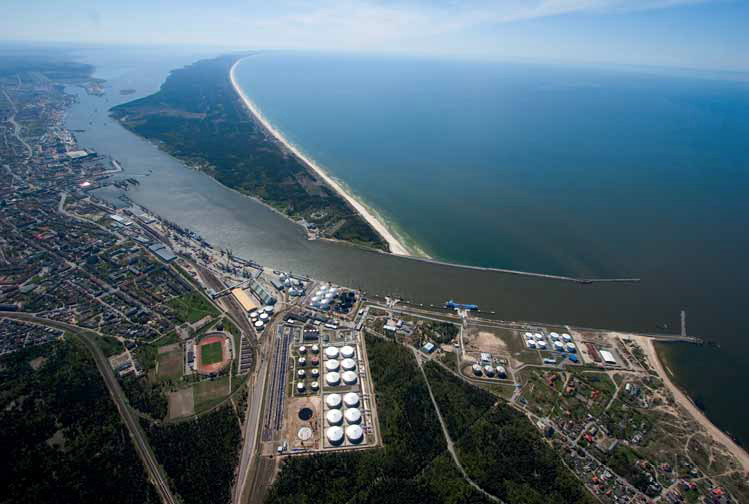
Investments raise Lithuania’s Port of Klaipeda to a whole new level
The largest investments in the history of the Port of Klaipeda, implemented last year, have already borne tangible fruit. In 2013, 301 million litas (approximately US$110 million) excluding VAT were invested in the infrastructure of the Port of Klaipeda — three times higher than the investment in 2012, or two times higher than at during any one-year period of the port’s lifetime.
For the port infrastructure, 50 times more European Union (EU) fund were used than in 2011. The work carried out in the last year has propelled the Port of Klaipeda into a new era — it has now morphed from a feeder port into a hub port, i.e. cargo distribution centre where containers and bulk cargo are distributed to the entire Baltic Sea region.
“Due to the implemented huge investments, the prestige of our only Lithuanian Port is rapidly raising at the international level. We are very happy that the importance of the port and the ongoing investment are valued and understood by our politicians. A huge achievement was that we were able to persuade the government and parliament that it is not required to use profits in order to plug the holes in the budget of the
Klaipeda State Seaport Authority. In 2013, a profit of 81.4 million litas (US$30 million) was made; in accordance with the previous model, almost half of that amount would be taken from the port. There is no need to prove that the port’s assets make the best investment, because it gives a return period of 2.5 years. Such a payback is staggering not only for a state company, but in business generally,” said the director general of the Klaipeda State Seaport Authority Arvydas Vaitkus.
It is estimated that the state investments in the infrastructure of the Port of Klaipeda attract twice the private capital investment in the property designed for logistics, shipbuilding and repair services. The port can properly invest the state assets into the state property, improving it and creating additional value. What is created in the port largely determines how the revenues of almost 800 companies will be generated. About 23 000 people are employed at the port and port- associated companies.
“Statistics shows that our port is the fastest-growing port in the Baltic Sea; during the last decade, the load of the Port of Klaipeda has been increasing about 7% every year. The closest competitors of the port are the ports located to the north of Klaipeda. Constant investments, modernization and construction of new terminals enable it to compete successfully with the neighbouring ports and gravitate to a leading position. This factor has been assessed also by our business partners from abroad. For instance, transit cargo from Belarus increased even by a quarter in the first half of this year — such a leap in turnover was determined by the increased carriage of food products, fertilizers, feeds, containers and other goods.”, said Vaitkus.
The director of the Port Authority emphasized that continuous investment is vital. It is intended to make investments over 1,149 million litas (US$420 million) in the port’s infrastructure by 2018. More than half of that amount will be allocated for the deepening of the Port: 600 million (US$220 million) for the deepening of the shipping channel and 150 million (US$55 million) for extra depth at the quays.
“During the year of 2013 we have proven to the port users that we are their partners. We promptly dealt with a number of port development problem. We need to understand that the port will not achieve anything without investment. Due entirely to the investment made, the Port of Klaipeda has started this year as a hub port of bulk cargo and containers. Our next task is to take care of the companies based in the southern part of the port, in the Malku Bay, which have been undeservedly forgotten. We must develop the port steadily. Our other target — to deal with the port’s rail infrastructure issues and develop additional areas for the port’s needs, including the creation of the added value,” said Vaitkus.
The agility of the Port Authority was demonstrated during the implementation of the LNG (liquefied natural gas) project as well, which is currently in the final stages.
“Such a rapid pace of works has not yet occurred throughout the entire history of the Port of Klaipeda. Last year, in such a short time we were able to do as much as it had not been done in the previous years. I would like to point out that the dredging works were started only on 8 February 2013, although they had to be launched on 15 November 2012. Under these difficult conditions, however, the Port Authority was able to complete these works a month earlier than it was promised to AB ‘Klaipedos nafta’. We feel a responsibility to ensure that the project proceeds smoothly, that the required depth are ensured as well as the security,” said the head of the Port Authority.
According to Vaitkus, container loading is of great importance to the port, helped by the development of the container terminal which has been in operation for 20 years. The reconstruction of quay 143a has opened up new opportunities and led to a huge leap in container volumes.
The growth in fertilizers load is also impressive. Compared to the first eight months of the previous year, fertilizer load has increased by more than 36%. In total, 8.1mt (million tonnes) of fertilizer were loaded in the Klaipeda Port this year, 2.2mt more than in January–August of 2013.
It is expected that the capacity of the Port of Klaipeda to load larger quantities of fertilizers will be increased by a new bulk fertilizer terminal. This is one of the largest investment projects in the history of the Klaipeda sea cargo company KLASCO, for the purpose of which 70 million litas (US$25.6 million) were used.
Currently, KLASCO’s fertilizer loading capacity — up to 2.6mt of liquid and up to 4mt of bulk fertilizers per year — is the largest at the port. The terminal stands out by its ecological, technological and commercial security. Closed load ensures the quality of each consignment transportation in the port from the wagon to the ship. Modern technology speeds up the loading process and shortens the time of the vessel standing at the port. The loading process of the new 100,000-tonne-volume bulk fertilizer warehouse is fully automated. Now different fertilizers can be loaded simultaneously to two Post-Panamax ships at the quays with a depth of 14.5 metres, or to one ship, but with two loading machines, thus reducing the loading time by double and achieving the capacity of up to 3,000tph (tonnes per hour).
The Klaipeda Port’s fertilizer load volume was especially increased notably by UAB ‘Biriu kroviniu terminalas’ (BKT, Bulk Cargo Terminal), which performs the loading of fertilizers to containers as well. The BKT model suggests how a variety of ways can be found through the loading of traditional cargo and fertilizers in order to improve the loading efficiency and create the additional value added. BKT is one of the most efficient terminals in the port.
Possibilities for improving agricultural production have been widened after the company BEGA launched a versatile agricultural product export-import terminal, which is currently one of the largest and most modern in the Baltic region. The terminal is equipped and arranged in such a way that at the same
time, when two ships stand on the pier, one of them can be unloaded, and the other one can be loaded. This saves customers’ time; the export-import terminal’s project and technologies are adapted for loading in both directions at the same time. This gives the Port Authority almost double revenue.
“Such a modern, technologically equipped terminal, which exhibits reversing options, has never been seen in the Baltic ports. The good news is that the Port of Klaipeda is becoming from a feeder port not only to a container, but also to a bulk cargo hub. The implementation of the investment in this terminal opens wide opportunities to attract entirely new goods.” said Vaitkus about the prospects for the future.
The Port of Klaipeda has distinguished itself not only by a leap in fertilizer and container loading, but also by increasing ro/ro cargo traffic. Over the past two years, ro/ro cargo load grew by 14% in the region, and the Port of Klaipeda remains the ro/ro cargo leader in the Baltic Sea with 5mt of cargo per year. The port’s capacity to load this type of goods should further increase in the future, since in June of this year the Klaipeda Central Terminal was opened in the Port of Klaipeda — the most advanced passenger and cargo terminal in the Baltic countries.
Simultaneously, this terminal can accommodate as many as three vessels of any type: ro/ro passenger ferries, ro-pax ferries and cruise ships. The terminal can accept up to around half a million of passengers, to reload 5mt of ro/ro cargo. Currently, it is being negotiated what shipping lines will come to work in this modern terminal.
During 2013, the perspectives of the Port of Klaipeda were elevated to a completely new level. The central and southern part shipping channel has been dredged to 14.5 metres and widened by 150 metres.
“The key challenge for the future — the depth. We have no other choice, because ‘Baltmax’ ships are our greatest target. The depth in the Belt straight is 17 metres, the dominant maximum draught of such vessels is about 15 metres. We should be oriented into such ships so they can moor in Klaipeda. Otherwise, they will sail to other ports, where such a possibility exists or is being created. Thus, the dredging programme is one of the essential tasks. It is not enough to dredge the channel; we need to reach a certain depth also at the quays, where a large amount of goods is generated and where there is a great demand for ships. Future target is 17 metre depth up to the southern part. In this case, we should not only deepen the shipping channel itself, but also improve of the Port’s gates,” Vaitkus explained.
Another area in growth has been seen is cruise shipping. In 2014, the largest number of cruise ships visited the Port in its history. The giant cruise-ship Celebrity Eclipse was the longest vessel ever to call at the port, with a length of 317 metres and a height of 61 metres.
“The Klaipeda State Seaport Authority is a state company, it focuses not only on the commercial result or a direct return on investment. We are making a lot of investments that are necessary to society, the taxpayers, although this is not always useful to the Port Authority as a commercial institution. We can rejoice that we have completed another very important project, which is relevant to the residents and visitors to the city — officially completed the reconstruction of the Kairiu street, called the business card of Klaipeda, that leads from the international ferry terminal to Klaipeda city. The Klaipeda State Sea Port Authority had started the reconstruction of a 2.5km section three years ago. The work cost almost 30 million litas (US$11 million). This street is just one of many that has been reconstructed by the funds of the Port Authority. We annually invest in the well-being of the city of Klaipeda an average of 9.2 million litas [US$3.4 million],” said the head of the Port Authority.
According to the data of the port’s administration, companies operating at the Klaipeda Port pay on average about 1.5 billion litas (US$0.55 billion) to the state budget per year, which represents a staggering profit for the state. Another important figure is the jobs generated. Klaipeda Port, and its associated companies, provides employment for 185,000 people.
Langh Ship Cargo Solutions’ 20ft container
Langh Ship Cargo Solutions’ 20’ Open Top Bulk Container completes the supply of containers it offers for lease. The payload of the container is 30 tonnes and the tare weight is 3.95 tonnes.
MINING THE MARKET
The container’s properties make it ideal for use in the mining industry. The mining industry sets different requirements to containers than many other industries. The transported product is heavy, sticky, and sharp — in one word, difficult.
The 20’ Open Top Bulk Container is the answer to the wishes of the industry. The container’s flat walls are made of special steel that is three times stronger than normal Corten-steel; they are painted with a paint that endures the demanding nature of ores or scrap. Due to the flush walls the container is easily emptied in unloading and there is no need for manual removing of cargo residues.
The container’s hard open top roof makes the loading very fast for wheel loaders and the normal bulk hatches on the roof are suitable for silo loading. All the details are designed bearing in mind the nature of the transported products. Shields of the roof’s locking mechanism work as guide posts for the roof and the forklift pockets under the roof make it possible to handle the roof easily with a forklift.
The Langh Ship Cargo Solutions product family includes several transportation methods, which are suitable for transportation of heavy and sensitive steel products, heavy bulk products and even for flexitank use. Langh Ship Cargo Solutions has set as its goal to be ‘Superior in Steel Transport’.
Klaipeda Stevedoring Company BEGA: focusing on agribulk
BEGA, Stevedoring Company operates nine berths in Klaipeda sea port, Lithuania, with a total length of 2km. BEGA offers a full range of port services and logistic solutions, including cargo handling, storage, freight forwarding, distribution, transshipment, ship agency, packing of bulk products and others. The company specializes in handling of dry and liquid (non-oil) bulk products. The main commodities, handled by BEGA, are dry and liquid fertilizers, minerals and agricultural products.
During the two decades of operation, BEGA has fully developed dry and liquid fertilizers and raw materials, such as phosphates, apatite concentrate, handling facilities.
Recently BEGA has been focusing on agribulk which, as a percentage of its total cargo throughput, has increased from 7–8% in 2010 up to 25% in 2014 .
In 2012, in co-operation with Klaipeda state sea port authority and Cargotec, BEGA launched the Universal agribulk export-import terminal with total annual capacity of 2.5mt (million tonnes) and a storage capacity of 180,000m3 (planned expansion to 240,000m3 by 2020).
The terminal currently operates two berths on the jetty (each 240 metres in length) with the depth of 14.4m and the maximum vessel draught of 13m (further expansion plans are already under way).
BEGA’s multi-modal terminal complex features an integrated Siwertell solution from Cargotec, and it was developed to focus on new business in the region. BEGA can now handle both the export and transit flows of
agricultural products. For example, agricultural operations are now not limited to a particular season, so BEGA can meet fluctuating market demands for grain, soyabean meal and other feed derivatives.
The terminal is dedicated to loading and unloading vessels (simultaneously), as well as transshipping bulk cargo directly from larger to smaller vessels for onward distribution. It also is equipped for loading and unloading rail wagons and trucks. Separate storage compartments enable the terminal to store complete or part loads from large vessels, as well as smaller bulk parcels.
The largest amount, loaded into one vessel, was 74,000 tonnes (on the PIERA, which departed on 17 September bound for the Middle East); this was the largest ever grain shipment in the history of Klaipeda sea port. In total this year BEGA plans to handle 1.5mt of agricultural products, of which 1mt will be Lithuanian exported grain.
Grains for large shipments to the BEGA terminal are mostly transported by rail and small number of trucks. Also this season BEGA is accepting grain from small ships from Scandinavia and other Baltic states. The handling operations of loading Panamax vessels with exported grain and unloading smaller vessels with transit grain on the jetty are being performed simultaneously.
Lithuania is usually exports about 2–2.5mt of grain per year. Due to the geopolitical situation, Ukrainian feed exporters are searching for the ways to get into the European market. BEGA is capable of handling the flow of Ukrainian feed. BEGA is also a developing distribution centre for South American soyabean meal flows to Eastern Europe and CIS countries.
BEGA UNIVERSAL AGRIBULK EXPORT-IMPORT TERMINAL: LOADING SPECIFICATIONS
- loading the warehouse: 1,200m3/hour;
- v loading the vessel: 1,500m3/hour;
- v unloading the vessel: 1,200m3/hour;
- v loading the railway wagons (trucks): 600m3/hour; two railway wagons or trucks at the same time);
- v unloading the railway wagons (trucks): 1,200m3/hour (four wagons or two trucks at the same time)
KLAIPEDA STEVEDORING COMPANY BEGA: MAIN DATA
- the length of berths: 2km;
- maximum depth at berths: 14.4m;
- maximum vessel draught: 13.2m;
- total area: 30ha;
- the reserve area for logistical and industrial activities: 8ha;
- bulk terminals storage capacity: 450,000 tonnes (planned expansion to 730,000 tonnes by 2020);
- liquid reservoir capacity: 70,000m3 (planned expansion to 100,000m3 by 2020);and
- the total capacity of terminals: 8mt per year (planned expansion to 14mt by 2020).
Riga Central Terminal acquires Mantsinen 200 ES HybriLift® material handler
Riga Central Terminal (RCT) is acquiring a Mantsinen 200 ES HybriLift® material handling machine, which will considerably increase the company’s cargo handling efficiency. Expected delivery time of the equipment is December 2014.
“The machine will enable us to strengthen coal handling operations, including unloading wagons and stockpiling coal. Mantsinen 200 ES HybriLift® is one of the largest hydraulic material handling machines available on the market which proved reliability and efficiency in coal handling operations. Today, RCT is looking into increasing annual handling volumes and this machine is one main part of RCT’s total investment project. Machine is features the unique Mantsinen HybriLift® energy saving and recovery system,” says Eri Esta, chairman of the RCT Board. Mantsinen 200 ES HybriLift® features a 10.5 metre-wide rail-mounted gantry with a free height of 5.7 metres under gantry. This set-up will allow two rail-wagons to pass through the machine undercarriage. The machine has a reach of 35 metres, which will easily allow stockpiling up to 12 metres high and over 25 metres wide. Mantsinen will provide after sales services together with new partner Willenbrock Latvia.
Mantsinen is a family company based in Finland. Mantsinen has been providing economical and ecological material handling solutions for more than 50 years and producing material handling machines for 15 years. Mantsinen has a strong market share in coal handling in Russia and is now looking into expanding markets into Baltic countries.
Located in the port of Riga, RCT is the largest stevedoring company in Port of Riga, having provided services since 1996. RCT is a part of the Riga Commercial Port LLC (RTO) group. In 2013, RCT handled 10.4mt (million tonnes) of cargo with
revenues reaching €22.3 million. RTO is the leading investor, developer and operator of port terminals and transit services in the Republic of Latvia. Cargo volumes handled by RTO in 2013: terminal operations (11.9mt), railway transportation (9.6mt), and forwarding services (11.5mt). The consolidated turnover of RTO companies in 2013 was €209 million.
Cuypers Vorkliften Nv selects the strongest Mantsinen 200 M in Antwerp
In August 2014, Mantsinen Group Ltd Oy delivered a Mantsinen 200 M HybriLift® to Cuypers Vorkliften Nv, in the Port of Antwerp in Belgium. The Mantsinen 200 M HybriLift® is a mobile hydraulic harbour crane, mounted on a wheel-based undercarriage. This Mantsinen harbour crane is used mainly for loading steel coils and other steel products and it boasts impressive productivity of 60 cycles per hour in steel coil handling.
Cuypers Vorkliften Nv in Belgium is an Antwerp-based rental company, which specializes in heavy forklift trucks, container reachstackers, empty-container handlers, ro/ro-tractors (2×4 and 4×4) and hydraulic cranes. Cuypers Vorkliften is a renowned operator in Port of Antwerpen, providing short- and long-term rental with experienced and trained operators or drivers when necessary. The machinery is available for virtually all kinds of material handling and the fleet includes several special attachments. Cuypers Vorkliften head office and service workshop is centrally situated in the Port of Antwerp area and the company is known for its 24/7 services.
Mantsinen 200 M HybriLift® is the newest and largest investment for Cuypers Vorkliften Nv. World-premiered in June 2014, it is currently the strongest and largest hydraulic material handler on markets with a wheel-based undercarriage. Crane reach is 26 metres and lifting capacity is impressive 36 tonnes at 20 metres reach. Despite the enormous size of the machine, it provides precision, speed and safety which hydraulic material handlers are well known for. Mantsinen 200 M HybriLift is equipped with stage 4 final Volvo diesel engine, which is boosted by Mantsinen HybriLift® energy storage and recovery system. HybriLift® technology was launched by Mantsinen in 2008 and is has a strong track record of improving energy efficiency by up to 35%.
Owners of Cuypers Vorkliften Nv, Lieven Van Hoylandt and Marc Cuypers are pleased with their new investment. Van Hoylandt comments “Mantsinen 200 M HybriLift® has proven to be a very efficient, safe and economical crane for our operations”. Cuypers continues:“At this moment machine is operating at Wijngaard Natie terminal and mainly handling steel coils, every lift between 10–36 tonnes net weight by using the special attachment for steel products especially designed ‘by Cuypers’ for coil handling”. Cuypers’ coil clamp has been tested for 4,000 operating hours (SWL 25 tonnes) with a Mantsinen RHC 140 hydraulic crane, delivered to Cuypers 2007.
Cuypers Vorkliften has been extremely satisfied with the performance of Mantsinen 200 M HybriLift® and has already placed a repeat order. Van Hoylandt comments:“the speed of the crane is more than we expected and fuel consumption less than was calculated, so far our future plans are to utilize this modern crane in our rental ship loading and unloading operations with materials of breakbulk. We have also made the repeat order for second Mantsinen 200 M HybriLift® crane. The second crane will be delivered February 2015 and will be operating at Nova & Hesse-Noord Natie Stevedoring NV terminal.”
Mantsinen announces strategic partnerships
Finnish Mantsinen Group Ltd Oy has announced a partnership with Latvian SIA Willenbrock Latvia and Lithuanian UAB Willenbrock Baltic for the distribution of Mantsinen hydraulic cranes and material handlers, as well as after sales service on existing and new machines.
WILLENBROCK BALTIC is a well-known company, which has been serving harbours and terminals in the Baltics since 2007. It has a strong focus on maintenance and is committed to provide the best possible service 24/7. Service points are located strategically in Riga and Klaipeda from where all the customers in Latvia and Lithuania can be served quickly with fully equipped service trucks.
WILLENBROCK BALTIC is already a dealer of Terex-Fuchs, Linde, Konecranes SMV and Terberg among other non-harbour- oriented industry products. Chairman of the board at Willenbrock companies Gediminas Simkus says:“Mantsinen has a long history as a logistic service provider in the Baltics and the
company already has a good reputation here. Now we are bringing Mantsinen back with their new product range and with our local services. Mantsinen cranes and material handlers offer unbeatable efficiency and fuel-economy compared with other machines on the market. Energy saving is a global trend, which all port operators emphasize in coming investments. We are happy to be able to offer the most economical and ecological material handling solutions for bulk and general cargo handling in Latvia and Lithuania.”
Speaking for Mantsinen Group Ltd Oy, area sales director Tapio Pirinen comments that “Mantsinen is fortunate to find a partner who is so well known for good service and has a strong presence in the local harbours. Latvia and Lithuania are not large markets, everyone knows each other and good reputation is worth more than gold. Therefore it was important for us to find a partner that has already earned its reputation and whom the customers can count on at all circumstances.”
Finland’s Port of Inkoo: specialist in bulk handling
The Port of Inkoo in Finland specializes in bulk cargoes, and handles approximately 1.3 million tonnes of bulk each year. The port is a privately owned, public commercial port.
Right next to the port is the Fortum power station, which has its own port facilities that the Port of Inkoo can use, if needed, by separate agreement.
The port’s whole traffic is tramp shipments; there is no liner traffic into the port.
The port is one of the 23 winter ports in Finland, which are kept open by the icebreakers of the Finnish Maritime Administration in wintertime. The ice conditions are, however, easy at Inkoo during normal winters, and thus the channel is almost always ice-free.
The port specializes in the handling and storing of dry bulk materials. Its competitiveness is based on flexible handling and storing possibilities, long experience in handling of bulk materials and the port’s geographical location together with good connections by sea and road.
The port is situated in the bay of Fagervik at Inkoo district. There are good and fast road connections to Helsinki and other main centres of trading and industry. The distance to Helsinki by road is about 60km, to Lohja about 30km, to Lahti about 150km, to Turku about 120km and to Tampere about 200km.
Port regulations accepted by the local authorities of Inkoo on 17 March 2005 must be followed within the port area.
The company has its own stevedoring department, which offers vessel and cargo handling services at the port of Inkoo, and its own clearance and forwarding departments at Inkoo and Parainen offering services for vessel in these ports and other ports in the near distance.
EQUIPMENT AND STORAGE
The Port of Inkoo has three cranes — one 10-tonne crane on rails on the quayside (capacity 200–400tph [tonnes per hour]);
and two mobile multipurpose cranes (maximum lifting capacity about 6 tonnes and 10 tonnes, operating at 140–400tph for bulk goods, and 150–200m3/hour for round timber).
Other equipment includes:
- loading belt for gravel (loading speed about 300tph);
- six frontloaders (17–22 tonnes); and
- trimming machines, forklifts; and
- one weighbridge.
In terms of storage, the port offers 30ha outdoor storage areas, as well as 14 warehouses, ranging in size from 800m2 to 2,500m2. It also has a 4,500m2 warehouse for china clay.
SECURITY
The port complies with the security regulations according to IMO’s (International Maritime Organization) ISPS rules valid since the 1 July, 2004.
The port area is a closed area where by sea only vessels complying with international safety regulations can arrive, and by land only those vehicles or persons who are permitted to do so by the port authorities. Persons unauthorized to visit the port area can be removed from the area, if necessary by assistance of police, customs or border guards.
The vessels shall before the arrival to the port give their security report to the port either through their agent or direct to the port.
SERVICES
The port offers services for vessels. In addition to the port’s own services there are many specialized companies in the neighbourhood offering repair and maintenance services. These companies can be easiest reached by the port service/ship’s agent. Services include: mooring and unmooring; towage; electricity; water; ice breaking; and waste collection and environmental services. Fresh water can also be supplied.
Bulk handling activities at the Port of Grenaa
The Port of Grenaa in Denmark is continuously investing in further growth. In February 2014 the Port of Grenaa increased its capacity with a new Gottwald mobile crane. The crane is suitable for both bulk and heavy lift and has a capacity of up to 140 tonnes. The Port of Grenaa has modern equipment and can solve all types of tasks concerning loading and unloading with now two Gottwald mobile cranes and two loading machines; Sennebogen 860 M special and Fuchs.
The decision to purchase the new Gottwald mobile harbour crane was to enable the faster handling of more bulk products, something that the Port of Grenaa — and its customers — has wanted for a long time. Henning Laursen, managing director of the Port of Grenaa, says, “Now we are looking forward to receiving a new grab for the crane. It will increase capacity and speed significantly.”.
MORE COMPETITIVE
Both Port of Grenaa and its port customers are looking forward to the opportunities that the new crane provides. If it is possible, for example, to load a ship in two days instead of three, this makes a big difference to the bottom line:
Being able to operate with two cranes is simply a prerequisite for being able to operate effectively enough, primarily in relation to loading, but also in the sense that we can quickly empty the vessels, so overall, they spend less time in port.
A FANTASTIC HARVEST AT DJURSLAND
A long and hot summer in Denmark has meant lots of grain, also in the warehouses at the Port of Grenaa. Even outdoor areas were used by one of the customers to store mountains of grain. It has been the best harvest for many years and the earliest as well. Mainly it is wheat for fodder but barley for fodder, rape and malt barley as well pass through Grenaa, Denmark. Most of the grain is being shipped out to markets outside Denmark.
The Port of Grenaa has great expertise in the handling of liquid and dry bulk cargo. It offers all the necessary equipment and storage and warehousing facilities. Further investment is planned in the form of two bulk warehouses, which are expected to be completed by spring 2015.
Clean ship’s sides reduce NORDEN’s fuel consumption
Dampskibsselskabet NORDEN A/S is an independent shipping company incorporated in Denmark. NORDEN was founded in 1871, making it one of Denmark’s oldest internationally operating shipping companies. NORDEN operates in dry cargo and product tankers worldwide.
In dry cargo, NORDEN is active in all major vessel types. It is one of the world’s largest operators of Supramax and Panamax dry cargo vessels and has considerable activities in the Handysize and Post-Panamax vessel types as well as activities in Capesize. The company’s Handysize and Post-Panamax activities are operated commercially by NORDEN Handysize Pool and NORDEN Post-Panamax Pool, respectively, which also operate vessels from Interorient Navigation Company Ltd. (INC), Cyprus.
NORDEN’s fleet is among the most modern and competitive in the industry and NORDEN operates a mix of owned chartered tonnage, in total 209 dry cargo vessels and 46 tanker vessels — as of 30 June 2014. In addition NORDEN has a newbuilding programme with 35 vessels on order, i.e. dry cargo 31 and tanker four — as of 15 September.
KEEPING FUEL COSTS LOW
NORDEN has since 2007 had a climate action plan to reduce fuel consumption, and when the financial crisis broke out in 2008, this also made it reduce the speed of its bulk carriers and product tankers — back then, that was called ‘slow steaming’, but today is known as ‘right steaming’.
Since January 2013, NORDEN has worked systematically to reduce the fuel consumption of the company’s fleet of owned and chartered bulk carriers and product tankers through a newly established Fuel Efficiency Team. With bunker oil costs last year of US$671 million, fuel is NORDEN’s largest expense item after hire paid for the chartered fleet. Increased focus on cleaning ships’ sides overgrown with algae, mussels, etc. has resulted in fuel savings of approximately 2% during the first half of 2014.
The Fuel Efficiency Team spent the first year developing tools, and the results of this work are now in earnest beginning to show. During the first half of 2014, the team’s work has led to
measurable fuel savings based on greater co-ordination of the different fuel saving initiatives together with systematic data collection and analysis supported by consistent follow-up. Ships’ sides overgrown with alga, mussels, etc. can at worst mean a doubling of the vessel’s fuel consumption, and by focusing on cleaning of overgrown ship’s sides, NORDEN has reduced fuel consumption by approximately 2% across the fleet.
“Two per cent may not sound as much, but in terms of money, this is a substantial saving when considering the fact that NORDEN spent US$671 million in 2013 on bunker oil for the fleet of 44 owned and 241 chartered bulk carriers and product tankers,” says Head of Fuel Efficiency, Peter Sinding, who is a Master of Maritime Engineering.
In addition to the fuel savings made by sailing with clean ship’s sides, savings were made by controlling the speed of the vessels more closely.
BETTER SPEED CONTROL
The team’s area of responsibility also includes the product tankers and bulk carriers which the Cypriot shipping company Interorient Navigation Company (INC) has put into the pools operated and managed together with NORDEN — i.e. the product tanker pool Norient Product Pool (NPP) as well as the Handysize and Panamax pools.
The systematic and coordinated monitoring by the Fuel Efficiency Team of the more than 300 vessels operated by NORDEN and NPP has made it possible to quickly and accurately pinpoint the vessels which are not sailing fuel-wise as they should — which are not performing.
ALL VESSELS CAN BE COMPARED
One of the main reasons for the success of the Fuel Efficiency Team is the fact that the team has developed tools that strip the daily reported figures from wind, waves, current, draught and speed variations. Each vessel’s fuel consumption is seen in relation to hypothetical conditions such as a speed of 12 knots, fully laden and calm weather.
“In doing so, we achieve a measure of the vessels’ fuel efficiency which does not change when the speed is increased as the markets go up or because it is windier during wintertime compared to summer. This makes data from all vessels comparable,” says Sinding, whose team is far from done reducing the vessels’ fuel consumption.
MONTHLY MEETINGS
Every month, the team meets up with the heads of chartering and operations in NORDEN and NPP to discuss what to do about the vessels that are not performing. There can be a number of measures. In addition to cleaning overgrown ship’s sides, it could be cleaning the propeller, it could be expedited docking, and it could be changed operation of overgrown chartered vessels which we do not have enough time to clean if they are only chartered for a single trip. ”We are going for the low-hanging fruit.And with further fine-tuning of the measures, we can go even further,” says Sinding.
How NORDEN finds the right vessel
With 35 vessels on order and for delivery in the years 2014–17, NORDEN’s order book is quite substantial. Read here about the process that the projects department in Dry Cargo must go through before a contract for a new vessel can be signed.
Should we buy the vessel or should we rather charter the vessel — typically for a period of seven years and with purchase option? This is one of the essential questions which NORDEN must consider when deciding on whether to expand the existing active fleet.
At the end of the first half year of 2014, the active fleet counted 255 vessels — 209 dry cargo vessels and 46 tankers. These are 45 owned vessels, 50 vessels on charter with purchase option and 160 vessels chartered without purchase option or only for single voyages.
With investments in 18.5 vessels, 2013 became the largest net investment year in NORDEN’s history, and investment in additional 7.5 vessels in the first quarter brings the order book to 35 vessels — 31 dry cargo vessels and four tankers. These are modern, fuel efficient vessels for delivery in the years 2014–17, and the investment is in excess of US$1 billion. All vessels have been ordered while prices were attractive — which they still are in spite of the negative market development.
It is the projects department in Dry Cargo which is responsible for buying and selling dry cargo tonnage while the Tankers Department handles acquisition and sale of tanker tonnage.
PROS AND CONS
About pros and cons of either owning or chartering dry cargo vessels, the head of the projects department in Dry Cargo, vice president Henrik Lykkegaard Madsen, says: “The number one advantage of owning a vessel instead of chartering it is greater flexibility.
This goes for both the operational as well as the commercial aspect — for instance in terms of where to and with what we are sailing — and it also goes for timing of a possible sale. When chartering, we are bound until expiry of the fixed term of the charter agreement which is typically seven years. On the other hand, owned vessels require a greater amount in tied-up funds, and as owners, we also assume the risk of increasing operating costs.”
Easier to charter
If the decision is for NORDEN to charter a vessel with purchase option, the company will have a finished vessel delivered by the company chartering out the vessel. So NORDEN does not have to care about the chartered Capesize vessel, the 10.5 chartered Panamax vessels and the seven chartered Supramax vessels in the Dry Cargo order book before delivery as all technical specifications, including and in particular fuel efficiency, payment and other terms of the charter contract, have been agreed upon. The owner is fully responsible for the construction of the vessel, including supervision at the yard during the construction.
In contrast — when NORDEN decides to own a newbuilding — it must itself find a yard to build the vessel and, later on, supervise the ongoing construction with its own superintendents at the yard. This is the case with the four Panamax vessels and 8.5 Supramax vessels in the Dry Cargo order book.
ADVANTAGE OF BEING A REPEAT CUSTOMER
“Especially when ordering owned vessels, we will look into what former business partners can offer. The yards are often very loyal and flexible towards repeat customers — something we experience often in Japan. But we always evaluate relevant designs of pretty much all quality yards, who could be considered, and we end up choosing the yard that can offer the right vessel and at a competitive price,” says Lykkegaard Madsen.
All 31 dry cargo newbuildings in the order book will be delivered by Japanese yards known well by NORDEN.
TWO TO THREE YARDS IN THE SHORT LIST
The projects department in Dry Cargo has quite effective methods of comparing the commercial value of the different ship designs, while the technical standard is often more difficult to assess without being in close dialogue with the yard. Therefore, a very detailed assessment of the possible candidates is usually limited to two to three yards.
”The commercial and financial requirements and limitations are assessed first. Subsequently, the projects department enters into close co-operation with NORDEN’s newbuilding department in order for our requirements specification to the yard to be as complete as possible before we go into the concluding price negotiations with the yard,” says Lykkegaard Madsen.
Delivery time from a Japanese yard is currently three to four years.
Poland’s MTMG Terminals handles wide variety of bulk product
MTMG Terminal is located at the main entrance to the Port of Gdynia in Poland, and is directly connected to the railway and road communication systems.
Within the structure of the Port of Gdynia, MTMG as a universal terminal renders the services of reloading, warehousing, big-bagging and sorting all kinds of bulk cargoes in port and maritime turnover. It is a multipurpose stevedoring company which handles cargoes like coal, coke, agri products, minerals, aggregates, sugar, fertilizers and other dry bulk and liquid cargoes. MTMG operates on five quays with depths from 9m to 13.5m. Maximum vessel length is 300m and there are no air draught limitations.
Although MTMG Terminal only came into being as a state- owned company in 1995, activities connected with stevedoring started when the Port of Gdynia was built in 1923. The terminal was privatized after Atic Services of Paris, bought the shares in 2011. From September 2014, a new owner — Hestya Energy B.V. — has taken over. Hestya Energy B.V. is a private company pursuing the development of European dry and liquid bulk terminals with the goal of creating a diversified asset portfolio through greenfield development, the acquisition of existing terminals and the acquisition of existing refining sites and related infrastructure and the conversion of these into storage terminals.
CARGOES HANDLED
MTMG Terminal is a multi-purpose terminal and, as such, it handles bulk products that include coal, coke, agri products (such as soya bean meal, wheat, rape seed, maize, rye), feldspar, aggregates, crushed stones, sugar and so forth. This list will continue to grow, as MTMG aims to be able to handle any bulk goods that its customers require. In the past year, MTMG has handled approximately 6mt (million tonnes) of bulk cargo. The majority of the bulk cargoes related to imported/exported coal, imported soya bean meal, and exported wheat.
In terms of liquid cargoes, MTMG handles these at its two dedicated quays. They include: ether, xylene, diesel, n-butanol, white spirit gasoline, hydro wax, paraxylene and many others including chemicals of the 3rd, 6th, 8th and 9th classes according to the IMDG code). MTMG is also able to handle general cargo.
MTMG’s bulk cargoes fluctuate to some extent, in response to changes in some markets. The soya bean meal, imported coal and feldspar markets are relatively stable, while exported wheat, coal/coke and imported aggregates fluctuate rather more.
GLOBAL REACH
In terms of bulk customers, MTMG’s reach is truly global. Currently, it has agreements with customers in Australia, Argentina, Brazil, Holland, the United Arab Emirates, Germany, France and others. This customer base is stable.
COPING IN A COMPETITIVE MARKET
MTMG Terminal strives to remain competitive against direct competitors such as the Port of Gdansk, Szczecin and Swinoujscie, as well as other companies within the Port of Gdynia itself. The company remains competitive by offering a universal, modern terminal that offers high quality, customized services with stable, competitive tariffs.
EQUIPMENT AND STORAGE
MTMG Terminal offers a huge variety of handling equipment to secure dedicated loading/discharging operations. All companies within the Port of Gdynia are separate, private companies.
In terms of covered storage, currently, MTMG has three flat warehouses with a surface area of 16,000m2 and a four-chamber dust-tight warehouse with a cubic capacity of 20,000m3. It also has a total open area of 70,866m2 where cargo can be stored outside.
KEEPING IT GREEN
MTMG believes firmly in the need to safeguard the environment. To keep dust emissions low, it uses spraying equipment for cargoes laying on stockyards. For agri products, it is building covered belt conveyors that feed directly to the warehouses.
RECENT DEVELOPMENTS AND FUTURE PLANS MTMG Terminal is investing in a new warehouse, which will enable it to store a further 60,000 tonnes of agribulk, using modern, fast discharging technologies. Other projects are under way to expand open and covered storage. MTMG is also carrying out dredging work at one of its quays, to increase draught from 11 to 13.5m, with further work planned to increase this to 15m to enable the handling of Baltmax vessels.
Indexator’s XR-program is ready for the market
Innovation and product development are natural ingredients within Indexator Rotator Systems’ daily operations.
Now, the XR-program has been launched for applications where extremely high demands are placed on rotator functionality. Indexator Rotator Systems, producer of rotators and ancillary equipment, has now extended its experience further into other professional areas of application.
The XR-program consists of compact and powerful rotators with strong bearings. Thanks to the proven vane motor technology the XR-rotators have high torque, good compliance and balanced braking. Their compact and robust construction provides an ability to withstand heavy static and dynamic loads, both positive and negative forces as well as side forces.
The XR-rotators provide high oilflow for grapple cylinders due to large channels — ensuring high productivity and overall economy.
“We will successively extend the XR-program with more models and variants. Currently we introduce XR 500 and XR 600, where variants with an extra channel for central lubrication
also is avaliable.”, says sales and marketing manager, Erik Svensson.
XR-rotators offers a complete solution for heavy work within forestry, material handling, scrap handling, recycling and timber handling.
Polsteam: worldwide cargo ship operator
Polsteam, formerly known as the Polish Steamship Company (in Polish: Polska Zegluga Morska, PZM), is an international cargo ship operator based in Szczecin, Poland. It operates in Poland and nine other countries and continents. Most of its operations take place in the USA, Canada, South America and Western Europe. Polsteam is a state-owned enterprise (SOE) with around 3,000 employees.
In the group, sea transport companies prevail, including Zegluga Polska S.A, Polsteam Frachtowanie, Polsteam Shipping Agency, and Unity Line.
The Polsteam Group also comprises IT business Medialand, Polsteam Zegluga Szczecinska, tourism and catering and Marine Medical Services.The group includes also Pazim, a company providing management of the most attractive office and retail complex in Szczecin, Poland.
Polish sea ports are experiencing a positive period, with significant records being achieved in Gdynia and Gdansk, as well as in Szczecin-Swinoujscie.
The focus of commodities in Polish ports has changed in recent years. Not long ago, bulk cargo used to dominate, but there has been a shift towards general cargo — mainly containerized — which represents close to the total handled.
Bulk remains a major market, however, especially coal, coke, aggregates and grain.
Most of the dry bulk freight across the Baltic Sea region is handled in universal ports serving hinterlands within a rich spectrum of industries. This means that even small ports handle different kinds of bulk cargo; in Finland, for example, 25 ports out of 47 involved in international traffic serve at least three categories of bulk (excluding wood in any form).
Large ports, of course, handle many more categories of bulk. The Port of Riga, the number one dry bulk port in the Baltic region, besides three main commodities (coal, ore and grain) also lists in its statistics dry chemicals, woodchips, ferroalloys, peat, construction materials, scrap, sawn timber and metals.
Port Szczecin-Swinoujscie: expert in bulk handling
The company specializes in handling and storage of bulk cargo, such as coal, coke, iron ore iron, scrap, grain, liquid bulks, etc. and general cargo. Quality of work is approved by ISO 9000:2008 certificate.
COAL
Coal is one of the largest cargo volumes handled in the ports of Szczecin and Swinoujscie. In Swinoujscie, coal accounts for up to 25,000 tonnes/day unloaded at two quays: Górników and Hutników.
The Górników Quay is equipped with two wagon tipplers, defreezing installation, 156,000 square metres of open storage for up to 1,000,000 tonnes, and a shiploader capable of handling 2,000 tonnes per hour. Unloading of vessels is provided by two mobile Liebherr cranes. The Hutników Quay is equipped with 40-tonne and 25-tonne gantry cranes.
In Szczecin, 1.5mt of exported and imported coal is reloaded annually in a dedicated handling area equipped with a wagon tippler and a 1,000tph (tonnes per hour) shiploader.
IRON ORE
Iron ore is handled mainly at the Hutników Quay in Swinoujscie, equipped with 40-tonne and 25-tonne gantry cranes, providing the total handling capacity of 25,000 tonnes per day, the largest on the Polish coast. There is an open storage area of total 70,000 tonnes. The cargo can be loaded or unloaded into river barges by floating cranes at the same time.
Unloading and loading also take place at the Chemików Quay equipped with two 20-tonne gantry cranes, a sheltered conveyor and storage space for 100,000 tonnes.
GRAIN AND AGRIBULK PRODUCTS
Both ports of Szczecin and Swinoujscie provide handling and storage services for grain and agribulk products. In Szczecin, Elewator EWA terminal operates a new flat storage 45,000 tonnes warehouse for meal and grain.The terminal provides specialist services, including handling, storage, weighing, drying, cleaning, fumigation and pest control. All handling operations are supervised by computer-controlled weighbridges. The loading or discharging of vessels takes place at the rate of 12,000 tonnes per day for grain and 7,000 tonnes per day for feed.
In Szczecin EWA silo with capacity of 55,000 tonnes for grain is situated and it is the largest one on the Polish coast. There are three other silos in the port of Szczecin of total storage capacity 27,000 tonnes.
In the Port of Swinoujscie, at the Portowców Quay, a big cereal terminal of BUNGE started its activity at the beginning of 2012. This modern terminal with storage capacity of 50,000 tonnes can handle all types of cereal.
BIOMASS
The ports of Szczecin and Swinoujscie offer handling and storage of bulk volumes of biomass both in export and import. Cargo can be handled directly or indirectly and stored on paved yards or in roofed warehouses depending on the type of cargo.
AREAS FOR DEVELOPMENT OF BULK ACTIVITIES
Port Szczecin-Swinoujscie offers attractive development areas with full infrastructure and prepared from a legal and formal point of view to invest in bulk handling and storage activity or port-related industry.
BULK ACTIVITY IN FIGURES
Port Szczecin-Swinoujscie offers:
- 700,000m2 of open storage area;
- 180,000m2 of covered storage;
- 151,000m3 of tanks;
- 177,000 tonnes of silo storage for grain;
- 9km of quays equipped with facilities dedicated to service bulk cargo;
- bulk cargo turnover in 2013: 4.5mt of coal, 2.7mt of iron ore, 2.9mt of other bulk, 1.6mt of grain, 1.6mt of petroleum products;
LIQUID BULK CARGO
Various kinds of liquid bulk cargo are handled in both ports. In the port of Swinoujscie, Czech manufacturer DEZA operates a tar pitch terminal with a yearly throughput of about 40,000 tonnes.
Similarly to Swinoujscie, Szczecin also has dedicated terminals for pitch and coal tar handling which operate at Huk Quay, Walbrzyskie Quay and Parnica Quay in Szczecin.
The new sulphuric acid terminal, opened in 2012, operates at the Katowicki Peninsula close to a bulk cargo handling area in Szczecin. Three tanks of total 33 thousand tonnes at the Katowicki Quay were built by METRACO. A company providing professional cargo handling is Bulk Cargo Port Szczecin. Ports of Szczecin and Swinoujscie also handle petroleum products. Both ports have specialized terminals operated by PKN Orlen and Baltchem.
A large development potential has also been created by building a new outer port in Swinoujscie with a platform for servicing LNG carriers.
Gdansk seaport grows in importance
On 6 November 2013, the Inspector of Construction Supervision for the Province of Pomerania, granted permission sought by the Port Polnocny Ltd company to operate the dry bulk terminal in Gdansk, Poland.
The permission includes the repairs of the Rudowy Pier, the construction of storage yards with an area of almost 100,000m2, new technological equipment, staff and workshop facilities, transformer stations, road networks and utility and service lines — taking up an area of 15.5 hectares of the most attractive port land having direct access to the deepwater regions of the Gulf of Gdansk. Consequently, Port Polnocny Ltd owned by the Belgian group SEA-INVEST is now operating on 59.2 hectares of land using two cargo piers suited to handling coal and ore, which can accommodate the largest ocean-going vessels that can navigate through the Danish Straits.
Port Polnocny (Northern Port) — the flag-ship investment project of the 1970s — came into focus of Belgian interest in 2007. Having recognized the advantage of berthing facilities for 280- metre long bulk carriers with a 15-metre draught, they acquired the majority block of voting shares of the company that was established in 1991 following the privatization of the Commercial Seaport in Gdansk. The Belgian company of SEA- INVEST, which since the inter-war period has developed its experience in 25 ports all over the world, made the right decision: Gdansk is the right choice for successive maritime investments.
The project funded by SEA-INVEST and developed on the land managed by PGA SA is in fact the closing of another investment launched by the Port of Gdansk 40 years ago. However, although the liquid fuel piers operated by the erstwhile Port Polnocny were suited to handling both export and import goods, the Weglowy Pier (coal pier) was only capable of exporting coal from Poland using the advanced and efficient technologies. It was not until now that it is possible to shift coal from vessels onto freight cars and vehicles at a rate (30,000 tonnes) similar to that of loading a ship (35,000 tonnes). This is how the situation has changed in terms of exchange of goods with Poland, which in fact had been forecast by the designers of Port Polnocny — this is the requirement that the Port of Gdansk has to meet.
The volume of goods handled by the SEA-INVEST Group in the ports across Belgium, France, the Netherlands, Germany, Africa, India, Russia and Gdansk totals more than 120 million tonnes of dry, liquid, containerized and refrigerated cargoes — ranking as the European leader in terms of port turnovers and logistics chains.
From Antwerp to Ghent, Bayonne, Bordeaux, Calais and from Caronte, Rotterdam, Abidjan to Cape Town, SEA-INVEST provides jobs to more than 6,000 people. The analysis of Gdansk port natural location shows the following advantages: facilities to accommodate the Baltmax-class ships all year round in an ice-free port, highly efficient and continuously modernized rail and road services connecting the port with Poland’s industrial hinterland and with the entire Central and Eastern Europe.
These advantages can guarantee a successful project delivery of setting up in Gdansk a distribution centre suited to handling coal, iron ore, aggregates and biomass.This is the shortest way to launching a profitable hub for dry bulk cargo in the Baltic Sea.
The current infrastructure facilities including automated defrosting and unloading of freight cars, sorting, storage and loading of bulk carriers at the Weglowy Pier has been expanded with two 75-tonne cranes which — given the support of dumping and loading machines and a conveyor system with a capacity of 4,000 tonnes per hour — are suited to unloading a ship at the Rudowy Pier using the technology and at a rate that will prove satisfactory to each and every shipping and cargo operator.
The SEA-INVEST Dry Bulk Terminal in Gdansk looks quite impressive today. The port landscape — until recently rather coarse and plain, reminding the viewer of the wartime destruction — is now changing substantially thanks to the investments of recent years. In co-operation with PGA SA, every successive business partner contributing their innovative ideas in the form of investment projects, has the guarantee of profitability and success. Consequently, they are helping Gdansk to regain its significance determined by its natural advantages centuries ago and to strengthen its position as an ocean port facility and a Baltic hub suited to handling a full range of vessels and cargoes.
Adjacent to the Naftoport Coal and Liquid Fuel Terminal and to the Deepwater Container Terminal (DCT) — the Baltic hubs that have already earned their reputation — the SEA- INVEST Dry Bulk Terminal adds to the courageous dreams of Poland’s drawing benefits from its excellent access to the sea. The announcement regarding the construction of the PERN fuel base, expanding the container throughput capacity and providing new facilities for passenger traffic, among other projects, shape the perspective presented in the port development strategy, bringing to mind the rational use of benefits derived from the direct sea access.