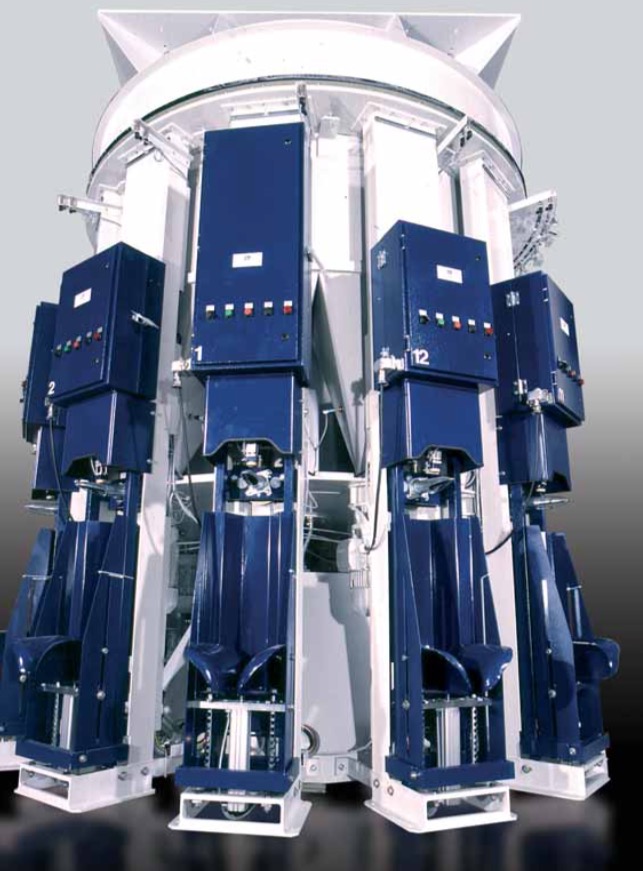
NEW TECHNOLOGIES ENABLE ‘COMPLETE PLANT’ CAPABILITY
Claudius Peters has unveiled its new PACPAL range of packing technologies which provide a state-of-the-art packing capability for any plant, and which also enable the company to offer a complete end-to-end ‘new plant’ capability (see graphic, above). The high-performance modular PACPAL range comprises a Roto Fill, Bag Applicator, Inline Fill, Bag Loaders, Big Bag Fill and a choice of different palletizer units capable of layering up to 5,000 bags per hour, depending on bag and unit type. These products, designed to adapt to any conceivable plant configuration, combine low-maintenance and optimized energy consumption with high availability and easy, interactive operation, utilizing the most innovative design technology available today.
Claudius Peters sales and technology Director Stephan Oehme said:“As well as promising significant new productivity benefits for our customers, these new technologies allow us to offer complete plant solutions, further underlining Claudius Peters’ reputation as the world leader in its industry.”
REPLACEMENT ETA COOLER CONTINUES TO DELIVER BENEFITS FOR LA UNION IN PHILIPPINES
A decision in 2011 to install a new Claudius Peters ETA Cooler in Holcim’s 20 year-old plant at La Union in Northwest Philippines, continues to deliver multiple efficiency benefits for the plant today.
Cooler-related kiln stops created by the plant’s existing cooler had created a bottleneck resulting in around ten days per year of cooler-related stops. Instead of reconditioning the cooler, the decision was taken to install a new Claudius Peters ETA Cooler.
This delivered immediate improvement in all operational parameters, including reduced fuel costs, increased cooler availability and a significant reduction in maintenance costs.
Commenting on the benefits that this decision was still bringing to the La Union plant, Andre Vos, Claudius Peters sales manager said:“This installation is an ongoing success story at Holcim’s plant at La Union. The combination of a simple aeration concept, controlled side aeration, independent lane movement and high clinker bed make the ETA Cooler’s process unbeatable. Low-cost modification of an old cooler may seem to be the most economical option, but the ETA cooler has brought much better results long term.”