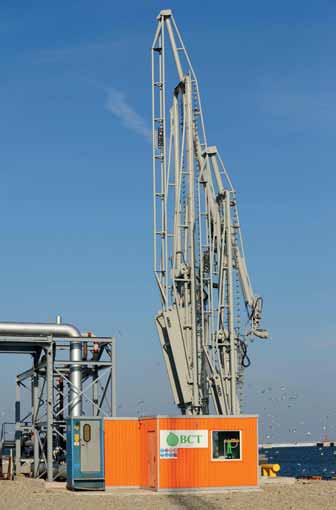
Two-thousand-and-nine is turning out to be a very productive
year for newcomer Baltic Chemical Terminal (AS BCT) in the
fertilizer transshipment business. Commercial operation started
on 9 February 2008 and in its first year the terminal handled
220,000 tonnes of liquid fertilizer. In the current year, AS BCT
will increase the volume of liquid fertilizer transshipped, and it
will also start transshipping ammonia.
The terminal is designed to handle over a million tonnes of
ammonia and a similar quantity of UAN (urea-ammonium nitrate)
solutions. Tank storage capacity is 120,000 tonnes. The terminal
is located in Estonia at the Port of Sillamae, just 23km from the
Russian border. Two deep-sea berths with depths of up to 13
metres enable the terminal to handle fertilizer from carriers of
up to Panamax size. Cargo loading/unloading is performed in the
following chain: railcar – storage tanks – vessel.
AS BCT’s highly professional workforce, and its long-term
experience in the transshipping of cargo, means that customers
benefit from high-quality services and high-tech terminal facilities.
Geographical location, as well as free zone status and the ability
to release goods into free circulation in EU member states,
means that fertilizer producers have access to high-quality
transshipment of their goods through the AS BCT terminal.
The most important event for AS BCT’s workforce as well as for its clients is the successful start-up of the new
environmentally friendly complex for ammonia transshipment.
Ammonia handling technology consists of two-phase cooling system, and starts from receiving of goods at two rail unloading areas equipped with 32 top unloading arms. Top unloading equipment balanced with spring balance cylinders, which have internal spring sets, is designed in such a way that safe operation is 100% guaranteed. Ammonia unloading speed starts from 130tph (tonnes per hour).
From the unloading areas ammonia is transferred via pipeline to a compressor room where the cooling process is performed.
The ammonia operating system is of a closed and automated type.
Liquid ammonia is stored in two storage tanks each with a capacity of 30,000 tonnes, and known as cup-in tank of the
double integrity type. The outer tank provides a vapour-tight flameproof enclosure around the primary steel container. This safety precaution is designed to prevent ammonia leakage in case of the primary container damage, and conforms to high safety requirements.
The loading of vessels is performed at loading rates of up to 1,200tph via a marine loading arm, technical parameters of which allow ammonia handling at ambient temperature from –40°C to +50°C. The manoeuvring operation of the loading arm is possible in winds of up to 22m/s. Such parameters ensure yearround operations.
The loading rate is regulated by the efficiency of the pumps used. Three ammonia pumps are available at the terminal allowing simultaneous shiploading and rail wagon unloading operations.
Unlike ammonia, the UAN solution is not flammable or explosive, which makes UAN transshipment accident-free. The
first UAN block train received in 2008 was unloaded by AS BCT’s qualified workforce using high-tech equipment in six
hours. The unloading process is performed at two rail unloading areas equipped with 32 unloading arms at the rate up to 600tph.
UAN is stored in free storage tanks with capacities of 20,000 tonnes each. Vessel loading is performed via marine loading arms, the technical parameters of which allow for UAN handling at wind speeds of up 22m/s and ambient temperature from –40°C to +50°C.
One of AS BCT’s development areas is the implementation of new modern methods of air pollution reduction. One of these is the operation of a propane flare, which was designed and installed in compliance with high environmental standards. The function of this equipment is to burn excessive ammonia gases improving ammonia transshipment safety.