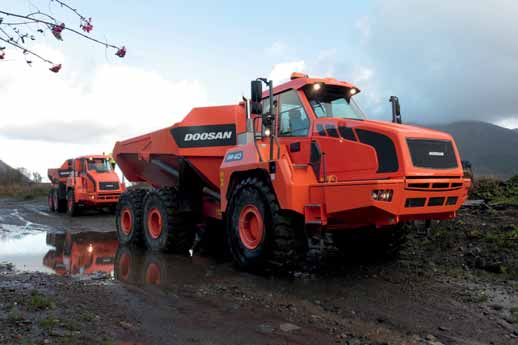
Doosan Construction Equipment has launched new versions of the company’s DA30 and DA40 articulated dump trucks (ADTs) meeting Stage IV/Tier 4 Final engine emission regulations. The design of the new DA30 and DA40 ADTs goes far beyond just meeting the latest emission standards and incorporates many additional features and product improvements to establish a new benchmark in load carrying performance, fuel efficiency, enhanced controllability and high operator comfort, together with improved reliability, durability and reduced maintenance and servicing costs.
Like all Doosan ADTs, the new DA30 and DA40 models feature an articulation hinge positioned behind the turning ring to provide equal weight distribution to the front axle even during maximum steer articulation. This together with a free-swinging rear tandem bogie ensures equal distribution of weight to each wheel and guarantees permanent six-wheel contact and drive for equal power distribution and excellent performance on difficult terrain. Collectively, the forward turning point, the unique tandem bogie and the sloping rear frame results in ‘best in class’ rough and soft terrain capabilities and avoids the need for electronic aids such as traction control.
‘BEST-IN-CLASS’ FUEL CONSUMPTION
The ‘best-in-class’ fuel consumption of the new Doosan ADTs is down to a combination of features including new Scania Selective Catalytic Reduction (SCR) and Exhaust Gas Recirculation (ECR) diesel engines and a new ZF EP transmission, improving the transfer of power from the engine to the wheels for outstanding traction. When this is coupled with the enhanced rear differential system which reduces engine rpm and further increases machine durability, customers are ensured of an improved cost per tonne carried with the new Doosan ADT range.
The new Doosan DA30 and DA40 ADTs are powered by Scania DC9 276 kW (370 HP) and DC13 368 kW (493 HP) diesel engines, respectively, meeting the Stage IV/Tier 4 Final emission regulations through the use of both SCR and EGR technologies, with an electronic engine brake system, one of four brake systems on the trucks. The new Stage IV/Tier 4 Final ADTs do not need a diesel particle filter (DPF) to meet the emission regulations.
Specifically designed by ZF for use on ADTs, the new ZF EP countershaft transmission provides eight forward speeds [with a top speed of 55 km/h (34 mph)] and four reverse speeds. In the DA30 and DA40 models, the front differential is mounted directly onto the transmission, so there is no driveline that needs greasing and reducing the overall length of the machine for better weight distribution and a tighter turning circle. With smaller equal gear steps between gears, and a higher overall gear spread (eight forward gears), the transmission works optimally with the engine for better fuel efficiency.
The DA30 and DA40 Stage IV/Tier 4 Final ADTs have been tested with a new tracking and management system to be launched in the near future by Doosan and have been shown to deliver outstanding fuel consumption figures to provide an excellent cost per tonne transported. This is an improvement on the already excellent figures for the Stage IIIB/T4i machines in operation around the world, which are claimed to have outperformed other machines on the market by up to 15% and, in some cases, have carried up to 10% more load.
For the DA40 model, for example, the body capacity has been increased to 24.4m3 and the payload has been boosted to 40 metric tonne without tailgate, an increase of more than 15% over the payload of the previous MT41 model from Doosan. In both the new DA30 and DA40 models, the higher speeds and payloads contribute to reduced cost per tonne rates, allowing customers to increase profits from their mining, quarrying or earthmoving operations.
In response to requests from ADT users, Doosan will be supporting the high performance of the DA30 and DA40 Stage IV/Tier 4 Final machines with a new (optional) tracking system designed specifically for use on Doosan ADTs, providing full information on payloads, fuel consumption and cycle times. In addition, the company recognizes that fuel efficiency is very much dependent on the skill and experience of the operators and for this reason, Doosan has a team of trained demonstrators available to visit customers’ sites in Europe to train up drivers in the most fuel efficient way to operate units.
Other new features on the Stage IV/Tier 4 Final machines include an upgraded display with an integrated gradient meter that shows the gradient of the dump truck’s trailer, helping to ensure that drivers can safely dump their loads in all conditions. There have also been changes to the displays for the time and outside temperature.
Together with a new grill with larger cooling vents, the new DA30 and DA40 ADTs both feature increased cooling capacities, allowing the trucks to be operated in the most punishing outside temperatures, as high as 60 °C and above.
HIGH OPERATOR COMFORT
The ROPS/FOPS cab has been designed with simplicity of use and operator comfort in mind. One of the most spacious on the market, it has ample room for a trainer seat, cool box and cup holder. With a noise level of only 72 dBA, it is also one of the quietest cabs on the market. In addition, the easy-to-use power steering with orbitrol valve amplifies oil flow to both steering cylinders, reducing operator fatigue by making steering light, reactive and easy.
For reduced maintenance, as well as better stability, the turning ring mounted on the front part of the truck also results in less wear on tyres and driveline. The unique driveline concept, with only two differentials, also limits component wear. Other aspects that contribute to the reduced cost of ownership include just three wear parts on the rear frame — one tandem bearing on each side of the frame and one articulation point bearing.
The new DA30 and DA40 ADTs also have only one rear differential compared to two on all other comparable machines on the market and have only one hydraulic pump for steering, hoist and servo pressure functionality, compared to the two and sometimes three hydraulic pumps used on other trucks on the market.
Installed in the factory as standard equipment, the auto lube system is managed by the machines’ VCU so that it pumps grease to all sections of the trucks only when required. A new ‘one-key solution’ gives operators access to all compartments of their machine via a single key.