The concept of highly efficient filter systems, combined with excellent delivery, has proven its worth since 2010 and techNaero has supplied several very big filter installations to some very polluted areas. From the very beginning, techNaero has developed its huge filter programme in such a way that all filters are made in sections able to be stowed into ordinary containers and shipped to even the most remote area worldwide. At the same time, this means that production can be carried out anywhere where the right skills and prices are available. Due to this, and the very low freight prices for ordinary containers, techNaero is very competitive all over the world. When talking about high quality and efficient filters, the company claims that its system is second-to-none.
DELIVERED SINCE 2010Since 2010, techNaero has delivered 13 very big installations to companies in the coal, steel and mining industries in the Ukraine, Russia and Georgia. The filter systems have a high hourly cleaning capacity. For example, in total, 28,000kg of very fine dust particles are taken out of 800,000m
3 of polluted air. The supplied filters operate with very fine coal dust, fine ash and different metal alloys such as ferrosilicon etc. — some with explosion venting and some without.
The biggest filter to be delivered by the company so far was 4.6m in diameter and 13m long; it was therefore very difficult to transport any other way than disassembled.
Even though the programme consists of standard components, which also makes it easy to expand, techNaero designs and tailor- makes every filter installation according to specific requirements
THE CONCEPTThe filters arrive on site in containers — cheap, fast and efficient — and are then easily assembled using a local work force (perhaps assisted by a supervisor) and then finally commissioned by techNaero’s dealer/agent or from the main office. After commissioning the end-users have both a technologically efficient and a cost-effective installation that will offer high-quality service for many years.
When finally installed the filters are very modern and efficient and fulfill all requirements. They also satisfy all the requirements in terms of explosions set out by directives such as ATEX, the NFPA68 and VDI-3673.
The round filter construction makes the filters very strong and efficient for all kinds of dust so, no matter if there is a huge under- pressure or overpressure in the system the filters are able to cope with it.
techNaero is a relatively young company and at present is represented in Denmark, Norway, the Ukraine and China. However, it is working to expand its group of agents and dealers worldwide. The Buttimer Group has been designing and building mobile, rail and stationary dockside unloading hoppers for more than 20 years. During this time numerous technical challenges have been encountered and solved, be they functional, structural or mechanical.
In recent years the demand for quicker cycle time for both unloading and loading of ships, coupled with larger vessels, has put an ever-increasing demand on larger and larger capacity handling equipment. This, however, brings with it its own problems; the larger the capacity, the larger the equipment and so there are huge structural and mechanical demands, plus the rapid displacement of large quantities of dusty product creates an environmental problem, not to mention the effects of dust on all mechanical equipment.
The two main problems that have been encountered in the units are, firstly, keeping the structural integrity intact, and hence eliminate cracking of twisted structures, and the eliminating/ limiting of dust emissions into the surrounding environment. The structural solution is briefly explained below, followed by in-depth description of the dust problem.
One major issue that had to be overcome once Buttimer started to produce pneumatic tyre mounted units, dockside mobile loaders (DML), was a system to counteract and eliminate the twisting of the structures whilst they travelled over uneven ground. Regardless of how level the operating quay wall is, with the size of the DML measuring up to 14m x 14m and 18m high, there are large deflections over the structure, and as it twists it exerts very high torsional loads on all joints. Buttimer has developed and successfully produced a hydraulic system that acts
as a suspension, lifting (jacking) and braking system. This system takes up level variations in excess of 1m over the diagonal of the unit. This, coupled with Buttimer’s advanced mechanical steering system, allows for a highly manoeuvrable unit. This system has an Irish patent and also a worldwide patent pending.
As a direct consequence of the nature of crane and grab bulk unloading, large quantities of airborne dust are generated. The main areas where this occurs are where the grab releases the product into the hopper and where the product is then fed from the hopper into a truck or wagon or onto a conveyor. As the cargo is dropped into the hopper an equivalent quantity of air is displaced and as it evacuates the hopper it brings with it dust. Then as the product is evacuated into open wagons and trucks the problem is further exacerbated.
As a result of airborne dust many consequential problems are encountered. Firstly, environmental. Bulk cargoes range from feedstuffs, grains and cereals, fertilizers to coal, iron ores etc. Each product has different hazards associated with it and these are only further accentuated when the port area is in close proximity to residential or commercial buildings. Also contamination of the water is a concern. Secondly, the dust can cause havoc with mechanical equipment on the quay. Air filters and engines can become clogged and choked in short periods of time. Thirdly, cleaning of the surrounding areas can be time-consuming and expensive, not to mention hazardous.
When Buttimer developed its unloading hoppers, DMLs, RMLs (rail mounted loaders) and SMLs (static mounted loaders), it endeavoured to address dust emitted in the loading and unloading of the hopper. The first item fitted on the top of the hopper is the loading thimble. This is an approximately 3m high wall above the top of the hopper into which area the grab is situated before opening and discharging the product. Secondly, below the thimble and directly on top of the hopper there is a thrash grid to stop any unwanted objects or lumps of product. This thrash grid is sitting on a flexible flap system. This is a simple mechanical system that has angle steel plates with vertically hanging rubber flaps. Finally the thimble sits flush with two sides of the hopper and on the other two sides it sits inside the hopper wall. Within this cavity are placed insertable reverse jet cassette filters.
To explain briefly how this becomes effective: as the grab passes into the thimble opening and starts to discharge, it creates an enclosed space bounded by the open grab on top, hopper at bottom and thimble on four sides. As the cargo passes through the flexible flap system the flaps move to the side, the cargo slides over the angled plates and the rubber flaps close after stopping the dust passing back up through the grid as the air is displaced. However, approximately 10% of the grid is left open, to allow for the ingress of air so that the reverse jet filters have the required quantity of air to pull. The reverse jet filters suck the dusty air from the thimble area through the cavity between the thimble and hopper sides. The reverse jet system then clears the filter bags and the dust then falls directly into the hopper.
In the unloading area again an endeavour is made to create a controllable and finite space. This is created using hanging rubber curtains that the wagon or truck drive through. Also situated on all hopper outlets are mechanically operated loading chutes, these being fitted with automatic retraction system so that the cargo will drop the minimum distance to the bed of the truck or wagon and hence generate as little dust as possible. There is a fan connected to the chutes which extracts dust up through it and is in turn blown back into the top of the hopper. Where a conveyor is the means for evacuating the product the connection between it and the hopper is easily controllable and so doesn’t cause extra problems. The final area Buttimer addresses is the plant and equipment
room. One common problem that was encountered on numerous occasions was the generator, compressor etc would become choked with dust and so overheat. To solve this problem a dust free control room has been situated in the mid section of the hopper. This room is kept dust-free, utilizing a positive air pressure in the room and hence the dust is not drawn in. This is achieved by installing a fan system to blow the require volume of filtered air into the room. This also has the added benefit of keeping all running motors cool during operation in high temperatures.
With regard to loading at the top of the hopper and the use of a flexible flap system Buttimer greatly reduces the quantity of air that needs to be pulled through the filters, reducing it by more than 60% compared to having an open grid. This saves greatly on operating costs, but most importantly it helps limit the dust emitted into the environment.
Finally, the units are easily cleaned between uses or products by means of an onboard hose reel system accessible to all areas of the unit for flushing down. This is of particular interest in supporting the flexibility of Buttimer’s units to cater for multiple products easing or eliminating the fear of cross contamination.
All measures taken within the Buttimer design will reduce and limit the dust emitted, but cannot completely eliminate it. Due to the nature of the products handled and the fact that the grab is open to the elements from ship to unloading hopper one can never claim to eradicate dust altogether. Also the effectiveness of the system is very much dependent on the competency of the crane and unit operators. Buttimer can say that having supplied these units to many different clients in numerous countries and for a broad spectrum of products it has received rave reviews and testament to that is its repeat customers. Whilst the company has standard units to suit most common grab sizes, it is always open to accommodating whatever its clients’ needs may be.
PEBCO®’s systems help to keep bulk handling safe and free from fugitive dust
PEBCO
® is recognized worldwide as a manufacturer of powder and bulk solids handling equipment. PEBCO® designs and manufactures customized gates, valves, diverters, mass flow feeders, air slides, dustless loading spouts, telescopic chutes, Cleveland Cascade
® chutes and systems for barge, ship, truck and railcar loading.
PEBCO
® has become an established equipment provider in the coal and cement industries while at the same time expanding its expertise in other materials such as ferrous and non-ferrous ores, minerals, chemicals, and forest products. PEBCO
®’s products are also used in various other applications such as mining, power generation, waste incineration, lime, fertilizer, and dewatered sludge.
Since 1977, PEBCO
®’s corporate headquarters have been located in Paducah, Kentucky; on the western edge of the Kentucky coal fields and south of the Illinois basin coal fields. The company has been servicing mines, industries and utilities involved in fossil fuels for over 30 years. Through years of experience and service, PEBCO
® has grown to global prominence with headquarters in the United States and representation throughout the world.
Over the years PEBCO
® has assembled a team of specialists with a wide array of experience in various types of bulk material control. PEBCO
®’s engineering team treats each application individually and custom tailors 80% of products to exact
customer specifications. Seeking solutions to unique material handling problems, PEBCO
®’s experience, versatility, and innovation have led to the development of several patented products, features and options for equipment used in the dry bulk solids handling industry. As a result, PEBCO
® has patented products that demonstrate the innovation of the company in the field of moving, storing, and weighing bulk solids. PEBCO
® patents include: ROLLING BLADE
® Gate, Mass Flow Feeder control technology, Uni-Load® Chute and the Cleveland Cascade
® chute.
PEBCO
®’s dustless loading spout is used for loading bulk material into trucks, railcars, barges and ships, as well as for discharging material onto stockpiles. The dustless loading spout was designed with the following benefits in mind:
- fugitive dust containment;
- three-cable winching for additional stability; and
- internal polyethylene, abrasion resistant steel, urethane or stainless steel cones.
PEBCO® is a company dedicated to standing behind what it designs, manufactures, and sells. It offers an array of standard products, while at the same time seeking solutions to unique material handling problems. Utilizing the matrix system of management, the company co-ordinates the functions of: engineering, procurement, fabrication, installation, and preventative maintenance and service.
Geldof — handling wood pellets with zero dust emission
When handling bulk solids, the creation of dust is an undesirable, yet
often seemingly unavoidable result. Taking woody biomass such as wood
pellets or waste wood as an example, dust emission leads to production
losses, negatively affects the environment and involves a major safety
risk in the form of a potential dust explosion.
Geldof has gained extensive knowledge in providing effective
biomass-handling solutions for logistic and utility companies throughout
Europe.
Geldof recently installed a dust suppression hopper in the Port of
Ghent, Belgium. It has an impressive capacity of 1,000tph (tonnes per
hour). The hopper was especially developed to ensure the safe and clean
unloading of wood pellets by grab crane. Employing an innovative design,
Geldof succeeded in retaining all dust emissions completely within the
product stream. The result is both optimal efficiency and zero dust
emission. This concept is applicable to fixed and mobile units with
capacities and properties engineered to each individual application.
Such installations unequivocally secure Geldof’s proven and enviable
record of accomplishment in handling various free- flowing granular
products.
It is clear that dust control measures are required for the safe and
environmentally appropriate handling processes in all related equipment.
This year Geldof carried out a turnkey wood pellet handling
installation for the Electrabel Gelderland Power plant in the
Netherlands. Barges are unloaded pneumatically at this site at the rate
of 500tph via a mobile unit that eliminates dust emissions. The complete
circuit —from quay to boiler — uses completely closed conveyer belts, silos, hammer mill and buildings kept at a small negative pressure to avoided any possibility for wood dust to escape. It is obviously unavoidable, however, that wood dust is present within the system, therefore secondary containment measures such as dedusting and fire and explosion protection equipment are in place. All of the company’s developments are accompanied by all required studies, documents and certification.
Geldof is a European supplier of industrial equipment — including turnkey projects — for the
storage, handling and processing of bulk solids, liquids and gases. The company has an impeccable reputation for excellence in the engineering and realization of dry bulk handling installations, storage tanks, pressure vessels, flue gas treatment and special one-of-a-kind projects. Geldof offers its customers in Europe and other parts of the world A-Z solutions, renowned for their quality, functionality, efficiency and durability.
Geldof is primarily active in the (bio)energy, environmental and oil and gas sectors and also serves a broad range of other industries (construction, mining, steel and metal, bulk food, et cetera). The company remains a reliable partner by always placing its customers first. It has consistently distinguished itself through its specialized competency, organizational and operational excellence and its value-driven way of using its customers’ specific needs as its principal focus.
Dust Solutions Incorporated controls dust with semi-permeable wind breakers
Dust Solutions Incorporated (DSI), headquartered in Beaufort, South Carolina, USA, manufactures and supplies simple and effective solutions to many of the dust issues port operators encounter. One of these is reducing or preventing dust emissions from stockpiles and material handing operations using DustTamerTM wind fence/wind screen systems.
DustTamerTM is a man-made wind break system that consist of a specially designed semi-permeable fabric and attachment hardware that is installed on column supports such as wide flange beams, steel pipes or wooden poles. It is typically located on the upwind side of the area that requires protection from the wind.
Permeable wind fences work much better than a solid structure, because of the fabrics specially designed porosity. Approximately 30% to 50% (depending on fabric selection) of the ambient air will bleed through the fabric equalizing the air pressure differential from one side of the fabric to the other. This reduces air velocities and creates a lee zone just like a grove of trees does in nature.
Solid structures like storage domes have openings for equipment access, dumping or conveyor stacking activities. These open areas can be great sources of dust creation by allowing air to move from a high to low pressure area, increasing air velocities and the amount of airborne particulate. In addition containing the dust in a building may create worker health and equipment wear issues that did not exist before enclosing the source.
DustTamerTM free standing wind fences are used in a variety of applications such as material stockpiles, stack out conveyors, truck and railcar loading and unloading stations. DustTamerTM is also commonly used at dump pockets and load out silos in conjunction with DSI Dry FogTM systems. According to David Gilroy, DSI sales manager, the screen reduces the effect of ambient wind blowing across the dump pocket. This results in retaining the dust within the hopper long enough for micron sized water droplets (Dry Fog) to impact and agglomerate the airborne dust. The dust particles increase mass makes it fall back into the hopper without wetting the material (see photo on the top of p107).
SYSTEM COMPONENTSThe following components make up a wind screen system. DustTamerTM fabric is specifically designed for use as a wind reduction material. It is made from an industrial grade polyester, resistant to UV rays, in-climate weather and temperature extremes. Its unique ability to be stretched and tensioned to 500lbs of pull prevents “flagging” of the material and consequential damage due to abrasion.
The standard fabric width is 90cm (35.5 inch) wide and is available in forest green colour. The fabric is generally installed horizontally, spanning support columns as wide as 20 feet apart. Custom colours, widths and porosities are available in larger quantities.
Stand off brackets are specially designed metal brackets to ‘stand off’ the fabric from the support columns. This prevents the fabric from coming in contact with sharp edges or rough surfaces that I-beams and wood poles may have. They also make installation easy when attaching the fabric to the support columns by providing a material that is thin enough to allow self drilling/tapping attachment screws to penetrate the metal without pre-drilling.
Lock bars are used to ‘pinch’ the wind screen fabric against the stand off brackets. The lock bars are pre-drilled to accommodate self drilling/tapping screws.
INSTALLATION
Installation of the fabric is a relatively easy process. The fabric is lightweight and easy to work with. Starting at the top of the columns, the fabric is attached on the starting column and then tensioned and attached to the column supports with the lock bar system. Typical equipment and tools include man lifts, drill drivers and boom trucks
SUPPORT STRUCTURE
Wind screen fabric can be attached to a variety of surfaces. When used in place of solid siding on a building the existing column supports can be used with little or no modification. Other times a simple tubular steel frame is used to surround or cover a hopper similar to a cage or awning.
A free standing wind fence will require its own structure. Column materials can vary based on local conditions, available materials and engineering requirements. Typical materials include, wood poles, steel beams, channel iron, and steel pipe.
DESIGN AND ENGINEERINGSeveral factors must be considered when designing a wind fence system. These factors fall into the following categories:
1. Wind direction(s) and velocities. 2. Area of concern where dust is an issue (neighbour, water way, other facilities and stored shipments).
3. Size, configuration, position and height of the dust source (storage pile). 4. Existing site conditions including equipment traffic patterns, other structures (including underground) and grade of terrain. 5. Engineering factors that include wind load, seismic conditions, soil type and selection of column supports.
CONCLUSIONDust Tamer wind fence/screen systems, can be a highly effective yet cost effective measure to help control
fugitive dust, lessening environmental concerns and decreasing product loss. With some bulk materials, reducing product loss can increase profits and therefore pay for the fence in matter of time. It is a cost effective alternative to buildings and other solid structures and it can increase worker safety.The fabrics opacity can reduce the visual impact of your facility making your activities less obvious. It can be used as a stand alone system or in conjunction with Dry Fog Systems for point sources.
Keep clean with LISTENOW filter system
It’s in the nature of things: during loading of bulk materials there will be dust emissions, which is inconvenient and could even be noxious to the operators and harmful to the machines and the technical equipment.
The high performance filter system from LISTENOW lead to a significant reduction of dust (less than 5mg per normal cubic metre) and offers considerable advantages:
- clean air during loading;
- well-being and increasing production;
- less outage time by higher machine- productivity;
- any blocked exhaust pipes; and
- cost reduction by reduced cleaning.
According to application and use, it is possible to choose between an integral- or separately mounted scavenging-air-filter-system. Both models are characterized by an especially robust design. They are responsible for the return of the captured dust to loading material.
The filter housing is made of stainless steel and laminated fibreglass plastic, a solid construction.Therefore a more generous transition between loading equipment and filter is possible and the detachable housing cover also gives optimal maintenance access. The maintenance of the cartridges is on the clean gas side. The filter control is adjustable according to requirements.
The filtration devices are available in following sizes: 9, 14, 18, 24 or 30m2 (special size to 56m2)
Two weeks’ time for ESP conversion at Askale C¸imento, Erzurum Plant (Turkey)
INTRODUCTION
With more than 40 years’ history, CTP Team (Bedeschi Group) is a major presence in gas filtration technology application and has proven once more that it is a reliable partner for gas dedusting equipment installation and emission control, writes Roberto Binago, sales & projects director, CTP Team Srl — Bedeschi Group.
On June 2011 the CTP bag filter concept featuring low- pressure cleaning technology was put in operation for Line 2 at Erzurum plant of Askale C¸imento company and the 16 days’ shutdown time commitment was, in the end, reduced by two days.
The original electrostatic precipitator has now been converted into a specific design of the CTP bag filter implementing the SWAP technology (Sonic Wave Acceleration Pulse) for bag cleaning; it now offers enhanced efficiency and increased lifetime of bags while reducing energy consumption thanks to a new generation of high-performance components.
PROJECT DESCRIPTIONAskale C¸imento, one of the major cement producers in Turkey, decided to comply with the latest regulations for dust emission in its factory located in the Erzurum region.
The gas process line No. 2 for kiln and raw mill dedusting was originally designed with an electrostatic precipitator; the scope of this project was to re-use the existing facilities as much as possible and convert the ESP into a state-of-the-art bag filter for best filtration efficiency.
The upgraded dedusting line was designed by CTP with the following features:
- re-use of some of the existing ESP components such as hoppers, casing, inlet/outlet hoods and dust discharge system;
- supply of new filter components i.e. bag cleaning and filtering sets, clean gas plenum and top penthouse for weather protection complete with maintenance hoists;
- PLC for filter control;
- fresh air dilution damper for bags protection against temperature spikes;
- new compressed air station;
- modification of gas outlet duct.
- new ID filter fan, motor and drive for clean gas delivery to the existing stack.
The 3D layout arrangement and final configuration of the ESP conversion into bag filter with ancillary equipments are shown in Picture 1 above.
BAG FILTER AND SWAP SYSTEMAs for any conversion from an existing precipitator into bag filter, since the internal gas distribution towards electrodes and plates is completely different from the approach to the filtering bags inside the a fabric filter, intensive CFD modelling is always mandatory and is usually performed during the engineering phase before proceeding with manufacturing of new parts as well as for any modification of existing ones.
Picture 2 below shows part of the CFD study which is tailor made every time by CTP for any new process filter and particularly in case of modification of existing equipment.
In order to fit the necessary filtration area within the original ESP size, the filter design was fixed with 7.5m-long bags and equipped with the SWAP cleaning system which gives very high performance at low air pressure, for a perfect cleaning of 19 bags on a single row at the same time.
Picture 2
The SWAP technology developed by CTP Team is a unique bag cleaning system at low air pressure, designed to remove dust from several bags of extended length at the same time, with one single shot of compressed air, at best efficiency and minimum stress of the filtering element.
Thanks to this proven technology applied to many new filters as well as ESP conversions in several plants worldwide, CTP Team dedusting units can operate with on-line cleaning procedure which means no need to isolate the filter section during the cleaning cycle and consequent mechanical simplification and maximum reliability of the system.
The principle of SWAP cleaning technique is shown in Picture 3.
Picture 3 - principle of SWAP cleaning system.
In comparison with the conventional high pressure bag cleaning method, with SWAP technology the bag is not blown with primary air (from the tank) with addition of much more secondary air (from filter plenum) due to the Venturi effect. The special design of the cleaning valve, operating at high speed and fast response, creates a travelling wave starting from bag top line down to the bottom with the same profile and efficiency independently from the bag length. Depending on the size of blow pipe, bag and pneumatic valve, this system is capable of cleaning up to 30 bags at the same time with lengths up to 12m by means of a single shot of compressed air at very low pressure even in ‘on-line’ cleaning mode.
NEW ADVANCED FEATURESDue to the continuous technological improvements, in terms of increased efficiency at minimum energy consumption, the CTP team has now reached an important new goal.
With special powerful piston type valves, rather than the more traditional membrane-type ones, installed directly onto the pulse header tank, the very fast action of the valve and the elimination of Venturi, normally located at the mouth of the bag, a short and very fast pulse acts as a wave and travels along the entire bag at sonic velocity regardless of its length.
The innovation is related to a much shorter valve opening time and reduced inertia of the valve elements which lead to significant improvements in terms of cleaning efficiency, energy consumption and long-term reliability thanks to a lower compressed air pressure but enhanced pressure induced inside the bag up to the bottom area. The final result is a shape of the pulse which is such that the required acceleration of the filter fabric are achieved over a much greater length of the filter bag than with any other cleaning system available today in the market. Besides, a highly reduced consumption of compressed air required from the compressor is capable of cleaning an increased quantity of longer bags at the same time, extending the expected lifetime even more.
In Erzurum plant the CTP bag cleaning system is currently working at less than 2.5 bar; as opposed to the 6 bar used in the traditional pulse jet concepts; an additional benefit is that the SWAP technology also eliminates any problems of condensation on the inner surfaces of the filter bags caused by the temperature drop of expanding high pressure air.
A view inside the filter top penthouse is shown in Picture 4.
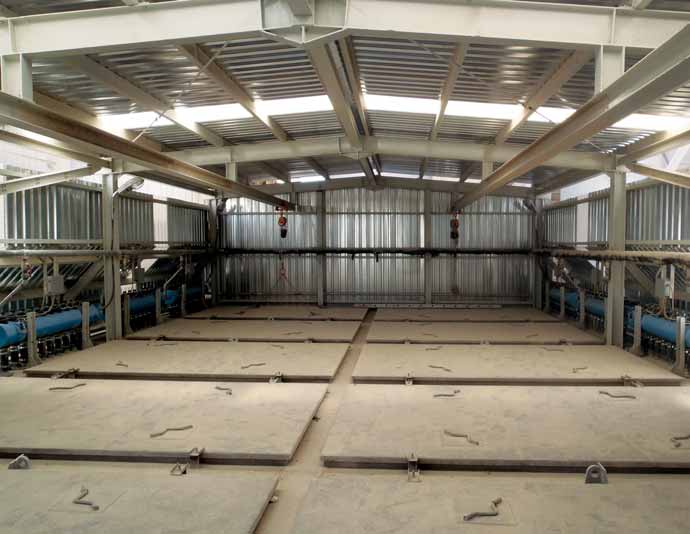
Picture 4
The air tanks equipped with new concept valves are visible on both filter plenum sides.
In conclusion the new improvements of the cleaning system are the following:
- top efficiency of bag cleaning system now performing the CTP SWAP technology by means of sonic piston valves;
- full control of the cleaning system now including the valve opening time regulation down to very low levels;
- dedicated PLC with full cleaning process control; and
- advanced calibration of technological parameters for optimal cleaning air working pressure, minimum pressure drop and reduced energy consumption.
PLANT PERFORMANCEAll the targets related to the plant performances have been fully achieved and emissions are even lower than expected.
In particular, the dust emission at the stack is lower than 1mg/Nm3 and the total filter pressure drop is 11mbar.
CONCLUSIONThe challenge of dismantling the existing precipitator and converting it in a new bag filter in two weeks’ time, has been fully achieved by CTP Team at Askale Erzurum plant in Turkey on June 2011.
A huge preassembling work before kiln stoppage, a sound design of new equipments as well as a perfect scheduling of all site activities, have been the key to achieving this significant result.
In Picture 5, one section of filter plenum positioned on top of ESP: the installation of few big pieces of equipment is mandatory to minimize the erection time.
In Picture 6 the gas outlet side view of the bag filter ready for start-up.
In addition to the well proven technology in gas filtration featuring the SWAP bag cleaning system, some new improvements in terms of efficiency, reliability and energy saving have been implemented by CTP Team for this project.
Any optimization of the filter size is ever more possible, thanks to the possibility of using longer filtering elements cleaned in few rows of many bags each always at best working efficiency.