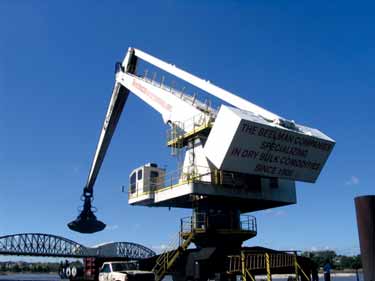
From pit to port: stock management solutions from RONIN
RONIN BULK COMMODITY INVENTORY MANAGEMENT SOLUTIONS
Imagine a pit-to-port stock management solution that provides constant knowledge and control of stock levels, grades, sizing, locations and provides daily reconciliations between book and actual physical values. Imagine having all of this right at your fingertips. This is now a reality, thanks to RONIN’s pit-to-port stock management solution.
The pit-to-port stock management solution from RONIN provides constant knowledge and control of stock levels, grades, sizing, locations and daily reconciliations between book and actual physical values. This is done by utilizing the company’s ARTEMIS LASER SCANNERS and proprietary software,ART, to enable accurate 3D surface mapping, stock management and accounting.
Whether in the mining, milling, trading, smelting or industrial sectors, production, financial, collateral, marketing and logistic managers constantly have a need for more accurate stock management and technology.
RONIN is a solutions company catering to the needs of these bulk commodity handlers in the form of accurate, laser-based, inventory management systems and surveying. The Ronin group comprises offices in Johannesburg and Richards Bay in South Africa, as well as in Buenos Aires, Argentina and Montevideo in Uruguay. From these locations RONIN is able to service the Southern African and South American markets and port users. Ronin also has representation in Europe and is currently in the process of setting up permanent offices in Mozambique and Zambia.
RONIN’s ARTEMIS solution is a surface mapping laser device which scans and plots the entire surface area of a stockpile, using one or multiple scanners. This is accomplished by taking over 10,000 distance measurements, per scanner, over the surface of the stockpile, as seen left. From the plotted surface area, a point cloud is formed creating a 3D profile of the stockpile.
By using this point cloud and taking into account ground levels, structures present and/or the storage vessel dimensions, RONIN is able to accurately calculate the volume of the stored product. The ART Software platform is the brains behind the system, providing valuable functionalities to assist with finance, collateral management, logistics, marketing and production. The ARTEMIS scanners communicate wirelessly to a dedicated ART PC on-site.
Here all the scan data is processed and displayed on the graphic interface. This interface shows site summaries, occupied and available tonnages, communication statuses, grades, 3D graphic representations and histories. The ART PC is connected to the clients’ network so that management can have up to date knowledge of stock locations, quantities, grades, sizing and histories. All this information is ready available on excel spread sheets or any other CSV files the client should choose to utilize.
Integrations enable the system to attribute weighted averages of bulk densities, moistures, sizing, calorific values or any other grading the client would like to utilize, to be applied every stockpile, bunker or silo on the network. This enables current and weighted averaged grading/sampling data to be utilized and applied, providing greater accuracies of tonnages and grading figures. This integration also enables daily reconciliations to be done between the book value and actual physical stock.
The RONIN ART Head Office Server (HOS) is available for complete control of all the clients operations at a head office level. This is done by networking all the ART PCs on the various sites and processing all the data of each site and stockpiles via a sequel server. This makes daily stock management from a head office prospective a reality.
All hardware and software is developed, manufactured and maintained from RONIN’s Johannesburg office. The software platform, installation and reporting is customized per client, per site, taking into account the objective and requirements set out by the client.
AIMS is RONIN’s alternative solution to the permanent installations as a moment-in-time stock-verification service. Using the same principles of the ARTEMIS scanner, in terms of surface mapping, AIMS provides accurate volumetric data and 3D graphic representations. This service is available for silos, bunkers, warehouses or open-air stockpiles. Bulk density verifications are also done on each stockpile to enable reports in tonnages. The AIMS report includes volumes, tonnages, 3D representations and any additional observations (i.e. contamination, excess moisture etc.). Dependent on the scope of work, reports are published within 24 hours following the survey.
The company’s Richards Bay office, Ronin Independent Surveyors, is in a key position to service the port users of the Durban, Richards Bay and Mozambican ports. In addition to the services and systems mentioned above, they provide an independent cargo monitoring service for in- and outbound cargo. This includes tally services, port superintendence/cargo monitoring, cargo reconciliations, stock auditing, density verifications, marine surveying, quality inspections, sampling and analysis, tarping, ribbed truck cleaning and cargo screening. These are independent services with high levels of service quality, ensuring customer satisfaction at all times. Quality on-board weighing systems for front-end loaders are available to assist with stock handling and management. These measure the hydraulic pressure needed to lift the bucket, converting the result into tonnages. The Loadmaster 9000i is trade approved in all EU countries and many countries worldwide, which eliminates unnecessary trips back and forth from the weighbridge. With functionalities such as an internal database for up to 1,000 products and/or customers, batch weighing capabilities, target weights, overload logging, tracking and telemetry. The Loadmaster is a simple, cost effective and valuable solution for stock handling and management.
Cutting coal handling costs with E-Crane: the original balanced crane
E-Crane continuously holds a strong position in the bulk material industry. This is no surprise, because its equilibrium balanced cranes were the very first of their kind. After 25 years of manufacturing, adding new features and further specializing, the E-Crane has evolved into what it is today. More than 200 E-Cranes are operating on all continents, handling a wide variety of various bulk materials. The coal industry, in particular, benefits from all of the advantages the E-Crane has to offer.
CUSTOM ENGINEERED TO SUIT ANY COAL FACILITY
When an E-Crane is purchased for a project, it all begins with the initial design. E-Crane engineers visit each facility to inspect the location and to get an understanding of the project requirements and possibilities for the site. If the coal facility requires specific needs, E-Crane engineers custom build the E-Crane to meet these requirements. They help with the entire facility design including hoppers and barge haul systems which are sometimes required at coal handling facilities. The modular design of the machine enables custom solutions with off-the-shelf components and pricing and allows for minimal time between order and commissioning. Coal can be a difficult material to handle depending on the situation. In order to eliminate spills and carry-back, E-Cranes are delivered with a clamshell grab that utilizes a powerful closing force. This gives the bucket excellent penetration and affords maximum fill, which can also be a time and cost saver for a coal handling facility.
With a maximum outreach of 156.8ft (47.8m), the E-Crane is capable of unloading up to Panamax-sized vessels. E-Cranes are also capable of unloading any type of barge or ship with minimal cleanup. Minimizing clean-up reduces the total unloading time saving money on the overall operation. This also leads to a faster turnaround of ships and barges due to greater efficiency.
STATE-OF-THE-ART TECHNOLOGY
Operating and controlling an E-Crane is easy due to its simple, ergonomic and intuitive design. Operators with little experience handling large equipment become skilled E-Crane operators in no time at all. The simple control system builds operator confidence, allowing for reduced cycle times to maximize productivity.
The innovative, balanced design of the E-Crane contains fewer moving parts than typical material handlers making it easy to maintain. The inherent design of the machine means less wear and tear on main components, providing longer service life with greater availability and reliability for mission-critical unloading. The ‘pit-stop’ preventative maintenance for the E-Crane is fast and simple, so that the E-Crane runs continuously in a cost effective,‘race car’ style operation. This eliminates costly maintenance downtime. E-Cranes now come with the reliable and user-friendly control system called the EMM, or Electronic Machine Manager. This built in system is a huge innovation in data collection technology, and allows for real-time data collection of things such as running time, how many times the E-Crane hits a fault while in operation, whether there is an overload or overheat, and more. Some even stream live, real time video of the E-Crane while in operation.
TURNKEY TERMINAL SOLUTIONS
A successful operation does not just stop with the E-Crane or material hander itself. Other equipment is necessary to work alongside the material handler or crane to efficiently handle the coal. E-Crane engineers assist in making these decisions for most of their customers. Engineers work with the customer to help them choose the right hoppers, barge haul systems, and E-Crane undercarriage required for an efficient operation.
E-Crane has over 25 years of experience in the coal industry and are the original manufacturers of the equilibrium crane. This invaluable experience and knowledge along with the benefits of the E-Crane prove to be the ideal solution for coal handling terminals.
CASE STUDY: BEELMAN RIVER TERMINALS
Beelman River Terminals conducts coal offloading operations at its terminal in Venice, IL., situated on the east bank of the Mississippi River just north of St. Louis.
The crane was engineered specifically for the Beelman facility and is mounted on a four-legged pedestal directly on the dock. The receiving hopper is barge mounted and captive between dolphins. This arrangement allows for a full fluctuation of water levels without affecting the unloading cycle time.
At the time of installation, the full facility and infrastructure at the Venice facility was not completed. The E-Crane was originally working every day offloading coal directly to trucks. Even with five trucks making continuous round trips, the E-Crane was outpacing them.
Operator friendly
The operator, who was new to operating heavy equipment prior to the E-Crane installation, quickly became very productive with the new E-Crane. In less than three months, the operator was already offloading full 1,800dwt barges in less than two hours, including clean-up. According to the E-Crane operator,“The machine is great! Very comfortable to operate.” It was also reported that,“The E-Crane does a great job at the bottom, leaving little material in the barge, making clean-up quick and simple. The powered rotator on the grab makes cleaning the corners quick.” The E-Crane at Beelman River Terminals continues to prove itself as an efficient and cost-effective solution to the coal handling operation.
Indonesian coal transshipping made easy with Swire CTM Bulk Logistics
The two Princesses continue to excel in coal loading operations in Kalimantan, Indonesia. Swire CTM Bulk Logistics (SCBL) owns the floating crane Princesse Abby and the floating transfer station Princesse Chloe, in a joint venture with PT. Mitrabahtera Segara Sejati Tbk Jakarta in Indonesia.
THE FLOATING CRANE ‘PRINCESSE ABBY’
Princesse Abby is essentially a floating crane, i.e. single crane mounted on a pontoon, being used for the direct transfer of coal from the barges to the holds of oceangoing vessels up to Capesize type. What make it stand out is that its hull structure is made by duly reinforced longitudinal frame with spoon bow, inclined stern and two skegs aft. Bilge keels are fitted on each side to the extent of about three quarters of the length of the pontoon; structural anti-rolling fins are also fitted in way of the stern skegs. It is equipped with movement-dampening devices and suitable dynamic factors to bear stress and fatigue resulting from continued heavy duty work in open seas. These are all developed and incorporated in the Princesse Abby’s design, making it less sensitive to adverse weather conditions as compared with standard floating cranes.
Since the commencement of operations, Princesse Abby has loaded 173 vessels, between Panamax and Capesize, transshipping over 10mt (million tonnes). Its best performance rate has been recorded at about 25,123 tonnes per day.
THE FLOATING TRANSFER STATION ‘PRINCESSE CHLOE’
Princesse Chloe is equipped with two Liebherr cranes, instead of just one, which have been strategically mounted on a pontoon,
with respect to the hoppers so as to minimize the slewing movement, thereby increasing the cycle time and efficiency. The cranes work in conjunction with a cargo handling system, supplied by Bedeschi, which consists of two duly designed hoppers and an array of conveyor systems leading to a telescopic/shuttle shiploader. Coal from each of the hoppers is extracted by means of individual variable-speed belt feeders. These frequency-controlled feeders extract coal from the hoppers and transfer it to the longitudinal conveyor. The belt width of the feeders is kept high and the speed is low to ensure uniform extraction of coal from the hoppers. Another conveyor then transports the coal longitudinally through the length of the floating transfer station: from the transfer point, a transverse conveyor helps in crossing over the entire beam of the terminal and joins the final conveyor leading to the shiploader. All the conveyors are enclosed to avoid airborne pollution.
The shiploader is a shuttle/telescopic boom type. It has a 19m air draught, which makes the Princesse Chloe capable of loading large vessels up to Capesize type. The shiploader is capable of swivelling by means of geared slewing rings and luffing by means of hydraulic mechanism. The entire cargo handling equipment is constructed and manufactured with the highest classification for heavy duty work in open sea conditions. The equipment has been designed for a heel and trim of 5° and 3° respectively. Another unique feature of Princesse Chloe is its double bow structure, which makes it capable of mooring on both sides and thereby increasing its flexibility to a large extent.
Princesse Chloe was delivered in April 2011 from Keppel Subic Shipyard and started coal transshipment operations at the Muara Pantai anchorage in the Sulawesi Sea (East Kalimantan) for PT Berau Coal.
Since then, Princesse Chloe has loaded 88 vessels, between Panamax and Capesize, handling about 7mt, with an average daily loading rate up to about 51,000 tonnes of coal, and achieving a best performance rate of about 56,500 tonnes daily. It also has an annual capacity exceeding 9.5mt.
Both Princesse Abby and Princesse Chloe have been designed by Logmarin and Interprogetti, and have been built under RINA classification and Logmarin supervision. The cranes are designed and supplied by LIEBHERR, which offers proven technologies in the design and operation of off-shore transshipment systems. Included are specific features for open water and heavy duty conditions such as duly designed heavy duty hoisting winches, strengthened boom, the slew bearings conceived with triple roller and four equally distributed slewing motors to minimize the risk of breakdown to one of the most critical components of the crane, four-rope grab configuration, heel and trim alarm systems, thus ensuring high turnover, efficient and effortless loading/unloading from most types of vessels up to modern Capesize vessels, as well as smooth and wider life cycle time.
The cargo handling system on the Princesse Chloe has been designed, manufactured and supplied by Bedeschi — an Italian company which specializes in the manufacture of all kinds of material handling equipment for both onshore and offshore applications.
BRUKS Rockwood reports on recent coal equipment contracts
BRUKS Rockwood, headquartered in Alpharetta, Georgia, USA, is a major manufacturer specializing in designing, installing and maintaining bulk material handling systems for the paper, energy, port terminal and minerals industries. Its systems have a wide variety of uses, including coal handling. BRUKS Rockwood is a division of BRUKS Group headquartered outside of Stockholm, Sweden, and part of the JCE Group of companies. BRUKS Rockwood’s innovative designs help manufacturers move their bulk materials more efficiently with automated systems that reduce labour and equipment costs, reduce product waste/loss, improve the quality of the delivered material, and reduce ongoing maintenance costs in harsh environments.
PRODUCT LINES/SERVICES
BRUKS Rockwood offers a wide range of product lines for handling bulk materials — including coal — from material receiving, processing, storage, reclaim, and delivering to the process. Although the company custom designs equipment to suit nearly any application; its standard equipment supply for bulk handling includes truck unloading equipment, stacker/reclaimer technology, and shiploaders.
Each play a pivotal role in the successful operation of an efficient bulk materials system, with the most recent projects for BRUKS Rockwood including the handling of coal, sulphur, pril, petroleum coke, wood pellets, and biomass. Careful attention must be paid to each design for handling a variety of goods with differing material characteristics, from viscosity, delicacy, combustibility, and dusting.
COAL ACTIVITY
Most of BRUKS’ recent proposal activity with handling coal has been mainly in export facilities with a few domestic projects. Currently in the construction phase is its circular polar stacker at the Port of Lake Charles. Sitting atop a concrete pedestal this stacker is designed to store both coal and petroleum coke at the
port before being reclaimed for export. In order to maximize the storage volume, this stacker is equipped with a shuttling feature that extends the stacking range an extra 70ft. Also coming off the ground is our most recent ship loader project at the Port of Portland. This shiploader is fixed and utilizes both slewing and shuttling to efficiently load vessels with fly ash, a byproduct of coal, at a rate of 2,450tph (tonnes per hour). This is the second shiploader BRUKS has provided for this terminal operator in the last two years; the other installation being at the International Marine Terminal in Port Sulphur, Louisiana. This machine was successfully commissioned in January 2012 and was delivered and commissioned in less than one year. With a design capacity of 5,000tph, this shiploader utilizes travelling, slewing, and luffing features to efficiently load coal into vessels in place. This design drastically reduces dock time and manpower requirements while providing maximum vessel size flexibility.
Another coal project going up is the company’s 210ft radial stacker for a large utility company in the Midwest. This radial stacker travels along rails about its axis to build its pile at a rate of up to 1,000tph per hour. The contract was awarded based on the successful delivery and commissioning of a 220ft cantilevered coal stacker in April 2011. This cantilevered stacker is an integral part of the coal receiving system with an automated stacking capacity of 2,500tph. It is designed to build a circular/conical pile without the use of intermediate supports which provides for unobstructed access to the pile and the base of the machine.
COAL OUTLOOK
With new domestic coal projects slowing down, BRUKS expects most future projects will involve process improvements at existing plants. Fortunately, the terminal business should remain active.
Keeping control of dust in coal handling operations
The Raring Corporation (TRC) is a specialist in ADSTM fog-based dust control systems, which are ideal for controlling dust emissions in coal handling operations. Founded in 1984 by its president David Raring,TRC has provided dust control solutions in the Americas, Australia, Africa, India and Europe. With experience in both fog and water based dust control systems, David Raring brings experience and expertise to every project TRC develops.
TRC uses Agglomerative Dust Suppression (ADSTM) , the in-situ collection of dust. Using no chemicals, properly applied fog prevents fugitive dust from contaminating its environs, agglomerating (clustering) with the dust and causing it to return to its source material.
Fog, or clouds, as cleansing agents are daily observed in nature; evaporated water condenses around small particles of dust, then agglomerate until the resulting clusters are large enough to return the pollution to earth as rain.
This technology works well in the most demanding environments, from extreme cold to extreme heat, from arid to humid environs. With a measured efficiency of up to 99.29%, TRC is justifiably proud of the solutions provided to its clients.
TRC’s equipment is effectively used in many applications including rail and truck dumps, bins and hoppers, crushers, screens, and conveyor transfer points.
In order to effectively sell and support TRC’s equipment, long- lasting partnerships with licensees and manufacturers’ representatives exist throughout the Americas, Austral Asia, India, and other parts of the world.
During the past few years,TRC has developed a PLC-based control system which performs diagnostics and self corrective routines. Utilizing 3-D modelling to analyse dust and fog containment ensures optimum nozzle placement. With a constant air purge,TRC’s nozzles neither freeze nor plug with dust.
Compared to dust extraction, the capital outlay for an ADSTM system typically costs one tenth to one half as much, operating costs are one quarter to one half as much and maintenance costs are minor, using only common hand tools. In addition to these benefits, the elimination each bag house also eliminates one point source of dust from the system, one less point to monitor and report.
Not only are the systems cost efficient, but they are also safer, as a dense blanket of fog absorbs carbon monoxide, thus reducing explosion risks. And any ignition source entering a fogged enclosure will be less likely to cause an explosion since its radiated heat is lost to evaporation.
Over the years TRC has successfully partnered with many clients to address their dust control challenges. In coal TRC’s clients include producers such as Arch, Rio Tinto, BHP, Peabody, Rag, and Consol and users such as Detroit Edison, Southern Companies, Consolidated Edison, and First Energy. And TRC’s equipment is used in coal ports from Madagascar to Patagonia.
Two of the company’s recent contracts include a rotary rail dump for Detroit Edison and a ship loading facility for Mineria Isla Riesco:
- Detroit Edison: replaced an existing baghouse with a PLC based ADSTM system for automated dust control during train unloading.
- Mineria Isla Riesco in Chile: provided an ADSTM system to control dust at crushers and transfers to shiploading boom conveyors.
Sandvik signs major coal mining systems order with Sasol
At the end of December 2012, Sandvik Mining signed a mining systems contract with Sasol Mining (Pty) Ltd for the Shondoni Mine Materials Handling project in South Africa. The value of the contract is approximately 650 million SEK and will contribute to Sandvik Mining’s business during the years 2013 until 2015.
The order entails the supply of underground bunker and incline conveyor, surface bunker and overland conveyors for a new coal mine. The scope of supply includes engineering design (E), procurement (P) and construction (C) for the Shondoni Mine Materials Handling system.
“The size and complexity of this system and the fact that Sandvik provides a complete integrated mining system of Sandvik surface and underground mining equipment, again demonstrates our capability to deliver wide-ranging high-tech solutions in the area of continuous mining and materials handling applications,” says Gary Hughes, President of the Sandvik Mining business area.
THE SANDVIK GROUP
Sandvik is a global industrial group with advanced products and an excellent reputation in selected areas — tools for metal cutting, equipment and tools for the mining and construction industries, stainless materials, special alloys, metallic and ceramic resistance materials as well as process systems. In 2011, the Group had about 50,000 employees and representation in 130 countries, with annual sales of more than 94,000 million SEK.
SANDVIK MINING
Sandvik Mining is a business area within the Sandvik Group and a leading global supplier of equipment and tools, service and technical solutions for the mining industry. The offering covers rock drilling, rock cutting, rock crushing, loading and hauling and materials handling. In 2011 sales amounted to about 32,200 million SEK, with approximately 13,200 employees (pro forma rounded numbers).
Verachtert Netherlands BV — specialist in work tools for excavators and wheel loaders
The Netherlands boasts a long tradition of supplying the world with innovative engineers and builders of large infrastructure projects. On the strength its centuries’-old experience in sea defences and water engineering works — brought about by necessity as most of the country lies below sea level — a slew of related supply industries has emerged servicing the country’s burgeoning portside and infrastructure industries. One such supplier is the Dutch firm ofVerachtert. In 2003,Verachtert became part of the Pon company, one of Holland’s largest family businesses and the holding company of a group of companies operating in mobility-related industries in countries worldwide. With 60 years’ experience in the trade, Dutch Verachtert has earned international recognition as a specialist in work tools for excavators, wheel loaders and cranes of all brands. From its
home base in ’s-Hertogenbosch (NL) the company engineers and sells products such as quick couplers, buckets, grabs, shears and hammers, which are widely recognized in the industry for quality and productivity. Its customer base includes international clients operating in earthmoving, road and water engineering, demolition, scrap metal processing, recycling, general industry and bulk handling. In many cases the products are designed and engineered to meet the customer’s specific needs and wishes. All work tools are supplied inclusive of an extensive services package, covering expert advice in choosing the best tool for the job through to maintenance and repair services. Moreover, the company prides itself on being a major European supplier of pre-owned worktools.
EXPANDING GRIP
With its recent takeover of the Dutch DCC-grabs Verachtert has consolidated its position in the field of mechanical and electro hydraulic grabs. The newly acquired asset enables it to offer customers an even broader product portfolio. The takeover has also paved the way for the crew at Verachtert to start servicing related segments of heavy industry such as mining and quarry operations. The mechanical and electro hydraulic work tools made by DCC Grabs are engineered for maximum operational efficiency in bulk cargo handling, dredging and recycling industries.
HIGH-VOLUME COAL BUCKETS
Verachtert designed and sold three special coal buckets (CAT988 and CAT990) to the OBA and EMO terminals at the ports of Amsterdam and Rotterdam, which are part of the HES-group.
OBA’s and EMO’s activities concern unloading and loading dry bulk cargo from/onto sea going vessels, coasters, lighters, trains and trucks as well as bulk storage. The challenge with this particular order was to design the most efficient type of bucket offering both maximum storage capacity and resistance to wear. The CAT988 coal bucket packs a volume of 16,500m3, whereas the CAT990 bucket holds 22,500m3. The capacity of the machines was enhanced through integrated suspension, large jaw action and smart engineering, resulting in a significant reduction of the operational cost per tonne of bulk cargo handled. The bucket is constructed largely from Hardox and provided with chockey bars for extended operation. A perfect example of the type of customized solutions Verachtert offers for practically every conceivable situation.
FUNNEL BUCKET
The Vantec funnel bucket is used for efficient bulk cargo handling and will handle all type of dry, loose bulk cargo transfers. A funnel bucket uses a tipping mechanism along with a hydraulic valve for the controlled loading of bulk vehicles and/or train carriages with a wheel loader. It eliminates the need for expensive investment in a single bulk transport and storage system (conveyer belts, silos, etc.) installed in a permanent location. The funnel bucket is exceptionally flexible and, like any ordinary bucket, can be deployed anywhere. The funnel bucket is engineered and customized by Verachtert to match customers’ specifications and the type of cargo to be handled. The advantages cited by the company include the hydraulically
controlled valve underneath the funnel bucket which enables controlled, reduced off-loading without spilling with a minimum of development of dust. Also, the funnel bucket saves on wage costs as only one operator is needed to operate the wheel loader and fill the bulk carrier. Measured loading/unloading of the funnel bucket is very fast (approximately 25–30 seconds for a 3.5m3 load), making this Vantec system highly efficient and the investment is soon recovered.
NEW VANTEC CUSTOMIZED PRODUCTS FOR EVERY APPLICATION
Verachtert is an official dealer for trusted brands such as Caterpillar and Engcon. With the Vantec range the company complements its portfolio with a line of tough work tool products based on extensive knowledge, built over many years’ experience in the trade and reflecting a complete understanding of work conditions, materials, productivity and efficiency. All products are customizable to meet customers’ specific needs.
Engineering solutions for coal storage and handling
Often, coal is stored in bunkers, silos or gravity-reclaim stockpiles at power plants. Unless properly designed, the storage system can experience flow problems such as flow stoppages, limited live storage capacity, feed rate limitation, etc. This is also true for self-unloading ships used to transport coal as well as for the surge hoppers and bins used to store fly ash and bottom ash. Similarly, if the feeder and transfer chutes are not designed properly, they can result in flow problems.
These problems can be avoided by properly designing or retrofitting the storage and handling systems.
Established in 1966, Jenike & Johanson is a major technology company which provides solutions for reliable storage and handling of bulk solids.
Problems solved/avoided by Jenike & Johanson equipment:
- flow stoppages or erratic flow due to arching and ratholing, in bunkers, silos and reclaim hoppers;
- limited live storage capacity in silos, bunkers and stockpiles;
- chute pluggages due to cohesive coals; v limited flow rate, flooding, and dusting of fine coal and fly ash;
- premature wear of material contact surfaces; and v solids handling equipment failure investigations.
Bulk solids handling problems are often the major cause of costly downtime and demurrage charges for many facilities, especially during startup. These same flow problems continue plaguing on-going operations by limiting throughput and creating safety and health risks, as well as reducing equipment life, increasing maintenance costs and causing premature equipment failure.
To address these costly problems, Jenike & Johanson has developed proven ways to design handling equipment that will promote reliable, smooth and unrestricted flow of bulk solids. Bulk solids handling equipment design should not be a trial-and-error approach; Jenike & Johanson doesn't guess at material properties, it measures them. It has one of the world’s largest and most complete laboratories for characterizing the flow properties of bulk solids under representative environmental conditions. For over 45 years, Jenike & Johanson has focused on developing first principle theories on bulk solids flow and conveying behaviour.
Its services include:
- coal flowability study;
- silo, bunker, hopper design review and recommendations;
- belt/apron feeder and interface design; transfer chute design;
- calculation of material flow induced loads on silo and hopper walls;
- and training on solids flow and pneumatic transport
Jenike & Johanson combines test results and real world project experience, which yields the best solution in terms of reliability and cost-effectiveness. Its skilled and experienced engineers provide detailed structural and mechanical design of solids handling equipment, and routinely design stockpile and gravity reclaim systems, silos, feeders, loading and transfer chutes and custom equipment (e.g., standpipes, large slide gates, etc.).
Bulk handling performance in India — setting new records with Liebherr
Liebherr mobile harbour cranes are mighty tools. In August 2012 Krishnapatnam Port set a new record for unloading coal using advanced Liebherr mobile harbour cranes (LHM). The state-of-the- art machines discharged 122,247 tonnes of coal in just 24 hours. This new record surpassed Krishnapatnam’s previous record of discharging 106,171 tonnes in just 24 hours, set in July 2011.
In April 2012, two Liebherr portal cranes of Adani Petronet Dahej Port Pvt. Ltd. (APPPL) broke the old record for coal discharging. A total of 60,077 tonnes of coal were unloaded in just 24 hours with two LPS 600s, the award-winning model in the category ‘Crane of the Year’ at the International Bulk Journal Awards 2011.
The LHM 600 is capable of handling bulk at up to 1,800tph (tonnes per hour) in standard configuration. The Liebherr Portal Crane (LPS) is an efficient combination of a space-saving portal and the proven mobile harbour concept. Particularly on narrow quays, individual portal solutions permit trains and trucks to travel below the portal. Due to the closed hydraulic system and an electronic system which is military proven and tested, Liebherr technology is absolutely resistant to all types of dust and dirt.
Liebherr’s Cycoptronic® ensures sway-free load motion. This optional tool automatically initiates dynamic counterbalancing movements and equalizes transverse and longitudinal sway of the load while operating at maximum speed. Additionally,
Cycoptronic® extensions Teach-In and Vertical Line Finder are available. If efficient bulk handling is required,Teach-In feature is an optimal extension to Liebherr’s anti-sway system. This point- to-point control for semi-automatic operation pilots the crane to pre-determined loading and unloading points at the highest possible speed. If one of the predefined points is reached the crane automatically stops. Furthermore, automatic steering to target points without any load swing and the possibility to stop crane motion at any time leads to a notable increase in both safety and speed. The Vertical Line Finder guarantees that the boom is exactly vertically above the load, thereby preventing side loading of the crane for a longer lifetime.
Liebherr offers a wide range of mobile harbour cranes and additional supporting tools in order to guarantee efficient bulk handling for ports worldwide.
LIEBHERR MOBILE HARBOUR CRANES IN INDIA
Early in 2004, the first Liebherr mobile harbour crane started operation for South West Port Limited in Mormugao, India. Seven additional deliveries in the same year marked the beginning of a success story. Since then the Indian Liebherr crane population has grown steadily as more and more terminal operators opted for Liebherr’s advanced mobile harbour cranes. Now, more than 60 LHMs load and unload cargo, mainly bulk, in Indian ports and 2012 was another strong year for Liebherr mobile harbour cranes in India. Another very positive aspect is the high penetration of electric drive, Liebherr’s alternative drive system allowing for eco-friendly land-based power supply. Approximately every second LHM delivered to India is equipped with E-Drive.
Furthermore about 90% of all Liebherr mobile harbour cranes delivered to Indian customers are operated in four rope configuration. This highlights the importance of bulk handling for the Indian port industry.
A close look at the order intake in recent years proves that there is a global trend towards stronger machines. That’s why demand for Liebherr’s high-capacity cranes increases year by year. The strongest mobile harbour crane, type LHM 600, has a maximum lifting capacity of 208 tonnes.
SMAG’S PEINER GRABS: seizing the attention of the coal market
For more than 60 years, Salzgitter Maschinenbau AG — SMAG for short — with its product, PEINER grabs, has stood for quality and customer satisfaction in the field of bulk goods handling. The wide range of grabs and lifting equipment (turnover business year 2011/2012 of €105m) allows SMAG to provide the right answer to every customer request in the field of geared bulk vessels. Owing to its many decades of expertise in development and construction of grabs, its customers have put their trust in the company and relied on PEINER grabs, particularly in the difficult market situation of recent years. To further develop this expertise, the company makes above-average investments in the research and development of products. Thus new designs and alternative materials are continuously brought into serial production. An example of the current development is an orange peel grab with a capacity of 56m3 and a weight of 30 tonnes. The goal of SMAG is to continuously improve its products while taking into account the requirements of the market.
At SMAG, the customer is always the centre of attention. The size, shape and dead weight of grabs may vary and, therefore, be tailored in every respect to the needs of customers. PEINER grabs are adapted both for lifting devices and for each application to always find an optimal solution.
SMAG offers a wide range of grabs suitable for coal handling. PEINER four-rope dual scoop grabs (VSG) achieve maximum efficiency through the optimum balance between dead weight and crane capacity and also require low maintenance. Ideal for loading and unloading coal from ships are PEINER scissor grabs (SCG). Based on the scissor principle and the double reeving of the closing ropes, the SCG is the fastest and most efficient grab for coal handling. It goes without saying that electro-hydraulic grabs from SMAG are a good choice when it comes to coal handling as well. Last year, SMAG manufactured various grabs for coal handling projects in Asia, Europe and South America, for example PEINER four-rope dual scoop grabs with a capacity of 32m3 (Poland) respectively 34m3 (Brazil) and PEINER Scissor Grabs with a capacity of 30m3 (Indonesia).
A well-proven alternative to motor grabs, especially for countries with weak infrastructure, is the PEINER radio- controlled single rope grab. It is particularly suitable in this case because it is not only compatible with many lifting devices (a simple crane hook is enough), but also impresses with its user- friendliness and versatility. Using spill and kick plates, the grab can be adapted for a variety of bulk materials and therefore is suitable for handling coal, too. Thus, within a very short time, any deck crane can be used for bulk goods handling without additional equipment. An external power supply is not required.
The maintenance is reduced to a minimum thanks to the use of high-quality materials such as HARDOX and WELDOX in combination with an optimized design. It keeps the life-cycle costs as low as possible. A modular design allows the use of standard parts in different grab models, which greatly simplifies the storage and results in faster response times in the production of new machines and after-sales management. Thanks to the intelligent design, it is also possible to match up high grab capacities with low dead weight.
Apart from the quality of PEINER grabs, SMAG is notable for its global service and dealer network that offers the customer a round-the-clock customer service. In addition to the assembly and start-up provided by its technicians, the company also offers training for the operating personnel. Thus SMAG’s customers get everything from one source.
A very important factor in the entrepreneurial thinking are the issues of environmental protection and sustainability. Environmental protection does not begin only when the grab is finished. Both at the work preparation stage and in the production process, care is taken to reduce the impact on the environment.
In addition, SMAG strives to keep the environmental impact associated with the use of grabs as small as possible. This is especially the case when it
comes to coal handling — an environmental friendly solution is very important. A number of features make it possible to minimize the loss of bulk materials and dust. In addition to dust covers, these include special sealing systems on the side and bottom lips. The use of steel sealing strips, rubber-sealed lips, overlapping bottom and side lips or special side toothing prevents bulk materials from trickling down. In contrast to the competitors, SMAG’s four- rope dual scoop grabs are also designed with just one, rather than two scoop pivot points. This results in such movement of scoops that ensures a synchronous closing and excludes any offset between scoops.