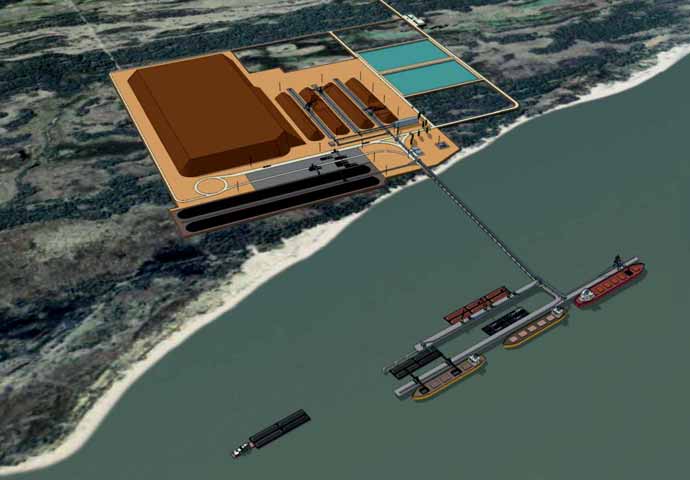
Engineering consultants are a vital link in the dry bulk commodity chain, offering expertise and practical solutions to the market. Their input varies from advising on the equipment needed to handle small quantities of bulk cargo, all the way through to the turnkey development of major ports.
Canada-based Ausenco is one of the major companies that offers engineering consultancy services. The company sets high global standards for leading edge engineering and project management services in the resources and energy sectors.
It is dedicated to delivering practical, fit-for-purpose solutions to complex problems that provide value to its clients, wherever they may be located. With 30 offices in 19 countries, it has the capability to deliver results for exciting projects in some of the world’s most remote areas.
Ausenco offers its clients a complete end-to-end solution through our areas of expertise which include energy, environment and sustainability, minerals processing, transportation systems, infrastructure, pipeline systems, operations and maintenance, and ports and terminals.
Ausenco is also committed to having a positive impact on the world around. It believes that, only by working together and with its clients, its communities and its environment can it achieve more to make a genuine impact on the world around.
A few of Ausenco’s most recent bulk-handling projects are detailed below.
GIBRALTAR DEVELOPMENT PLAN 3: GIBRALTAR MINES LTD.
Location: British Columbia, Canada
Business line: Minerals & Metals
Client: Gibraltar Mines Ltd
Timeframe: 2011–2013
Contract type: Create (EPCM)
Project Value: $237m
Ausenco provided engineering, procurement and construction management services for the third phase of the development and modernization of the Gibraltar copper-molybdenum mine, located in McLeese Lake, British Columbia, Canada. This project is known as the Gibraltar Development Plan 3 (GDP3) Project. The GDP3 project has increased the milling capacity at the
mine with minimal interruption to existing copper and molybdenum production. The project included the construction of a new stand-alone concentrator, which added an additional 30,000 tonnes per day to the processing capability.
The project incorporated additional primary grinding, secondary grinding, regrind, rougher flotation, cleaner flotation, concentrate filtration and tailings pumping capacity as well as various ancillary systems and upgrades.
A stand-alone molybdenum separation plant was also constructed to replace the existing molybdenum circuit; the new molybdenum plant has more than doubled the mine’s molybdenum metal production, to approximately 2.5 million pounds per year. These modifications and upgrades have enhanced Gibraltar’s operating flexibility and reliability and ensure that the mine continues to be an economic cornerstone for the region for years to come.
The GDP3 project increases the overall processing capacity to 85,000 tonnes/day with an annual copper production averaging 165 million pounds.
Achievements include:
- over 900,000 man hours without a lost-time incident;
- minimal interruption to existing production during plant shutdowns; and
- optimized existing site facilities and systems to provide cost-effective solutions.
Previous work performed by Ausenco for this project included an update to a 2008 Scoping Study for GDP3 incorporating process and layout optimizations made possible by the completion of the previous project phases.
ANTAMINA EPC PROJECT: ANTAMINA CONCENTRATE EXPORT TERMINAL
Location: Huarmey, Peru
Business line: Process Infrastructure, Ports, Marine and Offshore
Client: Bechtel International as agent for Compañia Minera Antamina
Timeframe: 1999–2002
Scope: Design and construction of concentrate loading port
Services: Planning, design, procurement, and construction
Project Value: $2.3 billion
Ausenco executed an EPC development of the Antamina concentrate export terminal at Huarmey, Peru.
The terminal is capable of exporting 1,800,000 tonnes of copper and zinc concentrates annually. Facilities include receiving tanks for the slurry, treatment facilities, storage shed for 150,000 tonnes of concentrate, conveyors from the filter plant to the storage building and from the storage building to the ships, berth for ships up to 50,000dwt and associated infrastructure.
Ausenco performed the project engineering and procurement and formed a joint venture (Sandwell SSK) with SSK Montajes e Instalaciones S.A.C., a Peruvian–Chilean contractor to carry out the construction.
The project was executed under a PI (performance incentive) contract where the owner and contractor share underruns and overruns. The contract was completed three months ahead of schedule with an associated budget underrun.
As well, Sandwell SSK achieved the best safety record of the 40 contractors on the $2.3 billion Antamina mine/port project, having exceeded 3.5 million hours of work with only one lost time injury.
The project was successfully constructed to World Bank environmental management standards. Ausenco received the Consulting Engineers of British Columbia,Award of Merit for this project in 2002.
DAMPIER PORT UPGRADE: EAST INTERCOURSE ISLAND ORE HANDLING OPERATIONS
Location: Business line:
Client: Timeframe: Services:
Location: Business line:
Client: Timeframe: Services: | Dampier Port, Western Australia Process Infrastructure, Mining and Bulk Terminals Hamersley Iron Pty. Limited 2003 Preliminary engineering, definitive cost estimates, construction planning, simulation modelling, construction |
At the time of this study, Hamersley Iron’s East Intercourse Island Terminal handled 35mt (million tonnes) per annum of lump and fine ore.
Train loads of 220 cars each carrying 105 tonnes, are bed blended by two travelling stackers. The ore is reclaimed by two bridge-type bucket wheel reclaimers at 8,000tph (tonnes per hour) and loaded into ships up to 350,000dwt. Fully laden ships up to 270,000dwt can depart at high tides.
The proposed new Yandicoogina Mine required handling a third type of ore and increased the port throughput to 65mt/year.
The definitive study by a Clough and Ausenco joint venture determined that upgrade of the East Intercourse Island Terminal is required to handle the third ore and increase shiploading efficiency.
The following upgrade construction was carefully planned to be completed in three phases, with minimal operational disruption: v two new 220,000 t piles for live storage of ‘Yandi’ ore;
- installation of one new bridge-type bucket wheel reclaimer;
- construction of a lay-by berth; and
- increased capacity of reclaimers and shiploader to 11,000tph.
Extensive simulation modelling was done to confirm the railroad deliveries, upgraded throughput capacity and vessel total time in port and loading performance. Detailed design and construction was completed by the Joint Venture.
CORUMBÁ EXPANSION PROJECT: FROM MINE TO TRANSSHIPMENT
Location: Business line: Client: Timeframe: Services: Scope: | Brazil, Paraguay and Uruguay Process Infrastructure, Mining and Bulk Terminals Rio Tinto Iron Ore
2007–2008 (12 months of a 3-year contract) Owner’s EPCM contractor for complete range of services from conceptual, pre-feasibility, and definitive engineering to procurement, contracting and construction management. Iron ore beneficiation, overland conveyor from mine to river port, river port facilities, river vessels and logistics, ocean port facilities, shuttle vessels, transshipment. |
Ausenco successfully completed definitive engineering and was awarded an EPCM contract for the Corumbá Expansion Project.
The contract consisted of iron ore beneficiation and transportation of 10mt/year from the mine near Corumbá, Brazil to Capesize ships anchored in the Río de la Plata, Uruguay.
Expansion plans to increase production to 20mt/year were included. The project included:
- mining equipment fleet;
- beneficiation plant, complete with water supply;
- a 30-km overland conveyor with complex curves, from mine to river port;
- barge loading port with drying capability;
- 19 tugs, 200 new barges, vessel maintenance facility, and logistics for transport of the product
- 2,500km down the Paraguay and Parana Rivers;
- barge unloading and shiploading port on the Rio Uruguay; and
- Panamax shuttle vessels and transshipment facility transferring ore to Capesize vessels anchored off Punta del Este.
The Corumbá Project Assets were sold to Vale in 2009. EPCM started but was not completed.
PUERTO NUEVO MARINE FACILITIES: COAL HANDLING EXPORT TERMINAL
Location: Business line: Client: Timeframe: Scope: | Cienaga, Magdalena, Colombia Process Infrastructure, Ports, Marine & Offshore Prodeco S.A. 2008–2010 Conceptual, basic, and detailed engineering |
Ausenco developed the concept engineering, basic engineering, and detailed engineering for the coal terminal marine facilities. Ausenco also developed the scope and managed the site-specific studies, which covered all geotechnical, navigational, and met-ocean aspects of the project. The marine facilities would become the largest coal loading terminal in Colombia, handling up to 180,000dwt bulk carriers. The marine facilities were comprised of a 1.3km-long trestle supporting two conveyors and an access roadway, a finger-pier supporting a travelling shiploader and capable of accommodating two Capesize carriers at any one time, a tug mooring facility, and a 9km-long dredged access channel to accommodate the full range of design vessels.
US company offers wide-ranging engineering consultancy services
Jenike & Johanson is a major provider of bulk material engineering services, including engineering consultancy.
The company delivers engineered solutions to achieve reliable powder and bulk solids flow based on proven theories and decades of project experience.
Bulk materials and their flow properties are at the core of all Jenike & Johanson’s work. Every one of its projects (7,500 to date) is truly unique. It offers its clients maximum flexibility in selecting services required to meet their bulk material handling needs. It does not follow the ‘one size fits all’ concept — which can be a dangerous pitfall in engineering. Decisions made during the feasibility and engineering stages of a project are critically important for its success. If your bulk solids systems are not engineered from the outset to handle the unique characteristics of your materials, process start-up time can be significantly delayed and design capacity may never be reached.
The company offers a wide range of services that effectively support various stages of a typical engineering project.
JENIKE & JOHANSON’S CORE SERVICES
- site visit: review process and equipment, collect critical design data;
- bulk material testing: characterize bulk material flow, conveying, or segregation behaviours;
- conceptual & functional engineering: design of silos, hoppers, feeders, chutes, stockpiles for reliable flow;
- physical & analytical modelling: model a unique process or develop/run a computational model; and
- structural & mechanical engineering: engineer key details for equipment for construction, fabrication.
ADDITIONAL SERVICES
Jenike & Johanson can also provide: review of your material handling system or
- peer reviews: process design from solids flow basis; courses on theory/practice of effective
- education & training: bulk material handling and conveying; legal services involving
- expert witness & litigation support: liability, equipment failures, etc.; equipment to measure powder flow
- bulk material testers: properties and segregation potential; and
- equipment: customized material handling equipment that
CASE STUDIES
Jenike & Johanson has given Dry Cargo International details of some of its recent case studies that relate to the dry bulk market.
1.Vessel analysis: ensuring metal concentrate cargo stability INDUSTRIES: Powdered Metals, Mining & Minerals
The need
The ‘Code for Safe Practice for Solid Bulk Cargoes’ provides rules of safe practice for the shipment of bulk cargoes by ship. One of the rules is to ensure the materials in the holds have sufficient time to settle and are stable before proceeding out of port. Bulk cargo carriers have been known to list and even sink as a result of unstable cargo — especially in inclement weather.
The metal concentrate producer understood the risks and was aware of the concern. However the codes give no specific guidelines on how long to wait to ensure a fine, dry concentrate has properly settled and no longer presents a risk of being unstable. Waiting too long presents costly time lost at the port so there is substantial pressure to depart as quickly as possible. Therefore a thorough basis for determining a sufficient wait period was required.
NEEDS ADDRESSED: Solve or prevent poor flow, address process non- uniformity
BULK MATERIAL HANDLED: Metal concentrate
EQUIPMENT: Storage
The solution
Jenike & Johanson was commissioned to study the problem and provide a reliable method for setting the wait period. Its approach was to measure the relevant flow properties of the metal concentrate. It then used its proprietary SETTLE software to predict how long the vessel must stay in the port before sailing to ensure the cargo is stable. This required an understanding of hold sizes, filling behaviour, and the flow properties of the material. For their ships and filling approach, it recommended that the vessel remain in port for at least 24 hours after the last hold was filled.
The result According to the client, there have been no reports of cargo shifts since adopting Jenike & Johanson’s recommendations. The project has eliminated the risk and provided an engineered approach for the required wait period before setting sail.
2.‘CSL Innovator’ self-unloading ship operates efficiently
Canada Steamship Lines — Toronto, Canada
INDUSTRIES: Mining & Minerals, Cement MAIN BULK SOLIDS: Alumina, Cement, Coal, Iron Ore, Ore, Potash, Salt
The need Built for world-wide ocean trade by Canada Steamship Lines (CSL), the CSL Innovator is a Panamax-class self-unloading vessel.
CSL’s new vessel had to be capable of transporting and discharging a wide range of materials. Typical free-flowing products include grain, iron ore pellets, and aggregates. Cohesive products include wet ores, concentrates, and cohesive coals. Fine, dry, dusty products include alumina and possibly cement. Products that cake include salt, potash, and sugar. Many products are single sized, but others, like gypsum, can contain large, slabby lumps.
NEED ADDRESSED: Solve or prevent poor flow BULK MATERIAL HANDLED: Cement, iron ore pellets, aggregates, wet ores, concentrates, alumina, salt, potash, coal EQUIPMENT: Storage, gate
The solution Personnel in Jenike & Johanson’s office in Toronto, Canada, worked closely with CSL designing viable hopper and gate configurations.
Flow property results obtained for a very cohesive iron ore concentrate were used as the design basis material. Jenike & Johanson considered many gate design concepts, constructed working models and performed flow pattern tests. Eventually, it developed a new gate of the ‘basket’ or ‘swing’ gate type in conjunction with Consilium CMH Marine AB.
The result The new ship, aptly named the CSL Innovator, has been in continuous service since September 1988. To date, the performance of the new hold configuration and gate design has been exceptionally good and has far exceeded industry expectations.
3. Fixing chute plugging problems at petcoke shipping terminal INDUSTRIES: Mining & Minerals, Energy & Power MAIN BULK SOLIDS: Coke
The need A major US conglomerate ships petroleum coke throughout the Pacific Rim. Delays in the loading operation created by flow stoppages can disrupt schedules, leading to higher shipping costs.
The facility encountered severe plugging problems with the chutes that feeds into their main storage silos. These stoppages occurred in several chutes at conveyor transfer points. The water used in cleanups ended up in the silos, which increased the moisture content of the stored coke and thus created additional clean-up problems downstream.
NEEDS ADDRESSED: Solve or prevent poor flow, address process non- uniformity BULK MATERIAL HANDLED: Petroleum coke EQUIPMENT: Conveyor
The solution Flow testing on various samples of petroleum coke allowed J&J engineers to evaluate the cause of chute plugging. A thorough review of the transfer chute system was performed. It was determined that the chute design needed significant modifications to maintain reliable stream flow.
A new chute geometry was developed, including a diverter (flop gate) feature. J&J was also contracted to develop mechanical fabrication drawings and supply of the new chute, which has several key features for maintaining sticky coal flow. Abrasive wear testing was also done by J&J to evaluate chute liner life.
The result The petroleum coke handling system has been in operation for over three years with minimal downtime for maintenance.
ABOUT JENIKE & JOHANSON, INC.
Jenike & Johanson is a major global provider of powder and bulk solids handling, processing, and storage technology. Over the past 55 years, it has tested over 10,000 unique powders and bulk solids and worked on more than 7,500 projects, giving its team the broadest real-world and in-depth experience in the industry to address a wide variety of bulk material handling and engineering needs.