargo handling, and further reduces port and demurrage costs. These types of vessels are capable of handling material up to 20,000 metric tonnes per hour, therefore effective equipment and continual process performance is a must.
The company’s technical superintendent stated,“Our core business is the shipment of iron ore. As the material is transported from ‘A’ to ‘B’, material is affected by a number of factors which contaminate the material and increase the moisture content within the ore, leaving the material lumpy and exceedingly sticky, which then builds-up on top of the A-frame inside the cargo hold.
The process of transporting material from ‘A’ to ‘B’ then becomes more difficult as it becomes extremely hard for it to be transported from one point to another without it sticking or building up within the unloading and loading points; likewise the lumpy material tends to cause considerable wear and abrasion within the pocket conveyor discharge chute.
Project manager Mark Bond commented, “Handling sticky iron ore is always a challenge for bulk material handlers as material characteristics can be extremely unpredictable especially where environmental factors are concerned. During such circumstances, end users do not have many options available, therefore maintenance engineers are then required to add in measures to help protect their systems and contribute to the on-going process and product output.
The technical superintendent added,“We approached Kingfisher as we required a solution which would reduce the material hang ups within the cargo holds and ease the cleaning process within the pocket elevator feed chute, as it is very important for us to keep our equipment material free and likewise eliminate the extra resources required to strip the cargo holds or implement additional cleaning regimes within the cargo holds and conveyor chute.”
After reviewing the issues, material flow and quantities, Kingfisher recommended to install a combination of wear resistant lining systems. Kingfisher K-PLAS material was to be installed top of the A frame, as the polymer material
promotes material flow, its smooth surface will allow material to slide down the system without causing material to ‘hang up’ on top of the A-frame, along with Kingfisher K-ALOX lining system 50mm and 25mm-thick 92P ceramic liners to offer protection to the main wear areas of the conveyor chute.
“The installation procedure involved cleaning and preparing the surfaces of the cargo holds, before our K-PLAS liners were installed,” stated Mark Bond. “Our aim is to offer the customer with a service which fits in with their requirements as Kingfisher’s service provision comprises full design, manufacture, surface protection and installation service.”
Operations director Graham Bailey commented, “Since the installation in July 2014, the customer has been reviewing the process and has confirmed the project has been a success. The results have been touchable, the hang-ups on top of the A-frame are now reduced to a minimum quantity and the pocket elevator feed chute now has less material build up, resulting in fewer wear areas.”
Shaking things up: self-unloaders use VibraFloor’s reclaiming system
VibraFloor’s innovative reclaimer has been used by several industrial sectors, seduced by the efficiency and simplicity of the technology which has been developed over the past three decades, writes Ivanny Salinas of VibraFloor.
The VibraFloor system is a major change brought into bulk ship design to optimize the reclaiming process, improve its efficiency while reducing the operation cost. The VibraFloor technology offers a number of valuable benefits, such as:
- 100% automatic discharge;
- no damage to ships’ structures nor handled products;
- low energy consumption; v very high discharge rate;
- automatic, safe and secure operation;
- no need for personnel or ancillary equipment (loaders); and
- no maintenance
Amongst recent projects, a woodchip barge is in operation in Chile which offers an unloading rate of 1,000m3/h; a second barge is under construction. Several ships have been put in operation along the costs of Norway, distributing fish feed.
The VibraFloor company is now working on orders for four additional Norwegian self-unloaders, ranging from 2,000dwt to 5,000dwt. These orders will be completed by the end of this year. More self-unloaders projects are under way in South America and northern Europe.
TECHNOLOGY AND OPERATION
VibraFloor is a reclaiming system, comprising independent modules laid side-by-side, end-to-end to cover the bottom of storage facilities and ship’s holds.
The system works by creating a wave in the flexible top plate of each module, instigated by a low-energy motor. This causes material (that has not already fallen by gravity) to collapse and be evacuated from the storage area.
High quality components and extensive research and development guarantee the efficiency and durability of the system. The design is flexible, customized to be fitted in ships’ holds regardless of their shape, and tailored to suit the stored product(s), conditioning and reclaim rate.
When required, ventilation ducts are provided to monitor storage parameters, temperature and hygrometry. All electrical components are ATEX certified to avoid the risk of explosion. Food grade and corrosion resistant standards are currently available.
All types of dry bulk product can be handled without human intervention, including sugar, flour, animal feed, seed grains, soya bean meal, wood chips, wood pellets, potash, urea, etc...
VibraFloor’s teams of technicians and engineers offer a high level of experience, and are available worldwide throughout the installation process to ensure smooth commissioning and efficient operation of the system.
Customers include sugar operators, fish feed distributors in Norway, biomass operators in Chile and Brazil, river operators in northern Europe.
VibraFloor is wholly committed to successful projects and clients’ satisfaction. Research and development in new sectors are consistently underway. The innovative VibraFloor technology with all its advantages is now available to the fertilizer industries and operators. It is expected to be made available shortly to the coal industry.
Customized transshipment and self-unloading solutions from Oldendorff
Most people within dry cargo circles would probably know Oldendorff Carriers. The German private company has been in existence since 1921 and today owns and operates more than 500 ships. It is considered to be one of the largest dry cargo carriers and has 19 offices around the world.
One area of the business which is perhaps lesser known to people is the ‘Oldendorff Project Department’ which provides tailor made transshipment solutions to clients that are in need of specialized logistical services and equipment.
The department has grown to over 700 people counting office staff and people actively on board various types of marine crafts and transhipment units.
Oldendorff currently manages transshipment activities in Guyana,Trinidad,Turkey and the Arabian Gulf. The commercial and technical management teams are situated in Lübeck Germany in the company headquarter and in Singapore.
Common for these transshipment projects are that they run for multiple years and sometimes include ocean freight contracts which means Oldendorff provides an all-inclusive logistical and transportation solution to the client.
‘Our clients are industrial companies which need a reliable long term partner guaranteeing their offshore logistics and transportation requirements are taken care of with utmost diligence — the relationships with our customers are very close for that reason’ says Managing Director, Projects Jacob Juncher.
Oldendorff has been engaged in self-unloading vessels for two decades and has several vessels committed to the CSL Pool which mainly operates in the Americas. “Our self-unloaders are employed and commercially handled by the pool whilst technical management is done by Oldendorff — the pool has offered a great way for us to differentiate and explore others types of ships than standard bulk carriers,” says Juncher. “A lot of experience in handling specialized equipment has been gathered over the years — experience we have been able to utilize elsewhere.”
The first transshipment project in which Oldendorff engaged is situated in close proximity to Iskenderun in Turkey. To guarantee timely and efficient coal supply to a new power plant, Oldendorff designed and constructed one of the world’s largest floating coal terminals. The Isken was delivered in 2002 and handles more than 3mt (million tonnes) of coal per year. “We have a team of 94 highly experienced people in Turkey. We are very pleased with the operation,” says Max Zentgraf, Manager Projects. “The Isken is a piece of bespoke equipment — it is the only one of its kind and has worked flawlessly since the beginning. We can fully discharge a Capesize in four days which is better than many shore installations can achieve,” says Zentgraf.
Oldendorff’s second project commenced in 2006 with the establishment of a barge and transshipment operation in Guyana handling bauxite for one of the world’s leading Alumina producers. “We employ 250 people in Guyana and have committed a large amount of equipment to service our customer. The operation is highly complex since we transport bauxite in our barges down a 250km-long stretch of the Berbice river which has very narrow bends — it requires special skillsets to navigate safely. Luckily we got very good people,” says Mia Gerritzen who is the project manager for the Guyana operation. Oldendorff is completely self-sufficient in Guyana having built a compound with living quarters close to the transhipment basin in New Amsterdam. There is even a jack-up dry dock which is used to maintain the 20 × 3,000 tonnes barges, tugs, crew boats and pilot boats. The transshipment is done by a Figee Lemniscate floating crane.
Oldendorff has specialized in transhipment and lightering operations in the Arabian Gulf since 2009. It currently operates a number of Panamax transhipment vessels with heavy duty side mounted cranes and conveyor boom systems which discharge at fast rates in to shore. There are also three self-propelled barges in operation in Abu Dhabi that services a large steel mill situated next to a channel with limited draught. “We are currently servicing a number of clients in the region with our transhippers and we believe there is still potential for growth,” says Linda Kongerslev, General Manager of EOL, an Oldendorff joint venture company based in Abu Dhabi. “Our view is long term — it has to be. Our clients invest and build for the future. Transshipment is needed in many places due to lack of adequate water depth for large bulk carriers. We have the equipment that can safely and efficiently deliver the product to the clients and reduce the time that the bulkcarriers are tied up for discharging,” says Kongerslev.
Oldendorff has two new customized 94,000dwt post-Panamax transshippers delivering in 2015 which will complement the on-going operations in the Arabian Gulf.
Oldendorff’s most recent transshipment project is located in Trinidad. The operation has been on-going since 2012 and primarily deals with transloading of iron ore from Handymax to Capesize vessels. A 120-man strong team runs two floating cranes in the Gulf of Paria which is naturally sheltered and enjoys calm weather all year around. “We haven’t had a single day of downtime due to winds or swell,” says Scott
Jones, Director Projects. Our operation is very versatile and besides from iron ore we have also handled coal and bauxite. The savings the customers enjoy are significant when they compare the all in rates Oldendorff offers — to the rates they would have to pay sending small ships far away,” says Jones.
The Oldendorff Project team has also been involved in design and implementation of new off shore equipment which is tailor made for clients that decide to operate themselves. “We look at anything that can provide the customer savings and efficiency improvements. “Says Juncher,‘it is like working in a Research and Development company where there are no limits — it is fun!”
In 2013, Oldendorff started a project team in Singapore. The team is headed by Jason Baird who has a long background in commodity trading companies. The aim is for Oldendorff to start offering their transhipment and logistical services to their customers in the Asia-Pacific and Indian ocean region.