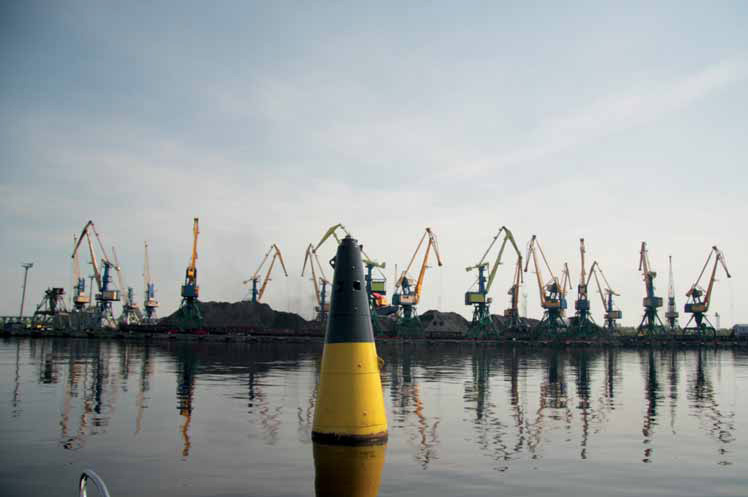
The large number of countries surrounding the Baltic Sea generate a variety of dry bulk traffic, from more traditional coal in the Baltic States and Poland, to a more diverse range at ports in Sweden and Denmark.
The Latvian Port of Riga handled 21.63mt (million tonnes) of dry bulk in 2012, which was 8.3% more than the previous year. Much of the increase was down to coal volumes, which rose by 10.4% to 14.9mt. In addition, grain products and some ores also increased.
The port’s importance in this trade cannot be understated, since it was the largest dry bulk port of those in the Eastern part of the Baltic Sea, handling 24% of region’s dry bulk volume.
A port spokesperson noted that no huge increases are expected for 2013, with the forecast for similar throughput as last year.
Overall, Riga could handle up to 26mt per year with its current infrastructure, although in a few years’ time capacity will have reached 32mt. The most advanced project is that of Krievu Sala, which is currently under construction. The aim is to relocate terminals away from the city centre and thus provide more efficient cargo handling. Once fully operational, its capacity will be in the region of 17–22mt.
Significantly, of the 32 stevedoring companies working in Riga Freeport, dry bulk is handled in 19 terminals, with a variety of different handling equipment to found, depending on what commodities are handled. In total, there are more than 110 different cranes units, with new equipment being added all the time.
Approximately, 75–80% of total port’s cargo is handled by train and approximately 85% of dry bulk traffic either arrives or leaves by rail, with all transit cargo trusted to the railways for onward movement. Eleven dry bulk terminals have direct rail access, linking into the national and international network.
At present, the main dry bulk commodities flowing through the port are coal, fertilizer, woodchip, wood pellets, metals, scrap and ferro-alloys. Coal, at 14.9mt, was the most significant commodity in 2012, followed by fertilizer (1.415mt), grain (686,900 tonnes) and woodchip (1.053mt).
The maximum draught at the main dry bulk berth is 14.7m, which accommodated its largest ever vessel, in 2012, when the 118,590dwt UBC ONSAN called with a cargo of 111,700 tonnes of coal.
As for storage, there are 333,000m2 of covered warehousing, 1,619,000m2 of open stockpiles and 250,000m3 of silos.
Other than handling and storage, a variety of other added value services are available, including coal magnetic separation and purification, cargo sorting, ore packing, grain blending- cooling, and fumigation.
In 2012, the Lithuanian Port of Klaipeda registered a 3.2% decline in overall dry bulk traffic in handling a total of 14.063mt. Some commodities did better than others.Agricultural products, for example, grew by 71.8% to 2.747mt, with grains, in particular doing rather well. At present, the covered storage capacity of dry bulk cargo at the Port of Klaipeda Port is about one million tonnes, while handling capacities for fertilizer and agricultural products have reached 14mt and 5mt respectively.
A port spokesperson points out that storage capacity of the above- mentioned cargoes has been increasing steadily, with stevedoring companies in the port having built new facilities so that the ongoing demand increases for agricultural products and fertilizer can be accommodated.
However, fertilizer traffic on the year was down from a 2011 record high of 9.564mt to 7.683mt, a drop of nearly 20%, which is mainly down to decreased demand. Nevertheless, the end-of-year figures do not accurately reflect what was really going on in this sector. While there was reduced demand, most sales contracts were only signed at the beginning of the second quarter of 2012, after which throughput levels effectively returned to higher levels.
The growth in fertilizer traffic since 1991 has been little short of breathtaking. Starting from a base of just 140,000 tonnes in that year, the upward trend has continued, with gains in recent years being vertiginous.
The Port of Klaipeda also has five other main bulk commodities that it handles regularly: minerals and aggregates, which amounted to 1.559mt in 2012, up 14.6%; ore (784,000 tonnes, up 25%); scrap (282,000 tonnes, down 31%); sugar (291,000 tonnes, down 29%); and peat (351,000 tonnes, up 34%).
“In 2013, we expect to handle about 15mt of dry bulk, up 4% on last year,” says a spokesperson.
Given the increasing volumes of dry bulk handled over the last ten years, various infrastructure development projects have been implemented in Klaipeda Port to allow larger vessels to be accommodated, with the maximum admissible draught now being 13.4m. In addition, the port’s various stevedoring companies have also invested in warehousing, handling equipment and processing technology. Once all current projects havebeenimplemented,capacity,whichstandsat23mt,will have been boosted even further.
The port currently has around 80 units of large-size cargo handling equipment at its disposal, ranging from portal cranes to transporters and port trucks, although the actual number increases year-on-year. These are owned and operated by the port’s six dry bulk terminals, belonging to the following
stevedoring companies: KLASCO, Bega, Biriu Kroviniu Terminalas, Malku jlankos Terminalas,Vakaru Krova and Mabre LPC.
“Loading capacities are currently anything up to 1,500tph [tonnes per hour], while unloading we can achieve around 300–400tph,” noted the spokesperson.
All handling companies at Klaipeda Port enjoy broad gauge rail connections with neighbouring countries to the east. Approximately 75% of all cargo handled by the port is transported by rail, while the port authority calculates that up to 95% of dry bulk cargoes arrive or leave by train.
Vessel sizes for transporting dry bulk average in the region of 25,000–30,000dwt, although the largest bulk carrier to access the port to date was of 96,000dwt
“The current 13.4m draught is our main limiting factor at the moment, although ongoing dredging will eventually deepen this to enable larger vessels to call,” says the spokesperson.
With Klaipeda equipped with a range of covered warehouses, silos, bunkers and open stockpiles, plans do exist among the stevedoring companies to offer value added services for dry bulk commodities in the near future.
Sea Port of Saint-Petersburg is the largest operator in the Greater Port of Saint-Petersburg, handling a variety of dry bulk commodities, in addition to containers, ro-ro, reefer vessels and finished vehicles.
In 2012, volumes of dry bulk cargo doubled to 1.8mt, which the company puts down to optimizing the technology involved in product handling and modernizing IT and logistics systems linking the port with its customers.
“We also introduced a new marketing strategy for the company, which allowed us to attract additional cargo flows,” says managing director, Pavel Oleynik.. “We are forecasting that this positive trend in dry bulk volumes will continue this year, although everything depends on the situation of the market. Quite how much that growth will be also relies on what demand there is for domestic and overseas products.”
Asked about Saint-Petersburg’s capacity for handling dry bulk, Oleynik points out that this is dependent on several factors, for example, berths being occupied by other cargo, the volumes involved and how long it takes to handle them, as well as on the number of vessels requiring stevedoring services at any one time.
“Sea Port of Saint-Petersburg is an universal operator and if necessary we can efficiently change technological processes, using all and any available capacities to handle dry bulk in whatever volumes our customers need.”
Within the port, there are grabs, gantry cranes and bucket loaders available to handle dry bulk. One interesting innovation is the deployment of a 300-tonne capacity floating crane (Bogatyr), which is used to transfer inbound minerals directly from railway wagons into a docked vessel. On the landside, a 150-tonne Liebherr mobile crane also sees significant deployment on dry bulk shipments.
Mineral fertilizer traffic is concentrated in a dedicated facility capable of handling up to one million tonnes per year.
“In respect of dry bulk, we are planning to expand our production base by putting into operation both new hi-tech equipment and new infrastructure, specifically to meet the needs of our partners,” says Oleynik.
Sea Port of Saint-Petersburg also has well-developed railway infrastructure. Nowadays, all dry bulk cargo flow is transported by rail, which involves close co-operation between the railway company and the port. In order to ensure the delivery and withdrawal of the required number of rail wagons, port-rail infrastructure has been specifically designed, allowing wagons to discharge directly into hoppers. Co-operation between port and railways has boosted productivity in this area considerably.
At present, the company mainly handles mineral fertilizer, ore, grain and coke at its own berths. However, because it is permitted to undertake activities throughout the port, it can, potentially, be asked to handle a wide spectrum of cargoes.
“The majority of commodities that we handle don’t require on-dock storage; they are moved directly from rail to a waiting vessel. This helps customers avoid losing time and avoids incurring additional expenses,” says Oleynik.
In 2012, of the 27mt of freight handled by the Polish Port of Gdansk, dry bulk accounted for 7.3mt, or just over a quarter. Main commodities handled were coal and coke, aggregates, artificial fertilizer and cereals. Although overall port tonnage was lower in 2011 — 25.3mt — the figure for dry bulk — 7.6mt — was actually higher. The difference is the result of slightly depressed demand for road building materials and fewer cereals, although coal did slightly better.
“For this year, the forecast is for a continuing decline in dry bulk traffic, essentially because of suppressed demand for road building materials. However, this pessimism was not borne out in January, with traffic in coal extremely buoyant, as well as strong demand for both cereals and chemical fertilizer,” says a port spokesperson.
In terms of capacity in the inner port, around 15mt of import and export dry bulk can be handled. However, only export consignments are shipped from the deep water berths in the outer port, with up to 50,000 tonnes being loaded every day. Additional capacity is being provided by the Sea-Invest Group, which is building a new, dedicated facility, the Bulk Cargo Terminal, which will be able to handle 5mt of coal annually for both import and export per year.
The existing deepwater Coal Terminal has an entirely automated loading system, with a conveyor belt network feeding several ship loaders. Stevedores managing the port’s cereals transshipment operations also have similar equipment. Other bulk quays use standard port cranes, where productivity can vary depending on the type of material being handled.
“We can load up to 50,000 tonnes of coal an day using the ship loaders, while using more traditional methods in other terminals, rates are around 10,000 per day,” says the spokesperson.
In July of this year, operations are due to commence at the deep water Gdansk Bulk Terminal, which will be equipped with a 60-ton Liebherr LPS 600 crane and an extensive system of RBL-PRITIP belt conveyors. It will also have the largest ship loader of any Polish port, which is being supplied by a Polish firm from Kluczbork.
Given the nature of the commodities handled at Gdansk, it is unsurprising that the vast majority come to the port by rail, but only building materials are moved in any quantity by road.
“Draught is not a problem at Gdansk,” insists the spokesperson. “We are an ice-free port all year round, and in the outer part of port we can offer a water depth of up to 15.5 metres, which means we can accommodate the largest ships that come to the Baltic. In contrast, movements in the inner port are limited to vessels drawing 10.5 metres of water, which is usually means not more than 50,000dwt vessels.”
In terms of storage, building materials are stacked and processed in specialist areas, while coal and coke are kept in dedicated stockpile areas, where some additional processing does take place. The port authority also provides warehousing for cereals and fertilizer, but time to time happened that transshipment tends to be direct between vessel and truck, or between truck and vessel, without the need for intermediate storage. The cross border Copenhagen–Malmo Port has yet to release figures regarding its dry bulk traffic in 2012, but in 2011 it handled a combined 3.4mt of dry bulk, which was 0.7mt more than in 2010.
Bulk manager Perry Emchen, notes that there is a variety of terminals split between the two ports. In Sweden, there is Swede Harbour, which is the largest bulk port in Western Sweden, able to handle fully loaded Panamax bulk carriers. It covers an area of 100,000m2, with 16,000m2 of covered storage, and is accessed via a 200m quay.
Also in Sweden, there is the Södra Bulk Terminal, which has a 330m quay that is normally used by much smaller vessels.
“In 2012, we constructed a new, 250m-long quay for dedicated cement handling, while Cementa built a new 90m-high silo for the exclusive distribution of cement,” says Emchen.
In Copenhagen, there are smaller facilities. Amagerværket is a dedicated terminal for the local power plant, which imports both coal and bio-fuel. In addition, Margreteholmen quay handles minor building materials, while Nordhavnen is a similar facility catering for salt, sea-dredged materials, broken stones, and other aggregates.
“We also have our largest dry bulk terminal in Denmark, which is at Prøvestenen. This used to cover an area of 180,000m2 and be served by three quays, totalling 554 metres.
However, in 2012, we effectively doubled the operating area, by adding a further 180,000m2 and an extra 650m of quay. Today, therefore,Prøvestenenis360,000m2 inextent,with1,204of berthing line divided among five different quays.
In Denmark, all materials handling equipment is owned by the terminal operators, not by the port. In Malmö, however, the port authority has three rail-mounted 20-tonne cranes positioned in Swede Harbour. In addition, the port owns a 64-tonne mobile crane, two Multidockers and one Fuchs 360 material handler. Significantly, one of the Multidockers was bought in 2012, while a large Volvo 350F front loader was bought in September 2012, it being the largest of its kind that Volvo manufactures.
“Our decision to go ahead with the expansion of Prøvestenen, in Denmark, is naturally predicated on our belief that more cargo will be handled there,” says Emchen.
The main commodities handled across the various quays of the joint port include scrap, raw sugar, stone, sand and gravel, glass, limestone and cement. Asked about productivity rates, Emchen says it is difficult to generalize, since these very much depend on the type of cargo, vessel size and volume. Rates, overall, are competitive with other regional competitors.
With pressure growing on ports to switch as much traffic as possible from road to rail, Emchen notes that, in Malmö, all dry bulk terminals are linked by rail, while the cement facility has a rail track that passes directly into the silo. Stena Environment also operates several trains conveying loads of scrap and iron products each week.
“We are handling a lot of transshipment cargo,” stresses Emchen.
In terms of vessel size, at Prøvestenen,Yeoman and Stema vessels of around 97,000dwt operate, while Swede Harbour handles fully loaded Panamax bulk carriers.
“As for adding value, Stena Environment has a hub operation at the port, importing via road, rail or coastal vessels, thereafter separating and shredding consignments, then shipping them out on fully loaded Panamax vessels. We also have key warehousing facilities at Swede Harbour for raw sugar,” says Emchen.
The Swedish port of Helsingborg reported handling 270,000 tonnes of dry bulk traffic in 2012, consisting of grain, soyameal, salt and limestone, compared to just 156,000 tonnes the previous year. In addition, it has a buoyant trade in wood pellets, which amounted to 170,000 tonnes in 2011 and 155,000 tonnes in 2012, although wood pellets are forecast to decrease by about 30% in 2013, as a new heating plant built for Öresundskraft will burn rubbish rather than wood pellets.
Öresundskraft is one of the port’s largest customers. It uses a single grab crane to unload inbound pellets, which is more than sufficient for a business that generates 12–15 vessel calls each year.
The other big customer is the Swedish Farmers’ Association, which operates its own, dedicated facility within the port, which has the largest grain storage capacity in Sweden. It deploys pneumatic equipment to handle a two-way flow of traffic, with the port authority only responsible for dropping bobcats in the hold to help clear consignment remnants.
All dry bulk into and out of the port moves by road, although the wood pellets are actually burnt at a facility within the port. Previously, coal was used to generate the same heating, but was made illegal some six years ago.
Draught at the port varies from 14m and 7.5m, divided across five different quays, with wooden pellets handled at a 180m long quay, with alongside draught of 13m.
“Traffic is essentially captive to Helsingborg, given substantial investment in facilities by our two most important customers,” notes a port spokesperson, who adds that the port authority is trying to replace the rapidly decreasing number of wood pellet consignments with other dry bulk, with road salt one target.
Barry Cross