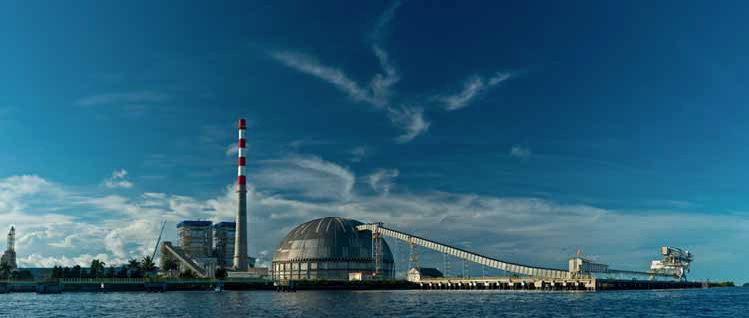
In 2012, world urea supply surpassed 161mt (million tonnes), while the volume of worldwide urea production is projected to exceed 202mt in 2016, writes Melanie Saxton of Geometrica. This, according to Merchant Research Consulting, indicates the ongoing demand for nitrogen and fertilizer globally.
As industries seek efficient and eco-friendly ways to cover organic or synthetic stockpiles (which may include nitrogen, phosphorus, potassium, sulphur, manure and other sensitive raw materials), they must address the usual culprits: seepage, bogging, exposure to moisture, overflow, and contamination of groundwater, estuaries and oceans. ‘Green’ storage initiatives must protect ecosystems, landscapes, crops and communities. One of the most common ways to store raw fertilizer materials is by stacking it in long prismatic piles, all the while defying the corrosive nature of the raw material, itself. Finding long span storage solutions can be a challenge, as elements relentlessly attack the internal structures of a facility.
Some fertilizer and sulphur suppliers face another obstacle. The seaside environments in which they operate add an external complication — a very real ‘double threat’ from exposure to caustic bulk combined with the corrosive nature of salt water. This is a huge concern for port side urea warehouses, including Grupo CICE in Veracruz, Mexico.
DEFYING CORROSION ALONG THE GULF OF MEXICO
When exposed to humidity, urea attacks both aluminium and galvanized steel. But industries along the coast of the Gulf of Mexico also face production hurdles in one of the most brutal saltwater atmospheres anywhere on earth. Grupo CICE, a diversified logistics and transportation company, needed to store up to 15,000 tonnes of urea awaiting transport and contacted Geometrica to design a building that would withstand challenging conditions at the Port of Veracruz.
Geometrica delivered a multi-faceted warehouse solution. Knowing that industrial urea storage and saltwater exposure combine to torture metal, Geometrica suggested a Freedome® barrel vault with a revolutionary longitudinal and vertical span. UsingatrademarkedFreedome® system,Geometrica‘putalid’ on Grupo CICE’s highly corrosive longitudinal stockpile in the form of completely prefabricated, self-scaffolding structure that aggressively protects interior and exterior environments.
Corrosion-resistant technology includes a variety of options, such as waterproof internal FRP (fibreglass reinforced plastic) cladding with special coatings for enclosing highly corrosive materials. Cladding may be made of steel, aluminium, fibreglass, fibre-reinforced plastic, polycarbonate or a combination of all. For severe exterior conditions, structural tubes of galvanized steel or aluminium are specifically manufactured with a finish of highly resistant thermoset epoxy or polyester coatings, with cross sections suited to project conditions. And because internal cladding provides a sealed, gap-free surface, it minimizes potential hazards.
Generally, no welding or special tools are required. Structures can be assembled in a short amount of time by local unskilled personnel who are trained on site, which has the additional benefit of bolstering regional economies.
Geometrica has built many domes for combustible and corrosive materials, including a range of fertilizers, urea or ammonia. These applications come in every stockpile shape — ring, conical, longitudinal and free-form. In the case of Grupo CICE, the lightweight skeleton was built of high-strength aluminium alloy (which was left exposed). Half-arches were assembled on the ground and lifted onto place with two light cranes. The application required a minimum of space and equipment and permitted other subcontractors to work side-by- side on site. The structure was protected by applying FRP cladding to its underside.
Defying terrain, wind, weather and maritime conditions, Geometrica delivered a unique building of 52m internal clearance width, 18m clear height at the centre, and 120m length that provided maximized useable space. The entire construction process took four months, and CICE’s general manager on site, Cesar Zamora, said of Geometrica,“Excellent quality, service, and products. 100% recommendable.”
CUSTOMIZED CONTAINMENT IN INDONESIA
When a fertilizer processing facility owns and operates its own port, its stockpiles must be covered under difficult circumstances. PT Pupuk Kalimantan Timur (Pupuk-Kaltim), Indonesia’s largest fertilizer producer, had very specific logistical and environmental needs. As part of its ‘green’ initiative, it chose to use only clean-coal technologies, including a circulating fluidized-bed boiler, a Geometrica coal-storage dome and a continuous barge unloader.
Fortunately, Geometrica was experienced in these technologies from previous applications at the JEA Northside power plant in Jacksonville, Florida. “This project was very similar to domed bulk-storage facilities we have built worldwide,” said Jorge Parada, Geometrica’s site consultant. “Our galvanized-steel dome technology has proved itself in many environments and applications. This one, along the coast of a tropical rainforest, is another great example.” The galvanized-steel dome structure is clad with aluminium sheeting, combining the strength of steel with the corrosion resistance of aluminium. It also meets National Fire Protection Association guidelines for control of confined dust. As for Indonesia’s typhoon-force conditions, Geometrica was also experienced in the design and installation of industrial storage solutions in a variety of wind loads. Pupuk Kaltim’s circular dome was to be supported by a 10-metre-high, reinforced-concrete, perimeter-ring wall and would cover 40,000 tonnes of coal, plus a coal stacker and a portal reclaimer. It would ultimately span 81m.
Geometrica labelled, pre-sorted, and packaged the components in the order required for assembly. Crates of these materials were then loaded into containers for shipment to the Port of Jakarta, Indonesia. From there, IKPT transported the containers to the job site in Tanjung Harapan. “Experienced Geometrica technical-support staff came to Bontang to train our local labourers and supervise their work,” said Ahmad Mardiani, Pupuk-Kaltim construction manager. “Because of their contributions and co-operation, our local labourers were successful and proceeded without delays.”
THE RUWAIS SULPHUR DOME IN ABU DHABI
Geometrica designed an immense sulphur dome spanning 134m in Abu Dhabi, the capital and the second most populated city in the United Arab Emirates. The area is home to a sulphur handling terminal for the oil & gas industry. Sulphur is a raw material with specific storage requirements.
It is known to explode on contact with oxidizing agents and can react violently when exposed to finely divided metals, alkalis, and mineral acids. It also corrodes damp steel and attacks the storage structure’s metallic components. As with any hazardous stockpile, Geometrica designed a well-ventilated circular structure with a framework that would defy corrosion and minimize safety hazards. The Ruwais dome was engineered for flexibility and customized to suit the project’s specific storage requirements, handling equipment, site requirements and design preferences.
In any application, conveyor openings may be placed at the apex or side as a practical solution for natural ventilation.
Penthouse enclosures can be used to protect top loading conveyors, while flashing can be used for side penetrations. When necessary, domes can be engineered to partially support the conveyor, or allow independent conveyor movement. Access openings for equipment, vehicles and personnel can be designed in any shape or size. Customized doors, frames, canopies and hatches are available for all openings. Translucent panels contribute natural lighting, energy cost savings and additional beauty to Geometrica’s structures. The company’s galvanized steel ladders are built for safety, using non-slip threads. Galvanized steel walkways are provided with OSHA-approved guide rails and nonslip grating. Ladders and walkways provide access to electrical systems, ventilation systems, mechanical penthouses, conveyors, galleries and safety exits.
STORAGE ENGINEERING AND ASSEMBLY
Whether facing typhoon-force wind loads or other brutal weather conditions, Geometrica’s space-frame applications take advantage of three-dimensional structural behaviour to achieve the highest calibre of strength.
Geometrica buildings can span up to a remarkable 300m (1,000ft). They provide unique solutions for manufacturers requiring a structure be built over existing stockpiles — with no downtime. Three different assembly methods are utilized, determined by the specific requirements of the site and application:
With a ‘Lift in Place’ method, sections are assembled at ground level and lifted into place with a standard construction crane. As sections are added, the dome takes shape. Cladding can be installed after the shell is assembled, or on individual sections as they’re put in place. This method works well when the dome is to cover a high structure and for longitudinal structures, as in the case of the Grupo Cice facility. Most assembly can be done at ground level, and other subcontractors can work simultaneously inside the storage dome.
‘Perimeter Self-Supporting’ is another technique in which workers assemble a ring at a time, from the perimeter ring beam up. Successive sections are attached until closure at the apex. Self-supporting is an extremely practical assembly method, with no ground level equipment to interfere with plant operations. Structures can be built while the pile is in use, or while adjacent construction is going on, providing great savings in time and cost.
The ‘Center-Out’ option is constructed around a tower, and the dome is assembled one ring at a time. As each progressively larger concentric ring is formed, the tower lifts the structure to accommodate its new height. The dome grows outward and upward, gradually forming the shell.